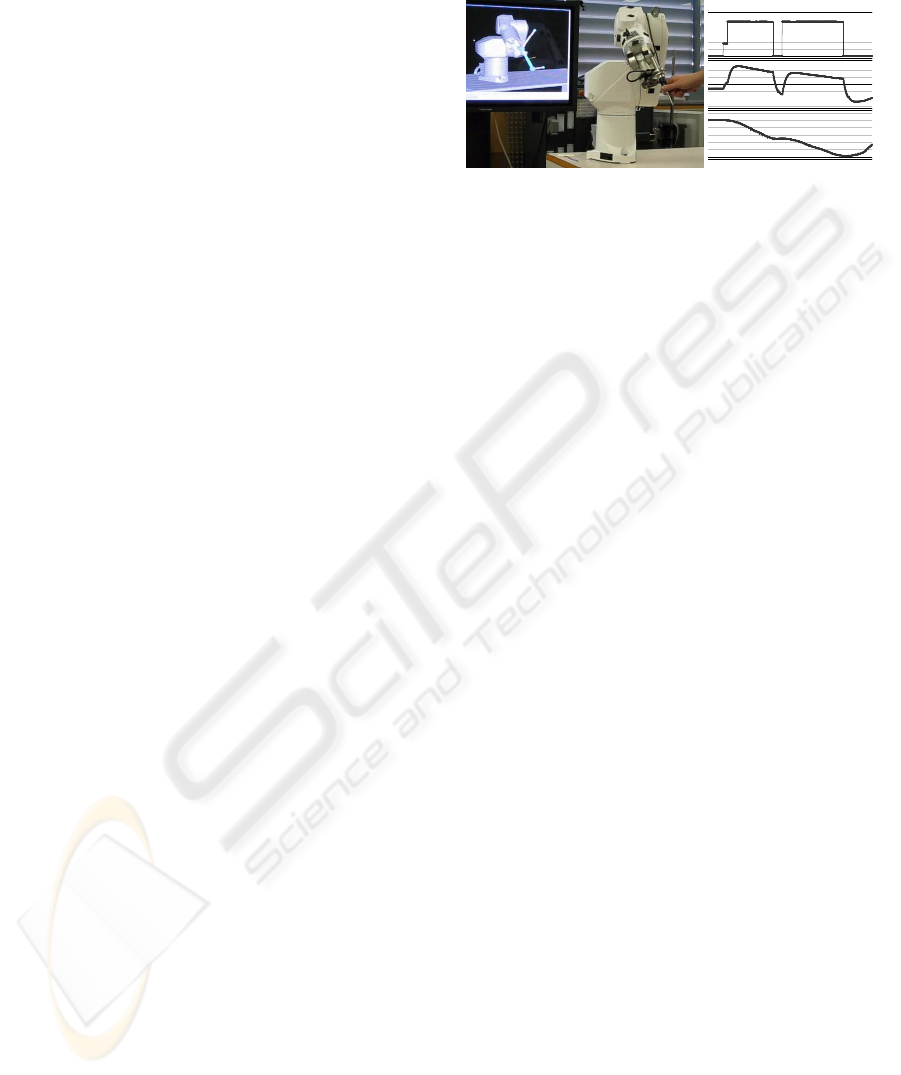
controller runs a communication server under
TCP/IP protocol.
The force sensor measures forces and torques
applied at the tool sustained by the robot. An analog
to digital converter hardware and a calibration
routine are called by the personal computer. As a
result, two vectors are ready to be introduced to the
behaviour model: external forces and torques.
The personal computer runs the hybrid
force/position control loop linked to the motion
controller and the force/torque sensor. As described
in next section, a set of algorithms have been
developed to accomplish all computing
requirements.
The control loop accomplishes the main
functionality of the software developed for the
system. The sequence of routines called at each
cycle is:
• Capture position and orientation of the robot
• Capture voltages at the force sensor
• Compute forces and torques from voltages
• Subtract weight of the tool using its orientation
• Calculate new state according to the behaviour
• Send new state to the motion controller
4B4B4 RESULTS AND CONCLUSIONS
The model proposed, based on a double virtual mass
body, and elastic and viscous links has been tested
with some results shown in Figure 3. Different
experiments have been designed and tested. Simple
tasks like object pick and place, path following or
surface polishing are accomplished. During the
execution of the overall task, a perturbation is
introduced by means of external forces and torques.
The system reacts to the perturbations measured by
the force sensor, computing new positions according
to the described model, and sending the perturbed
positions to the motion controller. After the real
perturbation, the virtual forces described earlier act
as guidance of the endpoint, smoothly driving the
end effector back to the pre-programmed path.
In order to increase human capabilities, some
cooperative tasks include virtual constraints. The
proposed model integrates three categories of
restrictions: geometric, kinematic and dynamic. In
order to accomplish the geometric constraints, a
proximity library (Giralt and Hernansanz 2006) and
a surface navigation method (Hernansanz et al 2007)
have been developed and incorporated.
As it’s a parametric model, different responses
can be achieved with the same model. By changing
the values of the virtual mass, elasticity and
viscosity, the behaviour can be tuned according to
specifications of a certain task.
Figure 3: Experimental results. The left picture shows the
perturbation of a trajectory by means of external forces.
The two below the picture describe numerical values of
the reaction. First graph is the evolution of the external
force applied to the endpoint of the manipulator. The
graph in the middle shows the evolution of velocity of the
end effector. Last graph describes position response to
these force steps.
REFERENCES
Dario, P., Carrozza, M.C., Pietrabissa, A., 1999.
Development and in vitro testing of a miniature
robotic system for computer-assisted colonoscopy. In
Computer Aided Surgery; 4(1):1-14.
Zhou, H.X., Guo, Y.H., Yu, X.F., Bao, S.Y., Liu, J.L.,
Zhang, Y., Ren, Y.G., Zheng, Q., 2006. Clinical
characteristics of remote Zeus robot-assisted
laparoscopic cholecystectomy: A report of 40 cases. In
World J Gastroenterol, 12(16):2606-2609.
Kanade, T., 2004. Workshop on Medical Robotics.
International Advanced Robotics Program. Hidden
Valley, Pennsylvania, USA., pp. 19-22.
Rosenberg, L. B., 1993. Virtual fixtures: Perceptual tools
for telerobotic manipulation. In Proceedings of the
IEEE Annual Int. Symposium on Virtual Reality, pp.
76–82.
Bettini, A., Lang, S., Okamura, A., Hager, G., 2002.
Vision Assisted Control for Manipulation Using
Virtual Fixtures: Experiments at Macro and Micro
Scales. In Proceedings International Conference on
Robotics and Automation, pp. 3354-3361.
Giralt X., Hernansanz A., 2006. Optimització de consultes
de proximitat en entorns robotics. In Proceedings 2ª
Jornadas de Recerca en Automàtica, Visió i Robòtica
ESAII IOC IRI, pp. 257-261.
Hernansanz A., Giralt X., Rodriguez A., Amat J., 2007.
RPQ: Robotic Proximity Queries. Developement and
Applications. In Proceedings of The 4th International
Conference on Informatics in Control, Automation and
Robotics. INSTICC Press.
ICINCO 2008 - International Conference on Informatics in Control, Automation and Robotics
214