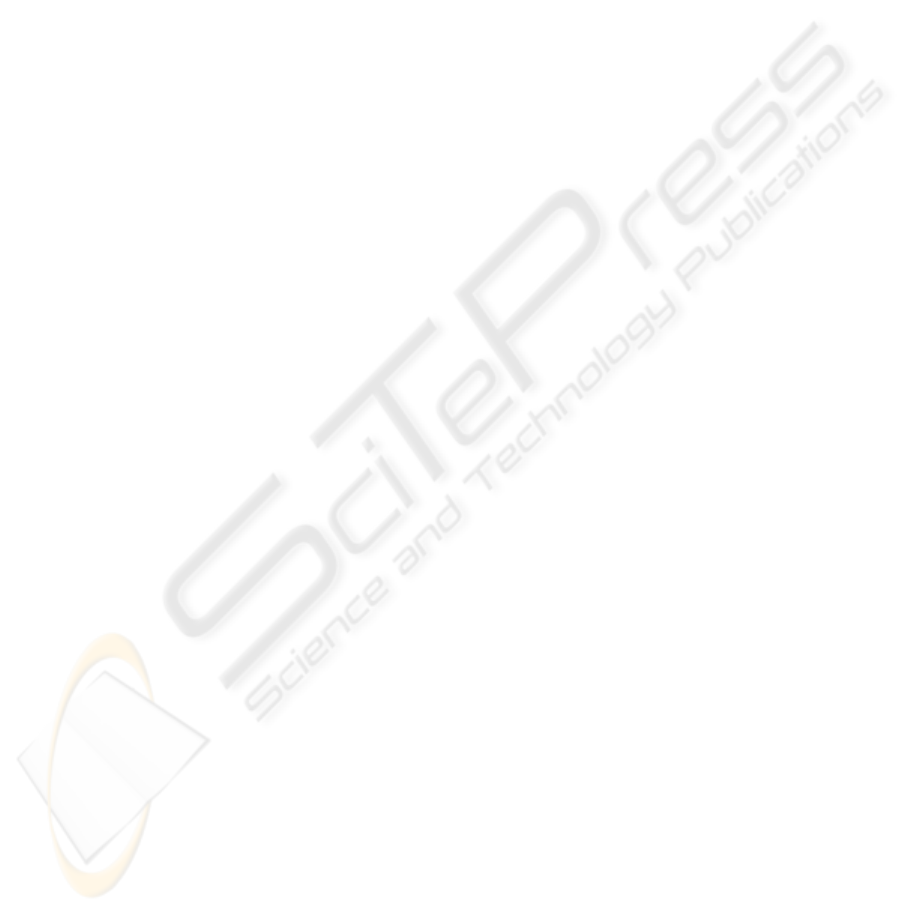
For each machining node, the access paths
which are associated with it, added with machining
operations carried out on this node, are linked with
logical AND. This regrouping is an aggregate
operation.
For the illustration example, the access paths
calculated in the first step of the procedure for the
machining area M
1
are the following: OR
(
1
MIN
Tr
→
,
12
MM
Tr
→
) and OR (
2
M
1
M
Tr
→
,
OUT
1
M
Tr
→
). The
following elementary transfers are then obtained
using the second step of the procedure.
1
MIN
Tr
→
= AND (
1
ZIN
3
R
TrE
→
,
2
Z
1
Z
CV
TrE
→
,
1
M
2
Z
1
R
TrE
→
);
12
MM
Tr
→
= AND (
4
Z
2
M
2
R
TrE
→
,
1
Z
4
Z
CV
TrE
→
,
2
Z
1
Z
CV
TrE
→
,
1
M
2
Z
1
R
TrE
→
);
21
MM
Tr
→
= AND (
2
Z
1
M
1
R
TrE
→
,
3
Z
2
Z
CV
TrE
→
,
4
Z
3
Z
CV
TrE
→
,
2
M
4
Z
2
R
TrE
→
);
OUTM
1
Tr
→
= AND {
2
Z
1
M
1
R
TrE
→
,
3
Z
2
Z
CV
TrE
→
, OR [AND (
4
Z
3
Z
CV
TrE
→
,
1
Z
4
Z
CV
TrE
→
), AND
(
6
Z
3
Z
CV
TrE
→
,
1
Z
6
Z
CV
TrE
→
)],
OUT
1
Z
3
R
TrE
→
}.
Finally,
1
M
TrA = AND [OR (
1
MIN
Tr
→
,
12
MM
Tr
→
), OR
(
2
M
1
M
Tr
→
,
OUT
1
M
Tr
→
)].
4 CONCLUSIONS
In this paper our modeling method dedicated to
FMS
mode handling is extended. The FMS
functional model is obtained by a modular and
hierarchical decomposition leading to the
elementary machining and transfer operations. For
large scale systems, it is difficult to obtain all
possible redundancies of a plant. So we propose to
determine aggregate operations associated with
machining areas from the plant model represented
by the OAG. The aggregate operations are generic
concepts which depend only on the plant and not on
production goals. Such method enables to generate
automatically aggregate operations for an existing
system or a system being designed. The proposed
modeling steps are then illustrated through an
example of a manufacturing cell.
Further works aim at implementing the proposed
method within the information system
CASPAIM_soft (Ndiaye et al., 2002).
REFERENCES
Berruet, P., Toguyéni, A.K.A., Craye, E., 2000. Towards
implementation of recovery procedures for FMS
supervision. Computers in Industry, 43, 227-236.
Elkhattabi, S., Craye, E., Gentina, J.C., 1995. Supervision
by the behavior modeling. In SMC’95, IEEE
International Conference on Systems, Man, and
Cybernetics.
Hamani, N., Dangoumau, N., Craye , E., 2005. A
comparative study of mode handling approaches. In
CiE’05, 35th International Conference on Computers
& Industrial Engineering.
Hamani, N., Dangoumau, N., Craye, E., 2006. A
functional modeling approach for Flexible
Manufacturing Systems mode handling. In INCOM'06,
12th IFAC Symposium on Information Control
Problems in Manufacturing. Elsevier Press.
Ndiaye, D., Bigand, M., Corbeel, D., Bourey, J.-P., 2002.
Information system for production engineering. Int. J.
of Computer Integrated Manufacturing, 15(3), 233-
241.
Ranky, P., 1990. Flexible manufacturing cells and systems
in CIM, CIMware Ltd. Guildford, U.K.
Tawegoum, R., Castelain, E., Gentina, J.-C., 1994. Real
time piloting of flexible manufacturing systems.
European J. of Operational Research, 78, 252-261.
Toguyeni, A.K.A., Craye, E., Gentina, J.-C., 1996. A
framework to design a distributed diagnosis in FMS.
In SMC’96, IEEE International Conference on
Systems, Man, and Cybernetics.
Toguyéni, A.K.A., Berruet, P., Craye, E., 2003. Models
and algorithms for failure diagnosis and recovery in
Flexible Manufacturing Systems. Int. J. of Flexible
Manufacturing Systems, 15(1), 57-85.
USING THE OAG TO BUILD A MODEL DEDICATED TO MODE HANDLING OF FMS
287