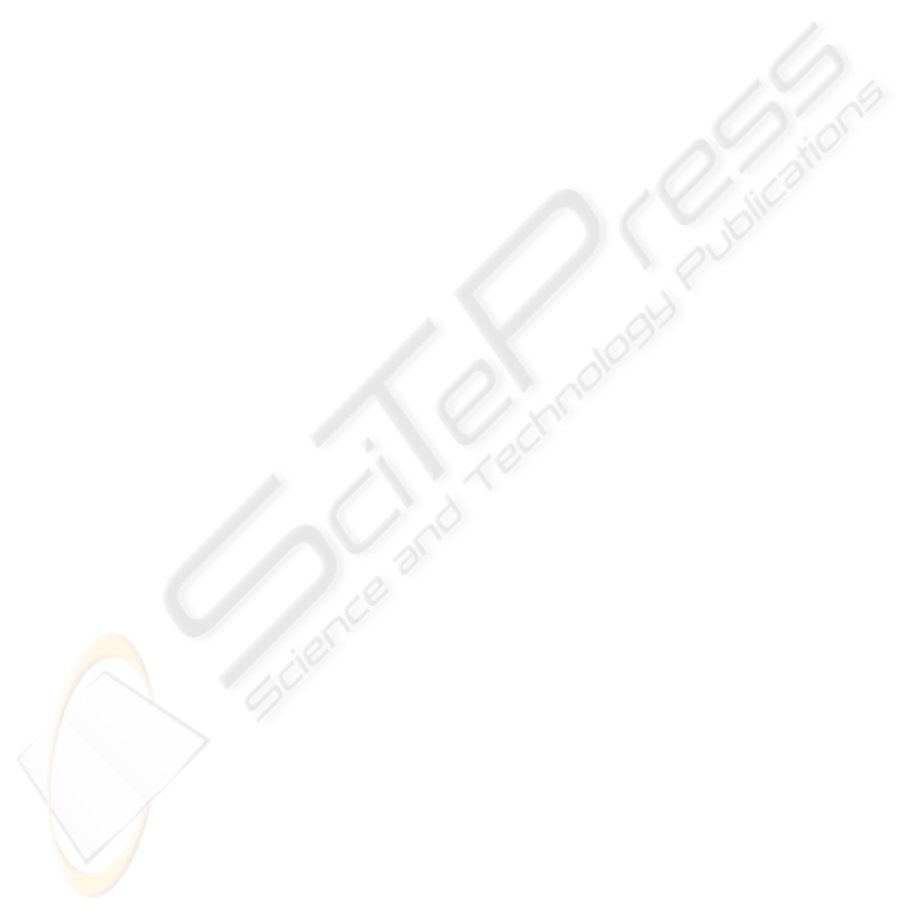
IG
i
be a task group consisting of task i and all its
predecessors (excluded from U set).
STEP 1. If U = empty, go to step 5, otherwise,
assign starting task from U.
STEP 2. Identify IG
i
. Check if it contains tasks with
both left and right preference operation direction,
then remove task i.
STEP 3. Assign operation direction Side{ IG
i
} of
group IG
i
. If IG
i
has R-task (L-task ), set the
operation direction to right (left). Otherwise, apply
so called direction rules DR.
STEP 4. If the last task i in IG
i
is completed within
cycle time, the IG
i
is added to Final set of
candidates FS(i). Otherwise, exclude task i from IG
i
and go to step 1.
STEP 5. For every task group in FS(i), remove it
from FS if it is contained within another task group
of FS.
The resulting task groups become candidates for the
mated-station.
FS = {(1,4), (2,3,5,8)}.
3.2 Groups Assignment
The candidates are produced by procedures
presented in the previous section, which claim to not
violate precedence, operation direction restrictions,
and what’s more it exerts on groups to be completed
within preliminary determined cycle time. Though,
all of candidates may be assigned equally, the only
one group may be chosen. Which group it will be –
for this purpose the rules helpful in making decision,
will be defined and explained below:
AR 1. Choose the task group FS(i) that may start at
the earliest time.
AR 2. Choose the task group FS(i) that involves the
minimum delay.
AR 3. Choose the task group FS(i) that has the
maximum processing time.
In theory, for better understanding, we will consider
a left and right side of mated – station, with some
tasks already allocated to both sides. In order to
achieve well balanced station, the AR 1 is applied,
cause the unbalanced station is stated as the one
which would probably involve more delay in future
assignment. This is the reason, why minimization
number of stations is not the only goal, there are also
indirect ones, such as reduction of unavoidable
delay. This rule gives higher priority to the station,
where less tasks are allocated. If ties occurs, the AR
2 is executed, which chooses the group with the least
amount of delay among the considered ones. This
rule may also result in tie. The last one, points at
relating work within individual station group by
choosing group of task with highest processing time.
For the third rule the tie situation is impossible to
obtain, because of random selection of tasks. The
implementation of above rules is strict and easy
except the second one. Shortly speaking, second rule
is based on the test, which checks each task
consecutively, coming from candidates group FS(i)
– in order to see if one of its predecessors have
already been allocated to station. If it has, the
difference between starting time of considered task
and finished time of its predecessor allocated to
companion station is calculated. The result should be
positive, otherwise time delay occurs.
3.3 Final Procedures
Having rules for initial grouping and assigning tasks
described in previous sections, we may proceed to
formulate formal procedure of solving two – sided
assembly line balancing problem (Kim et. al, 2005).
Let us denote companion stations as j and j’,
D(i) – the amount of delay,
Time(i) – total processing time (Time{FS(i)}),
S(j) – start time at station j,
STEP 1. Set up j = 1, j’ = j + 1, S(j) = S(j’) = 0, U –
the set of tasks to be assigned.
STEP 2. Start procedure of group creating (3.2),
which identifies
FS = {FS(1), FS(2), …, FS(n)}. If FS = ∅, go to
step 6.
STEP 3. For every FS(i), i = 1,2, … , n – compute
D(i) and Time(i).
STEP 4. Identify one task group FS(i), using AR
rules in Section 3.3
STEP 5. Assign FS(i) to a station j (j’) according to
its operation direction, and update S(j) = S(j) +
Time(i) + D(i). U = U – {FS(i)}, and go to STEP 2.
STEP 6. If U
≠
∅, set j = j’ + 1, j’ = j + 1, S(j) =
S(j’) = 0, and go to STEP 2, Otherwise, stop the
procedure.
4 MEASURES OF FINAL
RESULTS OF ASSEMBLY LINE
BALANCING PROBLEM
Some measures of solution quality have appeared in
line balancing problem. Below are presented three of
them (Scholl, 1998).
Line efficiency (LE) shows the percentage
utilization of the line. It is expressed as ratio of total
station time to the cycle time multiplied by the
number of workstations:
ICINCO 2008 - International Conference on Informatics in Control, Automation and Robotics
234