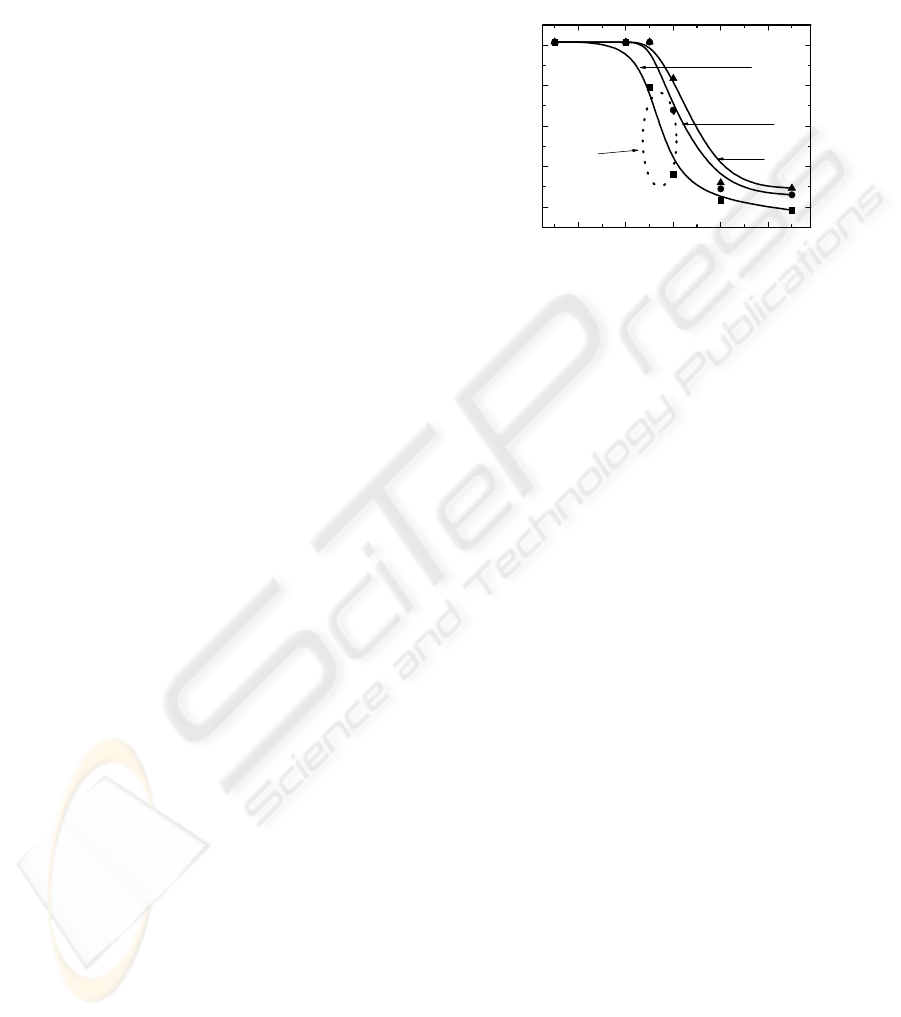
to mechanical deformation and change of nano-scale
electrical properties. An attempt to use the strain
sensing capability of single-wall carbon nano-tubes
(SWCNT) on the nano-scale level in a macro-scale
strain sensor was made by Dharap et al.. We present
in this paper an attempt to use the multi-wall carbon
nano-tubes (MWCNT) to devise a flexible
composite for macro-scale pressure indicators
(relative pressure difference sensors) or robotic
tactile elements.
2 DESIGN PRINCIPLES OF THE
STRUCTURE OF MATERIALS
On the basis of the results of other authors (Aneli,
1999; Zhang, 2000; Das, 2002; Job, 2003) we have
developed the following principles designing the
structure of materials to obtain most sensitive
multifunctional elastomer–carbon nano-composites:
1) Polyisoprene (natural rubber) of the best
elastic properties has to be chosen as the matrix
material;
2) High-structured carbon nano-particles (HSNP)
providing a fine branching structure and a large
surface area (better adhesion to polymer chains
compared to LSNP) should be taken as the filler.
Because of a higher mobility of HSNP compared
with LSNP the electro-conductive network in the
elastomer matrix in this case is easily destroyed by
very small tensile or compressive strain. We suppose
this feature makes the elastomer–HSNP composite
an option for more sensitive tactile elements in
robots.
3) The highest sensitivity is expected in the
percolation region of a relaxed polyisoprene
composite. The smallest mechanical strain or
swelling of the composite matrix remarkably and
reversibly increases resistance of such a composite.
From the thermodynamic point of view the sensing
of strain is based on the shift of percolation
threshold, for example, under tensile strain as shown
in Figure 1 (Knite, 2002; Knite, 2004).
As seen from Fig. 1, the shift of the percolation
threshold at less than 30% strain changes electric
resistance of the composite with 10 mass parts of
HSNP filler more than 10
4
times. The highest strain
sensitivity is expected in the percolation region (9-
10 mass parts of the HSNP filler) of a relaxed PNC
composite. Thus, the maximum sensitivity of PNC
composite materials to thermodynamic forces is
supposed to occur near the percolation threshold of
electric conductivity.
To obtain completely flexible tactile sensing
elements of large area (relative to rigid piezoelectric
sensors) a layer of the active PNC composite is fixed
between two conductive rubber electrodes by means
of a special conductive rubber glue.
6 8 10 12 14
4
6
8
10
12
The maximum
sensitivity
region
lgR, Ω
Carbon black, mass parts
streched 30%
streched 40%
relaxed
Figure 1: Shift of the percolation threshold in polyisoprene
– high-structured carbon nano-particle composite under
tensile strain (Knite, 2002; Knite, 2004).
3 PREPARATION OF SAMPLES
AND ORGANISATION OF THE
EXPERIMENT
The polyisoprene – nano-structured carbon black
(PNCB) composite was made by rolling high-
structured PRINTEX XE2 (DEGUSSA AG) nano-
size carbon black and necessary additional
ingredients – sulphur and zinc oxide – into a Thick
Pale Crepe No9 Extra polyisoprene (MARDEC,
Inc.) matrix and vulcanizing under 30 atm pressure
at 150 ˚C for 15 min. The mean particle size of
PRINTEX XE2 is 30 nm, DBP absorption – 380
ml/100 g, and the BET surface area – 950 m
2
/g.
The polyisprene – carbon nanotube (PCNT)
composites containing dispersed multi-wall carbon
nanotubes (MWCNT) were prepared as follows. The
size of MWCNT: OD = 60-100 nm, ID = 5-10 nm,
length = 0.5-500 μm, BET surface area: 40-
300 m
2
/g. To increase the nano-particles mobility
and to obtain a better dispersion of the nano-
particles within the matrix the matrix was treated
with chloroform. The prepared matrix was allowed
to swell for ~ 24 h. The MWCNT granules were
carefully grinded with a small amount of solvent in a
china pestle before adding to the polyisoprene
matrix. Solution of the polyisoprene matrix and the
concentrated product of nano-size carbon black was
mixed with small glass beads in a blender at room
temperature for 15 min. The product was poured into
a little aluminum foil box and let to stand for ~ 24 h,
PROSPECTIVE ROBOTIC TACTILE SENSORS - Elastomer-Carbon Nanostructure Composites as Prospective Materials
for Flexible Robotic Tactile Sensors
235