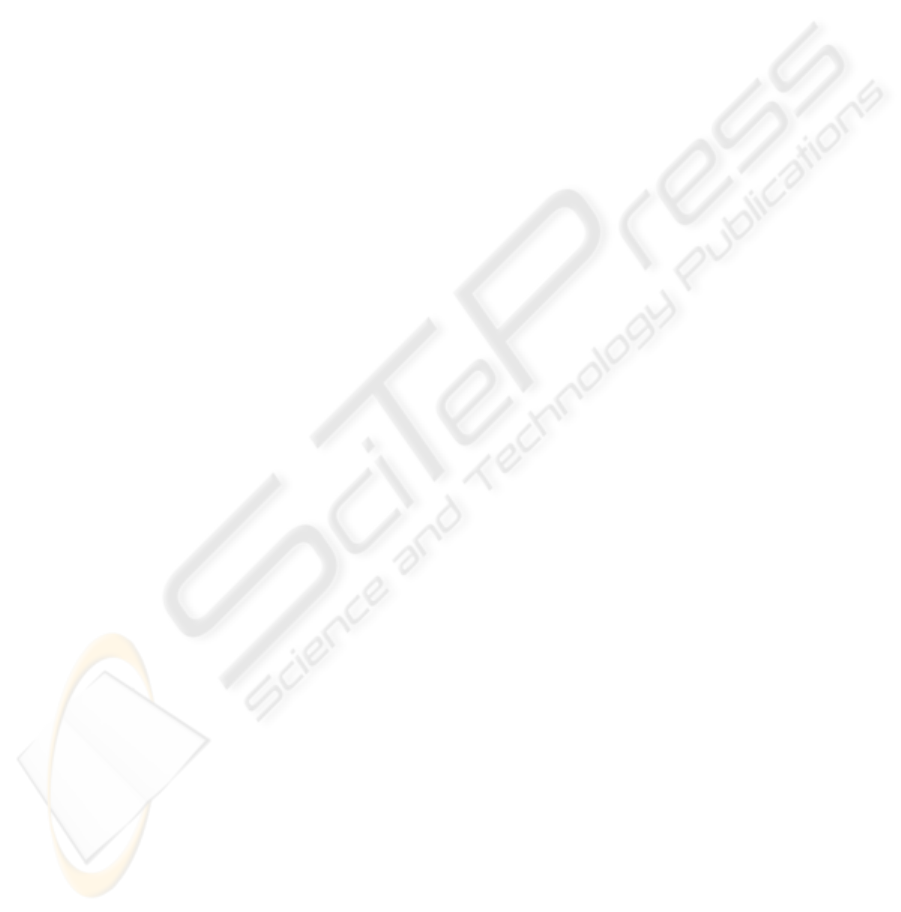
7 CONCLUSIONS
In this paper by the means of six sigma strategy, a
non-linear mathematical model for machine
partitioning in TAGV systems is considered with
bi-objectives that are minimizing the material flow
intra & inter-loops and minimization of maximum
amount of inter cell flow. Regarding to the NP-hard
complexity of the problem, ant colony meta-
heuristic method is applied. Then in different test
problems the computational time and the objective
functions value of ant method is being compared
with traditional methods.
REFERENCES
Asef-Vaziri, A., Dessouky, M., Sriskandarajah, C., 2001.
A loop material flow system design for automated
guided vehicles. Int. J. Flex. Manuf. Sys. 13, 33–48.
Asef-Vaziri, A. Laporte, G. Sriskandarajah, C., 2005. The
block layout shortest loop design problem. IIE Trans.
32, 724–734.
Banerjee, P., Zhou, Y., 1995. Facilities layout design
optimization with single loop material flow path
configuration. Int. J. Prod. Res. 33, 183–203.
Barad, M., Sinriech, D., 1998. A Petri net model for the
operational design and analysis of segmented flow
topology (SFT) AGV system. Int. J. Prod. Res. 36,
1401–1426.
Bozer, Y.A., Srinivasan, M.M., 1991. Tandem
configuration for automated guided vehicle systems
and the analysis of single vehicle loops. IIE Trans. 23,
72–82.
Bozer, Y.A., Srinivasan, M.M., 1992. Tandem AGV
systems: a partitioning algorithm and performance
comparison with conventional AGV systems. Eur. J.
Operat. Res. 63, 173–191.
Chhajed, D., Montreuil, B., Lowe, T., 1992.Flow network
design for manufacturing systems layout. Eur. J.
Operat. Res. 57 - 145–161.
Farahani, R.Z., Tari, F.G., 2001. Optimal flow path
designing of unidirectional AGV systems. Int. J. Eng.
