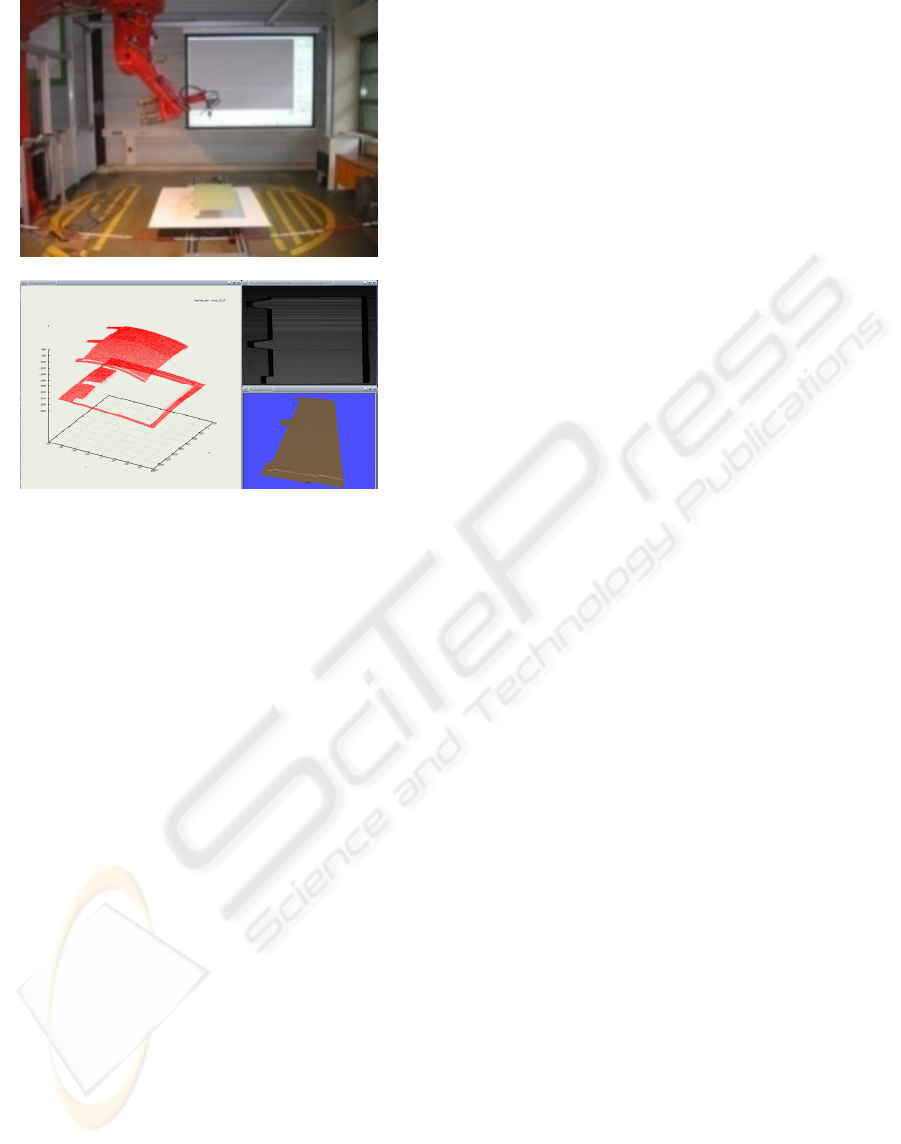
Figure 6: A split-beam technique captures the structure of
a 3D object (upper part) and translates it into a graphic
model (lower part).
By using the proposed, robot-based concepts of
multiple sensor quality monitoring, the customary
use of expensive 3D CAD-models of the test objects
for high-precision CNC controlled machine tools or
coordinate inspection machines becomes, in most
instances, unnecessary.
An intelligent, sensor-based distance-control
concept (Visual-Servoing-Principle) accurately
controls the robot’s movements with regard to the
work piece and prevents possible collisions with
unexpected obstacles.
6 CONCLUSIONS AND FUTURE
WORK
A development and demonstration platform (DDP)
for flexible inline quality monitoring using picture-
giving sensors was created.
The primary goal of the DDP is to investigate,
optimize and demonstrate to potential cooperation
partners how the system can be applied to reduce
effort and to increase flexibility. For example, it can
be used in the robot-based coordination of short- and
wide-range monitoring, for the introduction of
learning-capable evaluation processes, as a tool for
visualizing results and for user interaction, as well as
for the flexible networking and integration of
various wide- and short-range sensors.
Further inspection sensors, which are based on
another measurement principle, will be developed
soon on the sensor magazine and made available for
the surface testing. Investigations and pre-
developments for further (complex) applications can
be realized with the platform at small expenditure.
The applications for example can look like:
• The surface inspection of the outside and the
structural examination of the inside of a car
door;
• The crawler-type vehicle order supervision
within the range of a car window.
ACKNOWLEDGEMENTS
This research was supported by the „Fraunhofer-
Gesellschaft zur angewandten Forschung e.V.“
internal Program.
REFERENCES
Applegate, D. L., Bixby, R. E., Chvátal, V., Cook, W. J.,
(2006). The Traveling Salesman Problem: A
Computational Study. Princeton University Press.
ISBN 978-0-691-12993-8.
Deutscher, R., Munser, R., Hartrumpf M., (2003).
Detection and Measurement of Damages in Sewer
Pipes with a 3D-structured Light Projection Sensor,
In: tm - Technisches Messen 70, 2003(07):338-345.
Lawler, E. L., Lenstra, J. K., Rinnooy Kan, A. H. G.,
Shmoys, D. B., (1985). The Travelling Salesman
Problem. A Guided Tour of Combinatorial
Optimization. Wiley, Chichester 1985. ISBN 0-471-
90413-9.
Müller, Th., (2001). Modellbasierte Lokalisation und
Verfolgung für sichtsystemgestützte Regelungen,
Dissertation an der Universität Karlsruhe (TH), 8.
Februar 2001.
Pope, A. R., Lowe, D. G., (2000). Probabilistic Models of
Appearance for 3D Object Recognition. International
Journal of Computer Vision, 40(2):149–167.
Sung, C.-K., Kuntze, H-B., (2006). Flexible roboter-
basierte Qualitätsüberwachung mit bildgebenden
Sensoren, Sensor Magazin, Magazin Verlag Hightech
Publications KG, Bad Nenndorf, 2006(3):24-26.
Veltkamp, R.C., Hagedoorn, M., (2001). State-of-the-art
in shape matching. In M. Lew (Ed.), Principles of
Visual Information Retrieval, Springer.
FLEXIBLE ROBOT-BASED INLINE QUALITY MONITORING USING PICTURE-GIVING SENSORS
301