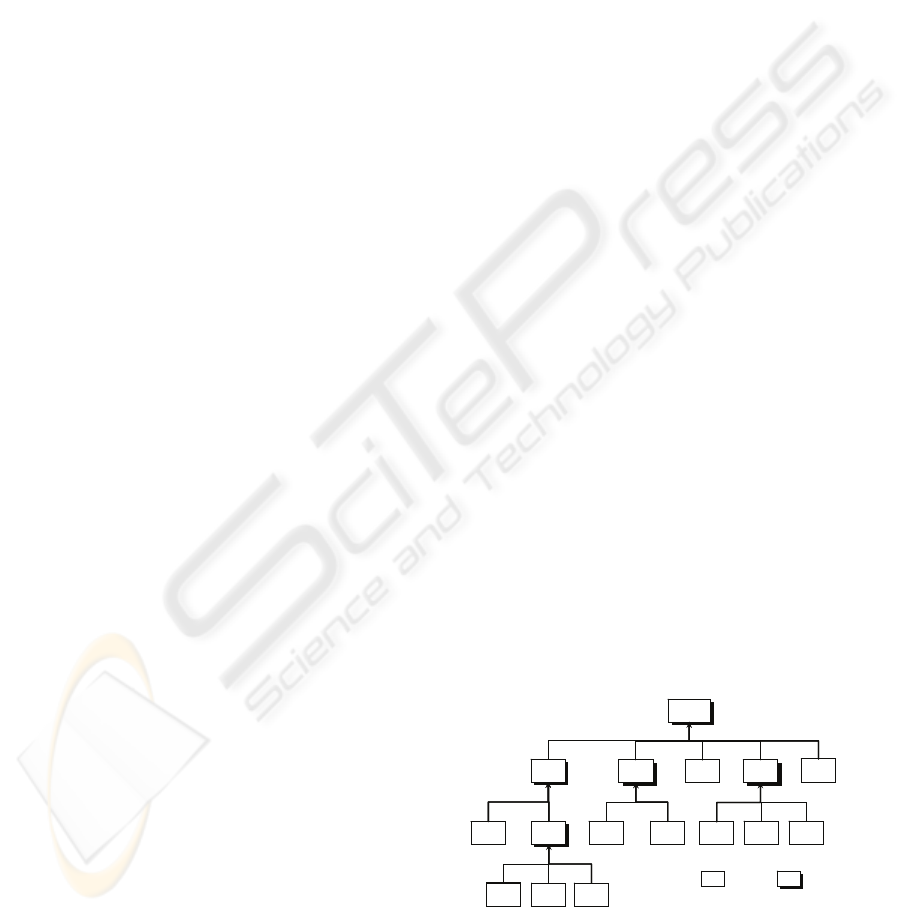
determine appropriate ones. In such selection,
arrangement and evaluation processes, a number of
configuration rules, i.e., constraints or restrictions
imposed by manufacturing capabilities, capacity
limits, desired objectives that measure productivity
and efficiency, etc. must be satisfied. Consequently,
decision making in production configuration is
deemed to be very complex.
With an attempt to assist practitioners to better
understand and implement production configuration,
in this study, we tackle the underlying logic for
configuring production processes for product
families. In view of the potential of dynamic
modelling and visualization in shedding light on
process logic, we propose to model production
configuration graphically. In relation to fundamental
issues in production configuration (Zhang, 2007),
the resulting difficulties in modelling production
configuration have been identified. They include 1)
handling a high product and process variety; 2)
accommodating many process variations resulting
from design changes; 3) dealing with configuration
at different abstraction levels; 4) satisfying a number
of constraints/restrictions describing, for example,
the connections between product and process
elements; and 5) selecting process elements/
processes from multiple alternatives.
Owing to their executability, graphical
representation and mathematic support, Petri nets
(PNs) have been well recognized as a powerful
modelling, simulation and evaluation tool for
complex flows and processes (Peterson, 1981). A
number of extensions have been made to classic PNs
in order to satisfy different modelling requirements.
Among all, colored PNs (CPNs; Jensen, 1995),
timed PNs (TPNs; Ramachandani, 1974) and nested
PNs (NPNs; Lomazova, 2000) are of particular
interest in this study. CPNs are able to provide a
concise, flexible and manageable representation of
large systems by attaching a variety of colors to
tokens. By including timing, TPNs can capture
systems physical behaviours through assuming
specific durations for various activities. By
considering PNs as tokens, NPNs is expected to
model large and complex system through refinement
and abstraction.
In this paper, we apply PN techniques to model
production configuration by taking into account the
difficulties imposed by the fundamental issues.
Accordingly, a formalism of NCTPNs (nested
colored timed PNs) has been developed by
integrating the basic principles of CPNs, TPNs and
NPNs. Product/process variety and configuration
constraints are handled by attaching various data
describing product items and process elements to
tokens, resulting colored tokens. A reconfiguration
mechanism is incorporated into the modelling
formalism to cope with process variations. Timing is
introduced to facilitate the selection of proper
machines, operations and processes. Moreover, a
multilevel net system is further developed based on
net nesting in NPNs to tackle explicitly the
granularity issue in production configuration.
The next section introduces an industrial
example of vibration motors for mobile phones,
which is used throughout the rest of this paper to
demonstrate the proposed formalism and the
modelling of production configuration.
2 INDUSTRIAL EXAMPLE
The industrial example adopted is the production of
vibration motors for mobile phones. The increasing
variations in mobile phones design lead to large
numbers of customized vibration motors to be
produced. Together with other factors, e.g., short
delivery lead times, the high variety of vibration
motors complicate the planning of their production
processes.
Modelling production configuration of a
vibration motor family using the proposed NCTPNs
is presented in this study. Figure 1 shows the
common product structure of the motor family. This
motor family assumes several part types, as shown
in the figure. According to the design requirements,
individual motors may not contain a specific variant
from each part family. In other words, not all part
types are assumed by each individual motor variant.
While the company produces all assembly families
and final motors, among all they manufacture
several part families, e.g., Ba family, Bb family, Tl
family.
VM
Rh
BA
AA
FA
CA
St Mt
Fm
Cl
Tp
Ct
Wt
Ba
Bb
Tl
: Part; : Assembly
FA: Frameassy; BA: Bracketassy; Rh: Rubber holder; Wt: Weight
VM: Vibration motor; AA: Armatureassy
CA: Coilassy; St: Shaft; Fm: Frame; Mt: Magnet; Ba: Bracket a
Bb: Bracket b; Tl: Terminal; Ct: Commutator; Cl: Coil; Tp: Tape
VM
Rh
BA
AA
FA
CA
St Mt
Fm
Cl
Tp
Ct
Wt
Ba
Bb
Tl
: Part; : Assembly
FA: Frameassy; BA: Bracketassy; Rh: Rubber holder; Wt: Weight
VM: Vibration motor; AA: Armatureassy
CA: Coilassy; St: Shaft; Fm: Frame; Mt: Magnet; Ba: Bracket a
Bb: Bracket b; Tl: Terminal; Ct: Commutator; Cl: Coil; Tp: Tape
Figure 1: The common product structure.
ICEIS 2008 - International Conference on Enterprise Information Systems
6