Sci. 12 , 31–44.
Farahani, R.Z., Tari, F.G., 2002. A branch and bound
method for finding flow-path designing of AGV
systems. IIE Trans. 15 , 81–90.
Farahani, R.Z., Laporte, G., Sharifyazdi, M., 2005 A
practical exact algorithm for the shortest loop design
problem in a block layout. Int. J.Prod. Res. 43, 1879–
1887.
Gaskin, R.J., Tanchoco, J.M.A., 1987. Flow path design
for automated guided vehicle system. Int. J. Prod. Res.
25, 667–676.
Gaskin, R.J., Tanchoco, J.M.A., Taghaboni, F., 1989.
Virtual flow paths for free ranging automated guided
vehicle systems. Int. J. Prod. Res. 27, 91–100.
Hillier, F.S., Lieberman, G.J., 2005. McGraw-Hill
International Edition, Eight edition. Operations
Research.
Kaspi, M., Tanchoco, J.M.A., 1990. Optimal flow path
design of unidirectional AGV systems. Int. J. Prod.
Res. 28, 1023–1030.
Kaspi, M., Kesselman, U., Tanchoco, J.M.A., 2002.
Optimal solution for the flow path design problem of a
balanced unidirectional AGV system, Int. J. Prod.
Res. 40, 349–401.
Kim, C.W.. Tanchoco, J.M.A., 1991. Conflict-free
shortest-time bi-directional AGV routing. Int. J. Prod.
Res. 29, 2377–2391.
Ko, K.C., Egbelu, P.J., 2003. Unidirectional AGV guide
path network design: a heuristic algorithm. Int. J.
Prod. Res. 41, 2325–2343.
Kouvelis, P., Gutierrez, G.J., Chiang, W.C., 1992.
Heuristic unidirectional flow path design approach for
automated guided vehicle systems. Int. J. Prod. Res.
30, 1327–1351.
Laporte, G., Asef-Vaziri, A., Sriskandarajah, C., 1996.
Some application of the generalized traveling
salesman problem. J. Oper. Res. Soc. 47,1461–1467.
Laporte, G., Farahani, Z.R., 2006. Elnaz Miandoabchi,
Designing an efficient method for tandem AGV
network design problem using tabu search. Applied
Mathematics and Computation.
Lin, J.T., Chang, C.C.K., Liu, W.C., 1194. A load routing
problem in a tandem-configuration automated guided
vehicle system, Int. J. Prod.Res. 32, 411–427.
Rajagopalan, S., Heragu, S.S., Taylor G.D., 2004. A
Lagrangian relaxation approach to solving the
integrated pick-up/drop-off point and AGV flow path
design problem. Appl. Math. Model. 28, 735–750.
Seo, Y., Egbelu, P.J., 1995. Flexible guide path design for
automated guided vehicle systems. Int. J. Prod. Res.
33, 1135–1156.
Sinriech, D., Tanchoco, J.M.A., 1991. Intersection graph
method for AGV flow path design, Int. J. Prod. Res.
29, 1725–1732.
Sinriech, D., Tanchoco, J.M.A., 1993. Solution methods
for the mathematical models of single loop AGV
systems. Int. J. Prod. Res. 31, 705–726.
Sinriech, D., Tanchoco, J.M.A., 1994. SFT – segmented
flow topology, in: J.M.A. Tanchoco (Ed.), Material
Flow System in Manufacturing, Chapter 8. Chapman
and Hall, London, 200–235.
Sinriech, D., Tanchoco, J.M.A., 1995. An introduction to
the segmented flow approach to discrete material flow
systems. Int. J. Prod. Res. 33, 3381–3410.
Sinriech, D., Tanchoco J.M.A., 1997. Design procedures
and implementation of the segmented flow topology
(SFT) for discrete material flow systems. IIE Trans.
29, 323–335.
Sun, X.-C., Tchernev, N., 1996. Impact of empty vehicle
flow on optimal flow path design for unidirectional
AGV systems. Int. J. Prod. Res. 34, 2827–2852.
Tanchoco, J.M.A., Sinriech, D., 1992. OSL – optimal
single loop guide paths for AGVs. Int. J. Prod. Res.
30, 665–681.
Venkataramanan, M.A., Wilson, K.A., 1991. A branch-
and bound algorithm for flow path design of
automated guided vehicle systems. Nav. Res. Logist.
Q. 38, 431–445.
MACHINE GROUPING IN CELLULAR MANUFACTURING SYSTEM USING TANDEM AUTOMATED GUIDED
VEHICLE WITH ACO BASED SIX SIGMA APPROACH
267