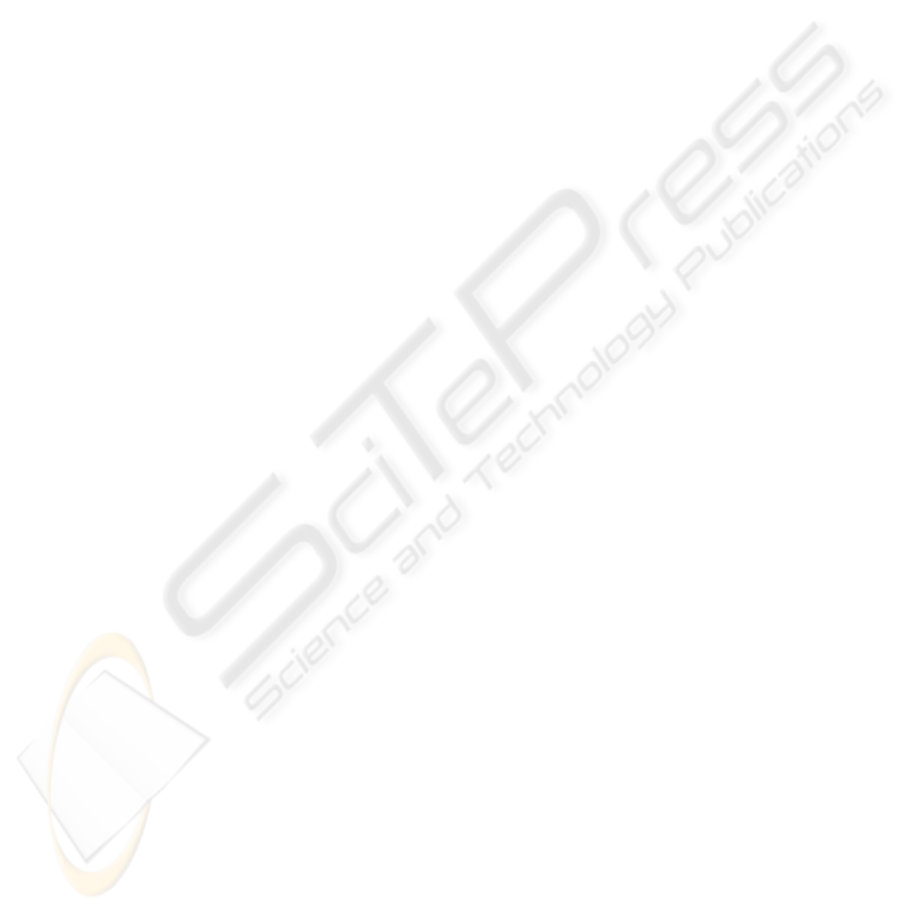
took one third of the time compared to the edge track-
ing skill based on discrete movements (250s vs. 80s).
4.4 Comparision of Both Skills
The skill with discrete movements as well as the skill
with continous movements are capable to completely
explore an edge. Both skills have benefits and dis-
advantages. The benefit of the skill with continu-
ous movements is its speed and its simplicity as it
needs less states compared to the other skill. In par-
ticular, the fast alignment towards the edge using an
adapted zero-force control has to be pointed out. As
the skill with discrete movements has at first to col-
lect single points to perform the alignment gradu-
ally, the skill needs more time and more control pro-
cesses. Otherwise it is easier for a superior level to
supervise these discrete movements. As outliers can
be detected by collecting a great amounts of contact
points, the exploration behavior becomes very stable.
For the exploration of unknown structures, collecting
single points is still favored, as it provides the supe-
rior level with more possibilitys for interaction. Skills
only based on a control algorithms need the whole
flow of information for the spatial alignment and are
not made for interaction. A combination of both ap-
proaches seems to be promising.
5 CONCLUSIONS AND FUTURE
WORKS
This work introduced a novel framework for the ex-
ploration of objects using haptic feedback. This
framework consists of three layer: an exploration
planner, a skill library with reactive exploration be-
haviors and a haptic perception layer. Two different
skill schemes have been introduced: skills with dis-
crete and skills with continuous movements. The per-
formance of our approach has been evaluated in the
evaluation scenario of tracking an edge which is ar-
bitrarily located in space. The tactile sensor and the
force-torque complement one another. The determi-
nation of contact points using a force-torque sensor
is less accurate but independent from the edge angle.
It allows the alignment of the sensor pad so that the
critical angle for the tactile sensor is under-run and
the tactile sensor can take over the exploration proce-
dure in order to undertake a more precise exploration
procedure.
Furthermore it became apparent that the explo-
ration with discrete and the exploration with contin-
uous movements have both benefits and drawbacks.
The continuous exploration based on a control behav-
ior is faster but provides less possibilities for inter-
action. Exploration procedures with discrete move-
ments are slower but are more robust and better to su-
pervize. A combination of both approaches seems to
be promising. Future work will include the extension
of the skill library and the transfer of an exploration
behavior on a humanoid robot hand.
REFERENCES
Chen, N., Zhang, H., and Rink, R. (1995). Edge track-
ing using tactile servo. In IROS ’95: Proceedings
of the International Conference on Intelligent Robots
and Systems-Volume 2, page 2084, Washington, DC,
USA. IEEE Computer Society.
Heidemann, G. and Schoepfer, M. (2004). Dynamic tac-
tile sensing for object identification. In Proc. IEEE
Int. Conf. Robotics and Automation ICRA 2004, pages
813–818, New Orleans, USA. IEEE.
Hu, M.-K. (1962). Visual Pattern Recognition by Moment
Invariants. IEEE Transactions on Information Theory,
8(2):179–187.
Klatzky, R., Lederman, S., and Reed, C. (1987). There’s
more to touch than meets the eye: The salience of
object attributes for haptics with and without vision.
In Journal of Experimental Psychology: General,
116(4), pages 356–369.
Lederman, S. and Klatzky, R. (1987). Hand movements: A
window into haptic object recognition. In Cognitive
Psychology, 19(3), pages 342–368.
Schmidt, P. A., Ma
¨
el, E., and W
¨
urtz, R. P. (2006). A
sensor for dynamic tactile information with applica-
tions in human-robot interaction and object explo-
ration. Robot. Auton. Syst., 54(12):1005–1014.
Weiss, K. and Woern, H. (2005). The working principle
of resistive tactile sensor cells. In Proceedings of the
IEEE International Conference on Mechatronics and
Automation, Canada.
OBJECT EXPLORATION WITH A HUMANOID ROBOT - Using Tactile and Kinesthetic Feedback
281