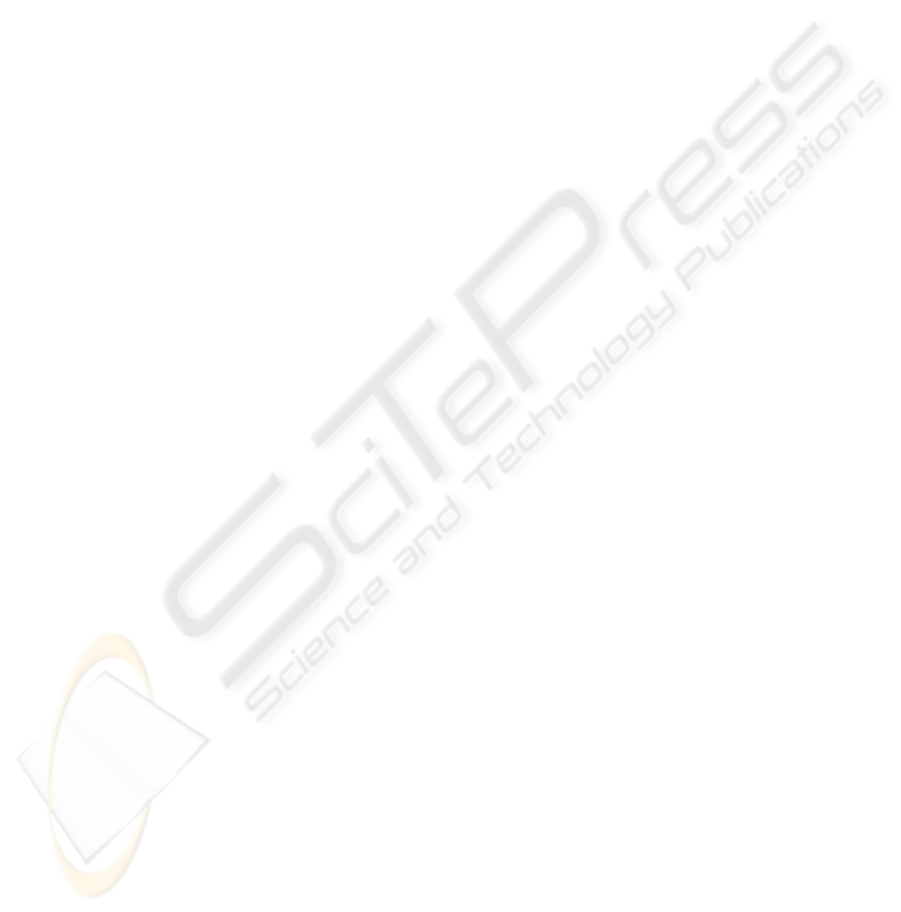
REMOTE ROBOT CONTROL AND HIGH AVAILABILITY
Silvia Anton, Florin Daniel Anton and Theodor Borangiu
University Politehnica of Bucharest, Dept. of Automation and Applied Informatics
313 Spl. Independentei, sector 6, RO-060032, Bucharest, Romania
Keywords: Networked robotics, high availability, remote control, flexible manufacturing systems, robot vision.
Abstract: Nowadays production flows are modular, each module in the enterprise being specialized and used to
achieve a particular task. In many cases the modules are connected and materials are sequentially processed
in each module resulting a final, unique product or assembly. One typical such production module is a
flexible cell/system using multiple robots. In this structure, providing continuous service for applications is
a key component of a successful robotized implementing of manufacturing. High availability (HA) is one of
the components contributing to continuous service provision for applications, by masking or eliminating
both planned and unplanned systems and application downtime. A high availability solution in robotized
manufacturing provides automated failure detection, diagnosis, application recovery, and node (robot
controller) re integration. The paper describes a platform which is a software product designed to control
and supervise multiple robot-vision controllers using remote connections with a number of Adept
Technology V+ controllers configured to use a high availability implementation, either located in a local
network or via Internet.
1 INTRODUCTION
In a robotized flexible manufacturing cell, robot (-
vision) controllers are masters over local
workstations or cells, because robot manipulators
connect two important material flows: the
processing flow and the transportation flow. One
solution to integrate these two flows with on-line
quality control in the manufacturing module, further
networked with the design and planning modules, is
to adopt a unified feature-based description of parts
and assemblies, technological operations, geometric
& surface quality control, grasping and manipulating
(Tomas Balibrea, et al., 1997).
The system is configured for high availability .
HA systems are a combination of hardware and
software components configured to work together to
ensure automated recovery in case of failure with a
minimal acceptable downtime (Harris et. al., 2004).
2 THE STRUCTURE OF THE
SYSTEM
The system is composed by the following
applications (Figure 1):
The Server Application (SA): Remote visual
control and monitoring of multiple robot controllers
from mobile and stationary matrix cameras.
• Visual control: the Server Application supports
almost all V+ and AdeptVision program
instructions and monitor commands.
• Monitoring: a Monitoring/Treatment scheme can
be defined for each Client/Station. For each client
a list of events and controller variables to be
monitored according to a user-definable timing
and precedence, and reacted at by user-definable
actions/sequences can be specified in an
Automatic Treatment Window.
• Communication management: the Server
Application manages the communication with the
robot controllers and cameras, transfers real-time
images from the cameras observing the robot
workplace and production environment, reports
status information, stores in a database and
displays images taken by the robot camera.
The eClients Applications (eCA): Java
applications running in web browsers. They provide
portal services and the connection of networked
production agents: image data and RV program /
report management; real-time robot control and cell /
workplace observation. The eCA are composed by
two applications:
229
Anton S., Daniel Anton F. and Borangiu T. (2008).
REMOTE ROBOT CONTROL AND HIGH AVAILABILITY.
In Proceedings of the Fifth International Conference on Informatics in Control, Automation and Robotics - RA, pages 229-232
DOI: 10.5220/0001507002290232
Copyright
c
SciTePress