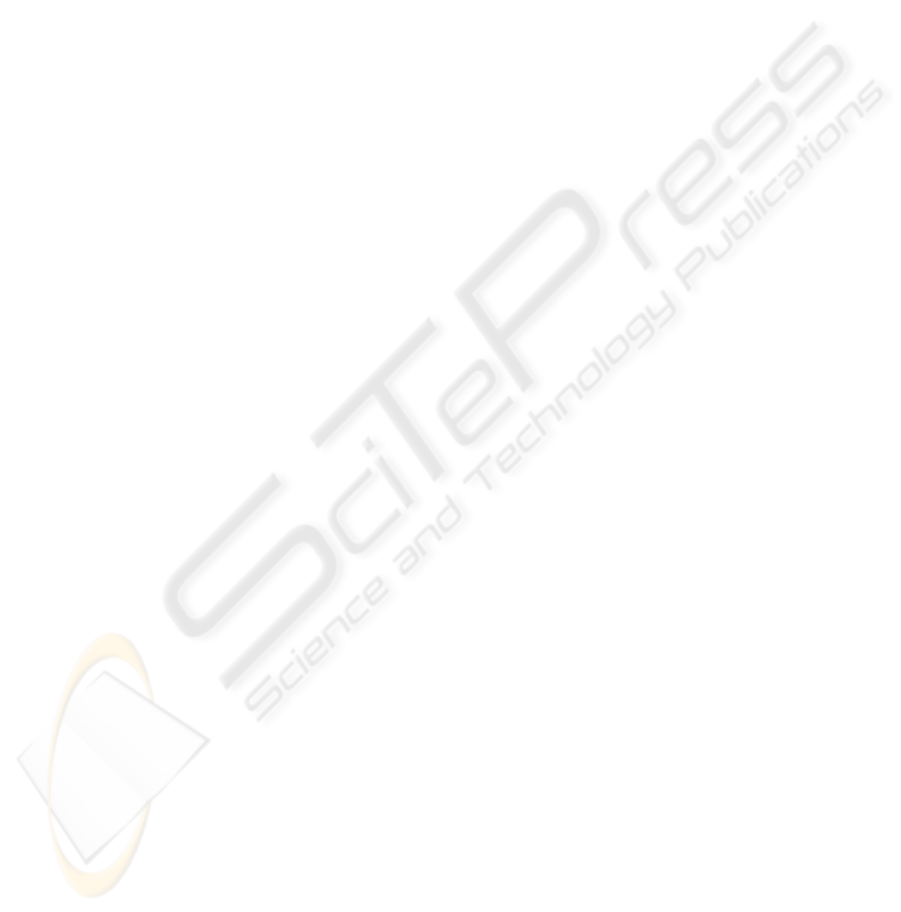
Then” rule structure to reason and analyze the key
performance indicators. The case library is used to
record all past cases of resource allocation decisions.
In those cases, the basic job requirements, resource
adoption, performance scores and their objectives
for assessment are organized and saved. They can be
retrieved in the performance evaluation module for
assessing the performance.
4 DISCUSSION
The proposed KPMS enhances the performance of
manufacturing companies by facilitating them to
acquire the greatest utilization and effectiveness
from their production assets, which is the ultimate
purpose of asset management. Performance
measurement enables managers to understand the
effect of their resource allocation decisions through
an overall performance score. As it is a dynamic
system that can select appropriate performance
indicators according to the company objectives, it is
suitable for current competitive environment in
which companies occasionally need to revise their
strategies and objectives for enhancing the
competitiveness. The importance of performance
criteria would be adjusted by the system to react to
the changes in company objectives.
Moreover, the system encourages companies to
achieve continuous improvement on their resource
utilization. After determining the overall
performance score, the assessed resource allocation
decision, as a new case, is evaluated against some
past similar cases of resource allocation retrieved
from the case library in order to realize current
performance and identify any area for improvement.
Consequently, it can suggest ways for improving the
performance by reusing the experience gained in
past cases while the new case of resource allocation
can be retained in the knowledge repository.
This paper mainly provides a framework of the
proposed KPMS. Implementation of the system is
being conducted in a local polyfoam manufacturer.
Once results are obtained, they will be presented in
further publication.
5 CONCLUSIONS
A good resource allocation planning is important for
manufacturing companies to utilize their physical
assets effectively. Performance measurement on the
resource allocation is necessary to assist companies
improving the resource utilization and
accomplishing their objectives. However, selection
of suitable performance indicators in accordance
with company objectives is a complex task
especially in a dynamic manufacturing environment.
The staff usually judge the resource allocation
decisions by their own knowledge and experience.
However, it cannot guarantee that the physical assets
are utilized in the most effective way. In this paper,
the knowledge-based performance measurement
system establishes an approach for evaluating the
performance of resource allocation decisions. It
helps manufacturing companies to improve their
operations in order to gain maximum utilization and
effectiveness from the physical assets.
ACKNOWLEDGEMENTS
The authors wish to thank the Research Committee
of the Hong Kong Polytechnic University for
supporting the project.
REFERENCES
Ahmad, M.M., Dhafr, N., 2002. Establishing and
improving manufacturing performance measures,
Robotics and Computer Integrated Manufacturing,
Vol. 18, pp. 171-176.
Chen, C.C., 2008. An objective-oriented and product-line-
based manufacturing performance measurement,
International Journal of Production Economics, Vol.
112, pp. 380-390.
Lee, J., Ni, J., Djurdjanovic, D., Qiu, H., Liao, H.T., 2006.
Intelligent prognostics tools and e-maintenance,
Computers in Industry, Vol. 57, pp. 476-489.
Mitchell, J.S., Carlson, J., 2001. Equipment asset
management – what are the real requirements?,
Reliability Magazine, October, pp. 4-14.
Wang, W.M., Cheung, C.F., Lee, W.B., Kwok, S.K., 2006.
A knowledge-based infotronics supervisory system for
intelligent service automation, Proceedings of the
Institution of Mechanical Engineers - Part B -
Engineering Manufacture, Vol. 220 No. 5, pp. 745-
758.
Wen, W., Chen, Y.H., Chen, I.C., 2008. A knowledge-
based decision support system for measuring
enterprise performance, Knowledge-based systems,
Vol. 21, pp. 148-163.
Yurdakul, M., 2002. Measuring a manufacturing system’s
performance using Saaty’s system with feedback
approach, Integrated manufacturing systems, Vol. 13
No. 1, pp. 25-34.
ICEIS 2008 - International Conference on Enterprise Information Systems
192