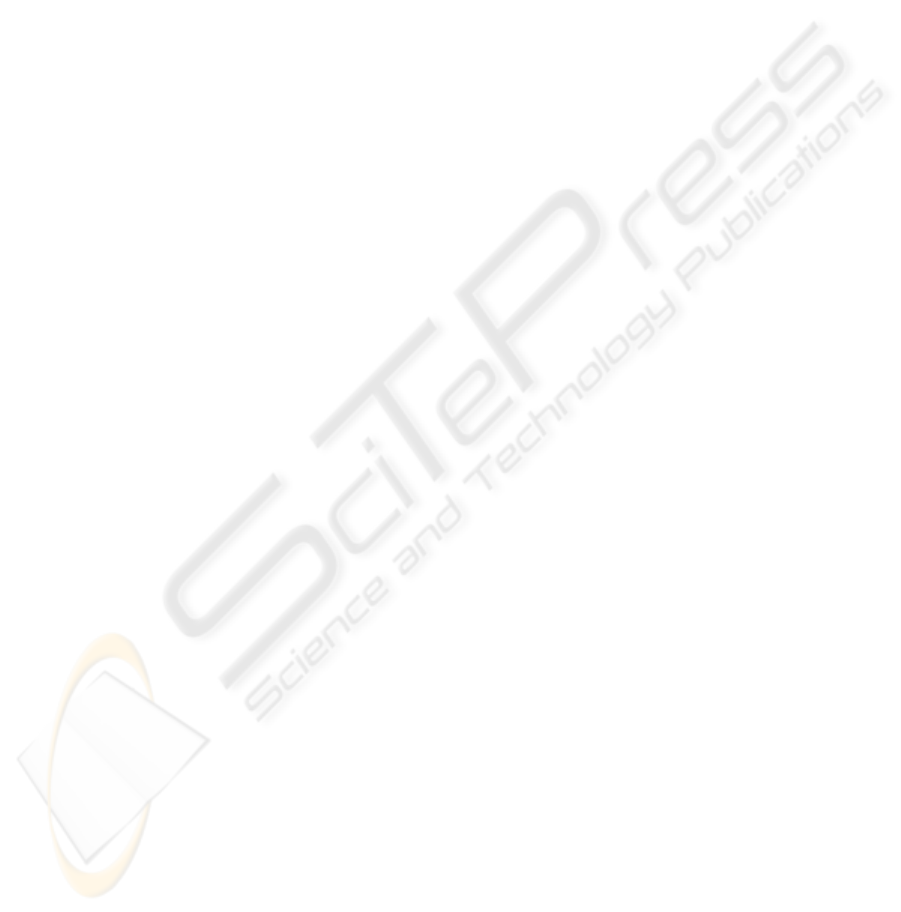
6 CONCLUSIONS
Modeling and simulation are important and essential
stages in the engineering design and problem solving
process because it allows to prevent the risks and to
lower the costs that appear with the design,
construction and testing stage of a new robot. Since
parallel mechanisms have a complex structure, using
the proposed approached of modeling and
simulation will lead to an increased efficiency in
developing new structures.
In the paper the modelling and simulation of the
PARAMIS new parallel robot is presented. The
simulations results obtained with the developed
simulation system for parallel robots allow a
structure verification before a parallel robot is built.
The developed simulation system for the parallel
robots offer multiple advantages: modularity of the
simulation system for parallel robots; friendly
graphical user interface of the simulation system;
possibility for parallel structure parameterization;
possibility to generalize some parallel structures;
Identification of singularities; possibility to identify
the optimal working zone; workspace generation:
the structures verification before a parallel robot is
built.
In this case, the contribution is the use a virtual
reality definition system to create the virtual objects
(bodies) that includes shape, dimensions, mass and
center of mass, surface characteristics and the
deviations from these characteristics may be also
considered. Between the virtual objects are defined
the appropriate structure joints. The type of joint,
their constructive dimensions, together with the
actuating define the motion restrictions that are
encapsulated within the subassemblies.
Over the predefined virtual structure is applied
the kinematic model using a programming interface
in Visual Basic ensuring the PTP or the path control
motion.
The presented simulation system enables the
motion visualization, enabling to introduce the
kinematic model over the virtual robot the single
foreseen limit being the hardware computing
capacity. The introduction of extra conditions related
to any element, joint or overall behavior of the robot
is possible with a small number of actions. The up-
to-date results validated the solution creating the
premises for the next step, the construction of the
experimental model for the PARAMIS robot.
ACKNOWLEDGEMENTS
This research was financed from the research grants
awarded by the Romanian Ministry of Education and
Research and the “Institutional Academic
Cooperation Research Grant” between the Technical
University of Braunschweig, Germany and the
Technical University of Cluj-Napoca, Romania,
awarded by Alexander von Humboldt foundation.
REFERENCES
Foley, van, D., Dam, A., Feiner, K.S., Hughes, F.J., 1990.
Computer Graphics Principles and Practice. Addison-
Wesley Publishing Company, 2
nd
edition.
Pisla, D., 2001. Graphical Simulation of the Industrial
Robots. Todesco Publishing House.
Ben-Porat, O., Shoham, M., Meyer, J., 2000. Control
Design and Task Performance in Endoscopic
Teleoperation, Presence. Massachusetts Institute of
Technology, 9, 3, 256-267.
Glozman, D., Shoham, M., Ficher, A., 2001. A Surface-
Matching Technique for Robot-Assisted Registration,
Computer Aided Surgery 6, 259-269.
Grace, K. W., Colgate, J. E., Glucksberg, M. R., Chun,
J.H., 1993. A Six Degree of Freedom
Micromanipulator for Ophthalmic Surgery. In Proc. of
IEEE International Conference on Robotics and
Automation, 630-635.
Brown University, Division of Biology and Medicine,
2005.
Pisla, D., Stan, S., New Approaches Regarding the
Modelling and Simulation of Parallel Robots. In Proc.
of the 2nd International Conference on Robotics,
Robotica-2004, Intergraf Reşiţa Publishing House,
151-152.
Plitea, N., Hesselbach, J., Vaida, C., Raatz, A., Pisla, D.,
Budde, C., Vlad, L., Burisch, A., Senner, R., 2007.
Innovative development of surgical parallel robots,
Acta Electronica, Mediamira Science, Cluj-Napoca,
201-206.
Merlet, J-P., 2005. Parallel Robots, 2nd Edition, Kluwer,
Dordrecht.
Sefrioui, J., C.M. Gosselin,, 1992. Singularity Analysis
and Representation of Planar Parallel Manipulators,
Robotics and Autonomous Systems 10, 209-224.
Park, F.C., Kim, J.W., 1999. Singularity Analysis of
Closed Kinematic Chains, ASME Journal of
Mechanical Design 121, 32-38.
Romdahne, L., Affi, Z., Fayet, M. 2002. Design and
Singularity Analysis of a 3–Translational-DOF In-
Parallel Manipulator, Journal of Mechanical Design,
ASME 124, 419-426.
Pisla, D., Pisla, A., 2001. Effiziente dynamische
Rechnersimulation für Parallelroboter, ZAMM, vol.
81, Suppl 5, 277-278.
Pisla, D., 2005. Kinematic and dynamic modeling of
parallel robots, Dacia House, (published in
Romanian), Cluj-Napoca.
MODELING AND SIMULATION OF A NEW PARALLEL ROBOT USED IN MINIMALLY INVASIVE SURGERY
201