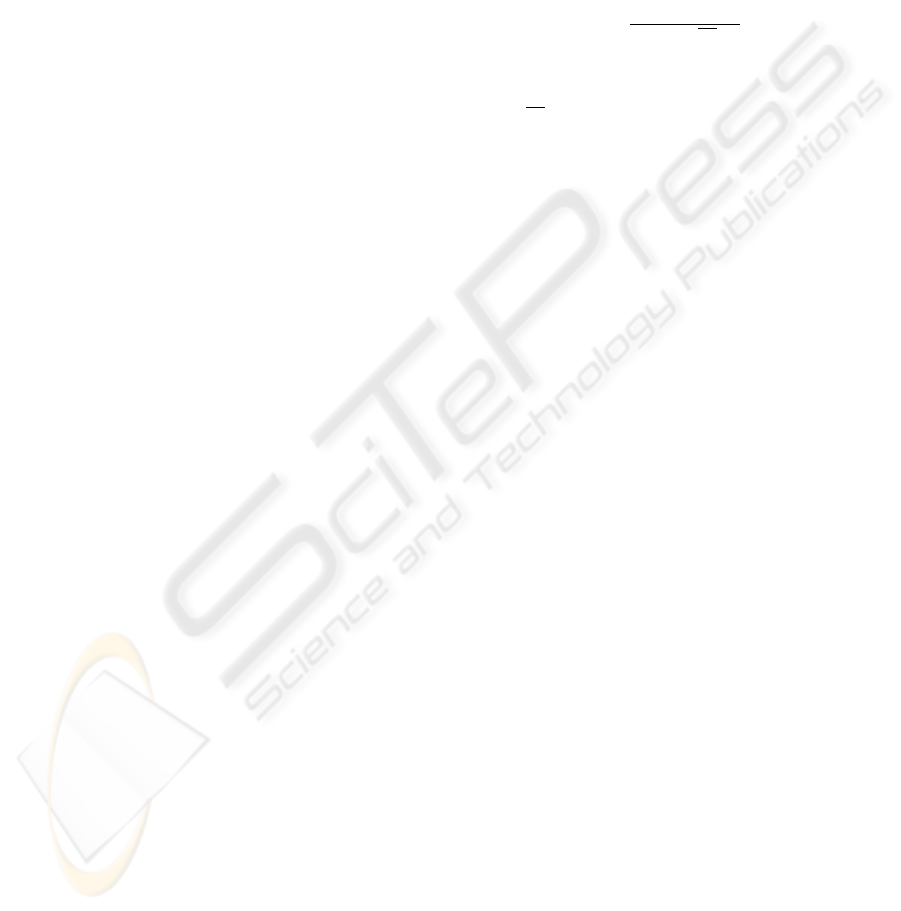
multiple participant decision-making (Kárný et al.,
2007) is discussed.
2 COLD ROLLING MILL
A reversing cold rolling mill is essentially used to re-
duce the thickness of a strip of metal. This is done by
passing the strip between rolls in alternating direction
under high applied pressure and strip tensions. Sev-
eral basic types of cold rolling mills are distinguished
according to the arrangement of working and backup
rolls. Data for experiments came from the twenty-
high rolling mill mentioned in the Introduction. For
this machine the strip thickness is measured by con-
tact meters on both sides of the rolling mill, providing
measurements of the input and output thickness and
its deviation from the nominal value. A target thick-
ness is defined, and this needs to be achieved with
high accuracy depending on the actual nominal thick-
ness and on the type of material. A typical required
tolerance in the considered data set was ± 10µm (mi-
crons).
Strip thickness variation h
2
on the output side of
the rolling mill is considered as the main system out-
put and the only criterial variable for further con-
siderations. The output is, under normal conditions,
securely controlled by the AGC (Automatic Gauge
Control) (Ettler and Jirkovský, 1991). The term "nor-
mal conditions" is worth a discussion: perfectly work-
ing hydraulic roll-positioning system, operating strip
thickness measurement together with values of rolling
force, strip tensions and speeds and other adjustments
from the technologically correct ranges are prerequi-
sites. Nevertheless, performance of the system may
not be optimal in all regions within these ranges due to
e.g. some hardly observable vibrations, unequal cool-
ing and lubrication conditions, etc. Thus even if the
AGC keeps the thickness deviation well in tolerance,
its performance can be further improved by tuning of
its working conditions. This is a task for an expe-
rienced operator. An advisory system was designed
to support potentially inexperienced operators (Quinn
et al., 2003; Ettler et al., 2005b). Evaluation of quality
of advices and their potential improvement is consid-
ered next.
The operator directly adjusts variety of variables
(actions), we consider just three of them: input and
output strip tensions and output strip speed. Actual
values of these actions form three-dimensional vector,
u
t
. The operator makes his decision according to his
experience, using the provided digital measurements
of key internal variables but also his senses (e.g. hear-
ing an unusual noise). On the other hand, the advisory
system must depend only on the measured quantities.
In the considered experiment, the advisory system op-
erated on ten variables including the three operators
actions listed above. The full vector of observed data
will be denoted by d
t
= [y
0
t
, u
0
t
].
Behavior of the operator and its improvement is
difficult to quantify. We define a quantitative cri-
terion, operator’s performance index, on a batch of
1000 subsequent data records:
P =
E(h
2
2
)
E((h
1
− h
1
)
2
)
, (1)
Here, E(h
2
2
) is the expected value of square devia-
tions of output thickness from the desired value, and
E((h
1
− h
1
)
2
) is the expected value of square devia-
tions of input thickness from the mean value of the
batch. The expected values are evaluated empirically
with respect to all data in the batch. In effect, (1)
measures the ratio of output quality to input quality.
An experienced operator is able to adjust conditions
for the AGC so that good output quality is achieved
even if the input quality is low, yielding small values
of P. On the other hand, high values of P indicate
worse output quality than optimum when input qual-
ity was relatively good, which is a sign of suboptimal
settings.
3 ADVISORY SYSTEM DESIGN
An advisory system is a special case of a control sys-
tem, control actions of which are not implemented
automatically, but only displayed to an operator who
has the freedom to follow or ignore the advice. How-
ever, the advices should be designed in such a way
that if followed, the system achieves the optimal per-
formance. Thus, an advisory system can be designed
using methodology developed for design of adaptive
controllers (Kárný et al., 2005). This methodology is
divided in two phases:
Off-line Phase: a family of parametric models of the
system is chosen, and the best model within this
family is identified using historical data. Bayesian
approach to this step involves the tasks of prior
elicitation, parameter estimation, model selection,
and model validation. Then, desired behavior of
the closed-loop system (i.e. the original system
controlled by an ideal controller) is formalized in
the form of a target model.
On-line Phase: the optimal advising strategies are
designed such that the closed loop of the con-
trolled system complemented by the advising
strategy is the closest to the target behavior. The
MERGING OF ADVICES FROM MULTIPLE ADVISORY SYSTEMS - With Evaluation on Rolling Mill Data
67