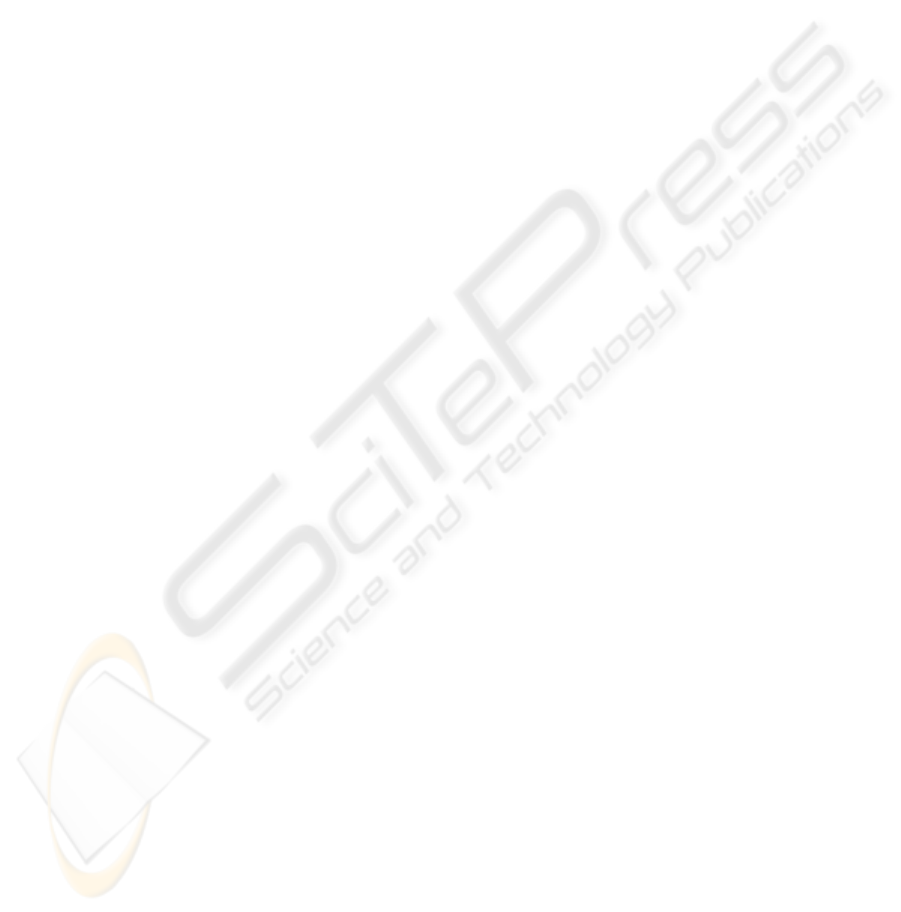
4.2.2 Simulation of a Virtual Sensor
The tuned simulation can function as a virtual
sensor, also called a soft sensor. The integrated
history of the sheet surface temperature as measured
directly by infrared sensors with the heat transfer
simulation to predict the sheet internal temperature
and to indicate the time required for adequate sheet
heating inside the oven.
One of the main outputs of the simulation is the
predicted heating curve for the material for a
constant heat flux (Equation (2)) shown in Figure 6.
From this, the system can control the heat flux by
controlling the heating element input power, which
results in a given temperature at a given depth at
time t in the material.
4.2.3 Adjusting the Time Frames of the
Different Modules
Unfortunately, the time frame of such a simulation is
orders of magnitude greater than what is needed to
control the thermoforming process in real time. This
problem is solved by generating the sensitivity
matrix of the simulation every time the simulation is
updated. For example, the heat flux in equation (3)
can be generated from the tuned simulation.
Equations (2, 3) are used to predict the sheet
temperatures at different depths for different sheet
zones for the time sequenced trajectories of the
heating element energy input allowing for heat flux
control as shown in Figure 5.
Since the simulation is reasonably accurate, the
control system only needs to apply the updated
parameters in the vicinity of the initial prediction for
the calculated operating point, which allows the use
of linear interpolations to adjust the operating point
as required, thus achieving a very fast response time.
4.3 Agent based Control
An intelligent agent based system is a loosely
coupled network of problem solving entities (agents)
that work together to find the answer to problems
that are beyond the individual capabilities or
knowledge of each entity (Florez-Mendez, 1999).
An agent based system was chosen for model based
control since it can deal well with multiple
submodels and data streams, and can cope with
submodels that are very different in size and that
operate on dissimilar time scales. These features
make agent technology especially suited for building
control systems based on models of processes,
where the processes are very complex and many
process and material parameters are dynamic.
All agents in the architecture operate
independently and asynchronously. The control
agent acquires sensor data from the physical layer
and sends control parameters as they become
available. Similarly, the process agents retrieve
sensor data and calculate state variables. The
retrieval of sensor data and the calculation of state
variables are interrupt driven based on detected
variations from previous states; thus, calculations are
only launched when needed and with the best
information available. This design minimizes control
cycle time while allowing data to flow
asynchronously and implements just in time delivery
of the different data streams, while still setting
control parameters with complex, but validated
parameters. The result is that during a short
production period certain parameters are updated
infrequently. This is not a problem, since they do not
highly impact the operating point of the process.
This architecture allows many processes to be
controlled in-cycle, i.e., while a part is being made
so that near perfect parts can be made every time. If
the process is very fast or parameters cannot be
measured during part manufacture, cycle-to-cycle
control can be done, i.e., parameters measured
during or after a part is being made are used to
control the next part being manufactured.
Control can be done with a single processor, if
the amount of computation is small. Nevertheless,
for a complex process like thermoforming, the
amount of calculation for process models tends to be
large and distributed over different time frames;
therefore, multiple processors may be required
depending on the complexity of the heating process.
With multiple processors, the control system can
dynamically allocate the execution of different
agents to different processors. Due to the
asynchronous operation of the architecture,
processes can be optimally controlled for submodel
execution times from milliseconds to hours.
5 PARAMETERS IDENTIFIED
ON-LINE
If the agent in charge decides that the drift or
variation of the parameter warrants an adjustment of
the simulator, parameters are changed and the
simulation is then re-run and the control models
regenerated. For the thermoforming process, the
following parameters are continuously monitored in
real time.
ICINCO 2008 - International Conference on Informatics in Control, Automation and Robotics
58