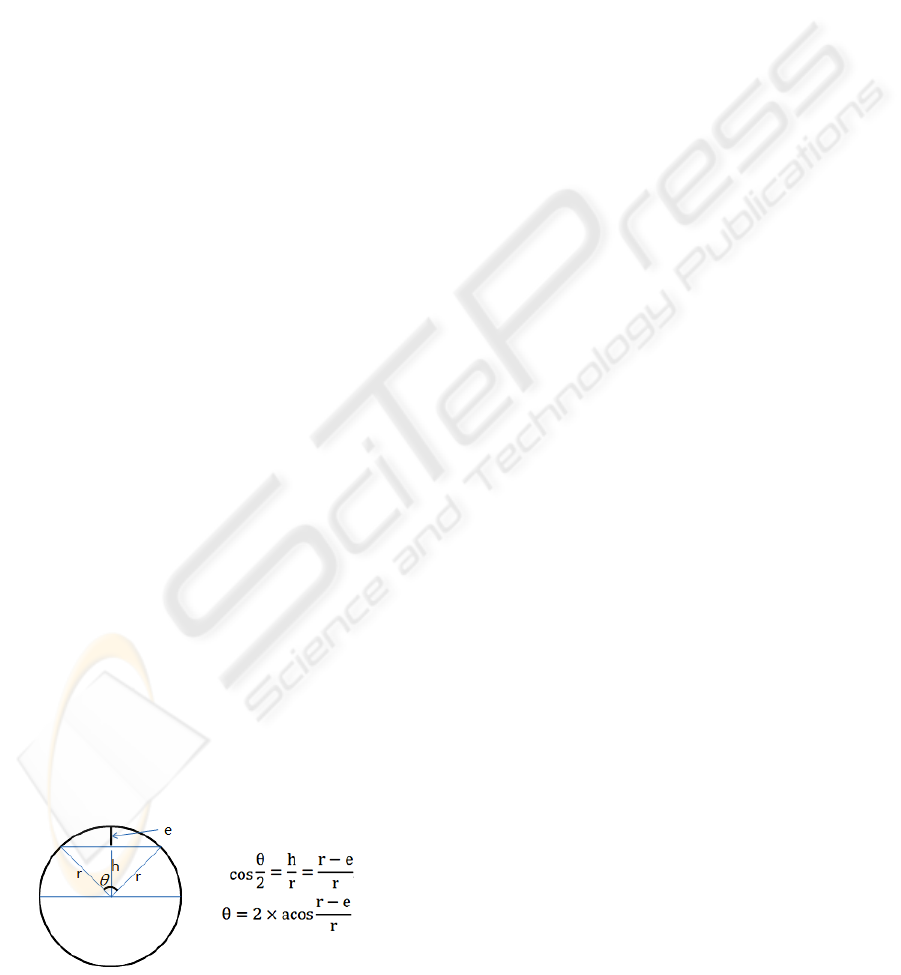
5) It contains inner part data :
In many cases, device CAD model data
contains invisible inner part data, which are
not necessary for simulation purpose.
2.2.2 Workpiece CAD Model
In many cases, workpieces have lots of curved
surface. For car assembly line, almost every
workpieces have smooth surface, like body, side,
door, hood, fender etc. The CAD model for this
workpieces are far more bigger than that of the
device CAD model, because it represents smooth
surface using triangular mesh. Typically, CAD
model for car door exceeds some hundreds mega-
bytes, while the size of device CAD model for
robots is some mega-bytes.
Due to the different characteristics, we apply
different methods to reduce the size of CAD model.
2.3 Reducing Device CAD Model Size
After converted by various software, the structural
information for the geometry data can be lost. This
makes it difficult to go further processing for
geometry handling. However, it is relatively easier
to detect geometric features from device CAD model
rather than workpiece CAD model.
We used the geometric features extracted from
device CAD model to reduce data size.
2.3.1 Replacing the Primitives
In many cases, the device CAD model contains lots
of primitives like cylinder, sphere etc. For replacing
cylinders, we assume that a n-side cylinder
representation in the CAD model is an
approximation of the pure logical cylinder which has
infinitely large n.
A cylinder consists of top, bottom and n-side faces,
where n ≥ 3. A cylinder with n-side consists of 4n-4
triangles. A cylinder contained in the device CAD
model typically has large n value. By detecting this
cylinder geometry and reducing the n, we can reduce
the size of data.
Figure 2: Calculation of n-side for cylinder.
Figure 2 shows how many number of cylinder
sides we can reduce, when the final error tolerance e
for simulation data is given. Using the radius r of the
pure logical cylinder and error tolerance e, we can
calculate maximum θ for reduced cylinder. The
reduced cylinder has 360/θ side faces.
Though this method is quite effective, it is
difficult to apply in real situation, because it is hard
to identify cylinder geometry from unstructured
triangular meshes. For sphere, it is more difficult to
identify. So this method is only applicable when the
CAD data contains structural information and we
can identify them.
Another problem for this method is after
replacing into the simple geometry, some parts
attached to the original cylinder side surface can be
dangling on a replaced cylinder.
2.3.2 Removing Small Parts
The device CAD model contains lots of small
components needed for part assembly. Small bolts
and nuts are one of those things. If these parts are so
small that the size is less than the error tolerance for
the simulation, we can safely remove them.
But in this case, it is not always possible to
identify small parts from unstructured triangular
meshes.
2.3.3 Removing Small Holes
The effect of removing holes from the geometry is
quite potential. A cube without hole can be
represented with 12 triangles, while a cube with one
hole of n side needs 4n + 8 triangles. (n+4 for top,
n+4 for bottom, 2n for side) If a hole is consists of
20 sides, the number of triangles reaches 4*20+8 =
88, which is more than 7 times of 12. If number of
holes increases, the number of triangles increases
rapidly.
The hole removing algorithm is difficult to
implement, because it is not always possible to
identify holes from unstructured meshes. For this
reason, first we detect small inner circle from a
surface. It is relatively easy to implement even if we
don’t have structural information.
Step 1: Group faces which exists in a same plane.
That means, the faces has the same plane equation,
and they are inter-connected.
Step 2: merge the grouped faces
Step 3: Trace boundary edges from the merged
face
Step 4: Identify outmost boundary edges
Step 5: Using the boundary edges, re-triangulate
the surface.
ICINCO 2008 - International Conference on Informatics in Control, Automation and Robotics
96