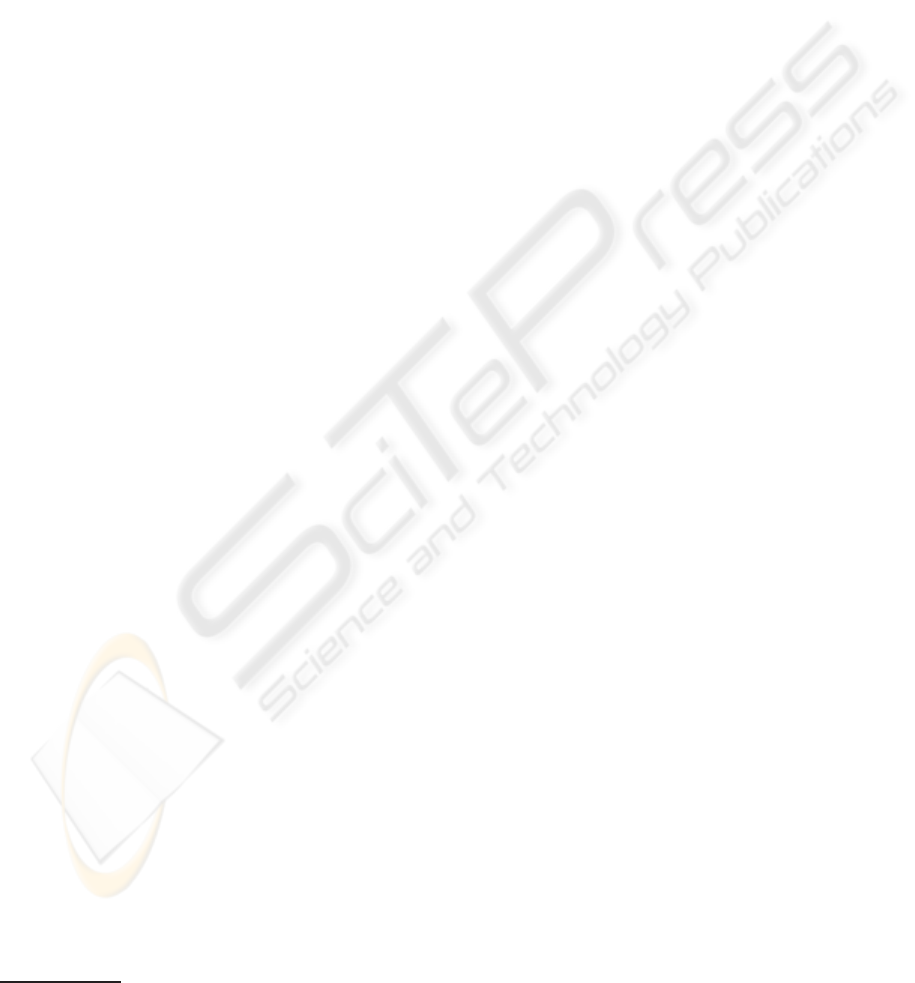
SENSOR AND ACTUATOR FAULT ANALYSIS IN ACTIVE
SUSPENSION IN VIEW OF FAULT-TOLERANT CONTROL
Claudio Urrea and Marcela Jamett
Departamento de Ingeniera El´ectrica, Av. Ecuador 3519, Est. Central, Santiago, Chile
Keywords:
Active suspension, sensor and actuator faults, full-vehicle suspension model.
Abstract:
This paper shows the first step of a fault tolerant control system (FTCS) to control active suspension on a
full-car suspension model. In this paper, the elimination of the inevitable pitch and roll actions of a spring
suspension between each axle and the body of a vehicle is studied. An actuator (linear motor) producing an
electromagnetic force and a pneumatic force acting simultaneously on the same output element is used. This
linear motor acts as a force generator that compensates instantly for the disturbing effects of the road surface.
Simulation results to illustrate the system’s performance in front of the occurrence of sensor and actuator faults
are shown.
1 INTRODUCTION
Vehicle suspension systems have developed over the
last 100 years to a very high level of sophistication
(Buckner, Schuetze, and Beno, 2000; Fukao, Ya-
mawaki, and Adachi, 2000). Most vehicle today use
a passive suspension system employing some type of
springs in combination with hydraulic or pneumatic
shock absorbers, and linkages with tailored flexibility
in various directions. These suspension system de-
signs are mostly based on ride analysis.
Traditionally automotive suspension designs have
been a compromise between the three conflicting cri-
teria of road holding, load carrying and passenger
comfort. In fact, despite the wide range of designs
currently available by using passive components, we
can only offer a compromise between these conflict-
ing criteria by providing spring and damping coeffi-
cients with fixed rates
1
.
On the other hand, active suspensions have been
extensively studied in the last three decades (Giua,
Seatzu, and Usai, 2000; Lefebvre, Chevrel,and
Richard, 2001; Lakehal-Ayat, Diop, and Fe-
naux,2002). In an active suspension the interaction
between vehicle body and wheel is regulated by an
actuator of variable length capable of supplying the
entire control force system’s requirements.
Ride comfort in ground vehicles usually depends
1
Components for passive suspension can only store and
dissipate energy in a pre-determined manner.
on a combination of vertical motion (heave) and an-
gular motion (pitch and roll). Active suspension is
characterized by a built-in actuator which can gen-
erate control forces to suppress the above mentioned
roll and pitch motions.
Including the dynamics of the hydraulic system
consisting of fluids, valves, pumps, etc., complicates
the active suspension control problem even further
since it introduces nonlinearities to the system. It
has been noted that the hydraulic dynamics and fast
servo-valve dynamics make controls design very dif-
ficult (Karlsson, Teely, and Hrovatz, 2001; Alleyne,
and Hedrick, 1995). The actuator dynamics signif-
icantly change the vibrational characteristics of the
vehicle system (Engelman, and Rizzon, 1993). Us-
ing a force control loop to compensate for the hy-
draulic dynamics can destabilize the system (Alleyne,
Liu, and Wright, 1998). This full nonlinear control
problem of active suspensions has been investigated
using several approaches including optimal control
based on a linearized model (Engelman, and Riz-
zon, 1993), adaptive nonlinear control (Alleyne, and
Hedrick, 1995), and adaptive control using backstep-
ping (Karlsson, Teely, and Hrovatz, 2001). These
schemes use linear approximations for the hydraulic
dynamics or they neglect the servo-valve model dy-
namics in which a current or voltage is what ulti-
mately controls the opening of the valve to allow flow
of hydraulic fluid to or from the suspension system.
However, nowadays a novel family of highly dynamic
electro-magnetic direct drives exit, i.e. servomotors
179
Urrea C. and Jamett M. (2008).
SENSOR AND ACTUATOR FAULT ANALYSIS IN ACTIVE SUSPENSION IN VIEW OF FAULT-TOLERANT CONTROL.
In Proceedings of the Fifth International Conference on Informatics in Control, Automation and Robotics - ICSO, pages 179-186
DOI: 10.5220/0001490201790186
Copyright
c
SciTePress