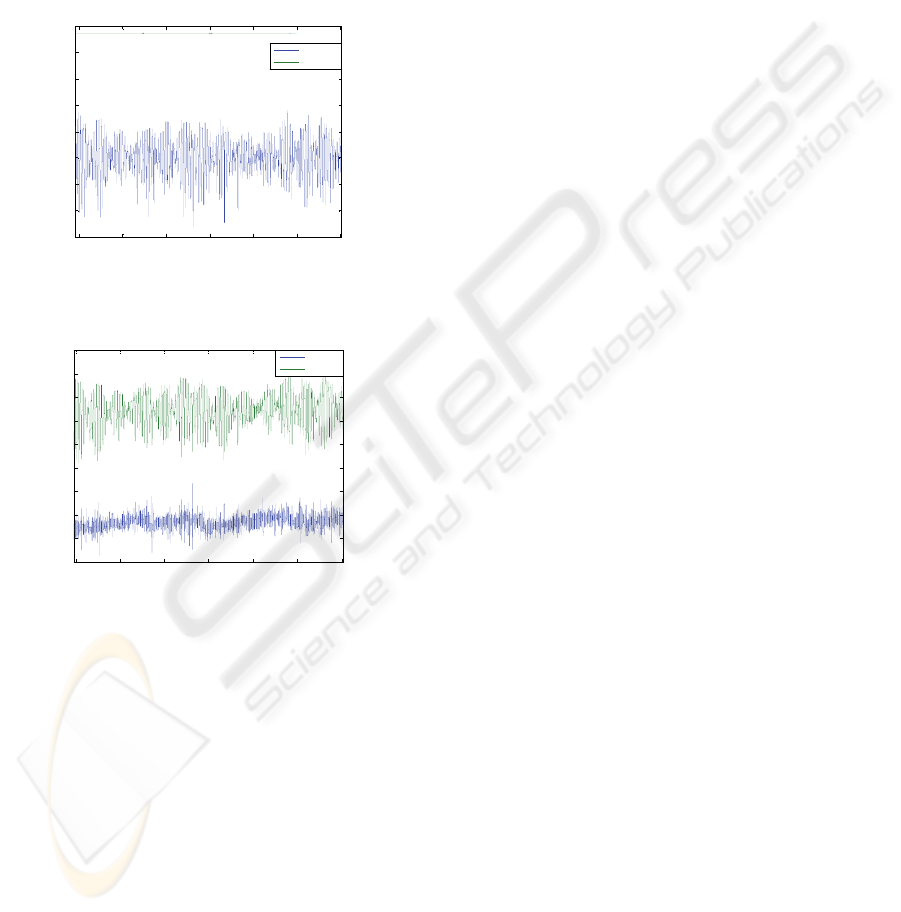
expected without clogging. Thus this estimation by
means of an observer, which may be useful for
control purposes, also helps to quantify the intensity
of the clogging phenomenon.
The observer, tuned as previously, is now
applied to a second experiment (record 2). In this
case, three frequencies of the signal
bulge
d
have to
be considered, respectively 0.084, 0.095 and
0.082 Hz as the most significant in the bulging
frequency range [0.05, 0.15] Hz.
400 600 800 1000 1200 1400 1600
-6
-4
-2
0
2
4
6
8
10
Flow out (l/s)
d-bulge
Qout-ideal
Figure 8: Comparison between the estimate
bulge
d and
idealout
Q
_
in the case of the second record.
400 600 800 1000 1200 1400 1600
10
12
14
16
18
20
22
24
26
28
Flow in (l/s)
d-clog
Qin-ideal
Figure 9: Comparison between the estimated
clog
d and
idealin
Q
_
in the case of the second record.
Figures 8 and 9 show the estimated disturbances
bulge
d and
clog
d . Figure 9 compares the estimation
of
clog
d to
idealin
Q
_
. Without ramp in
clog
d , it can
be concluded that
clog
d only represents the average
of the
bulge
d signal of Figure 8 which should be
added to it in order to estimate its correct value, and
that there is no clogging effect in this record. From a
control point of view as described in (Furtmueller
et
al
., 2005), to have the average of
bulge
d included in
clog
d is not problematic. In fact, the control
structure which compensates disturbances should
use the sum of
clog
d and
bulge
d as an input and not
the two disturbance estimations separately.
5 CONCLUSIONS
This paper presents the elaboration of a global
observer designed to estimate clogging and bulging
disturbances appearing in a continuous casting
process. These estimations may be further used as
inputs to compensation modules within mold level
control structures. This observer is built with
behavioral models of the physical process, assuming
that these disturbances can be modelled as
exogenous signals. Further research may consider a
nonlinear nozzle gain to model the clogging effect,
robustness analysis of the estimator, particularly
with respect to variations of the bulging signal
frequencies and model uncertainties.
REFERENCES
Thomas, B.G., Bai, H., 2001. Tundish nozzle clogging –
application of computational models. In
18
rd
PTD
Conf. Proc.
, Baltimore (US).
Sontag, E., 1998.
Mathematical Control Theory:
Deterministic Finite Dimensional Systems
, Springer.
2
nd
edition.
Yoon, U-S., Bang, I.-W., Rhee, J.H., Kim, S.-Y., Lee, J.-
D., Oh, K.H., 2002. Analysis of mold level hunching
by unsteady bulging during thin slab casting. ISIJ
International, 42(10):1103-1111.
Lee, J.D., Yim, C.H., 2000. The mechanism of unsteady
bulging and its analysis with the finite element method
for continuously cast steel. ISIJ International,
40(8):765-770.
Dussud, M., Galichet, S., Foulloy L.P., 1998. Application
of fuzzy logic control for continuous casting mold
level control.
IEEE Transactions on Control Systems
Technology
, 6(2).
Furtmueller, C., Gruenbacher, E., 2006. Suppression of
periodic disturbances in continuous casting using an
internal model predictor. In
Proc. IEEE Intl. Conf. on
Control Applications
, Munich, Germany.
Furtmueller, C., Del Re, L., Bramerdorfer, H., Moerwald,
K., 2005. Periodic disturbance suppression in a steel
plant with unstable internal feedback and delay. In
Proc. 5
th
Intl. Conf. on Tech. and Automation, Greece.
Time (s)
Time (s)
ICINCO 2008 - International Conference on Informatics in Control, Automation and Robotics
124