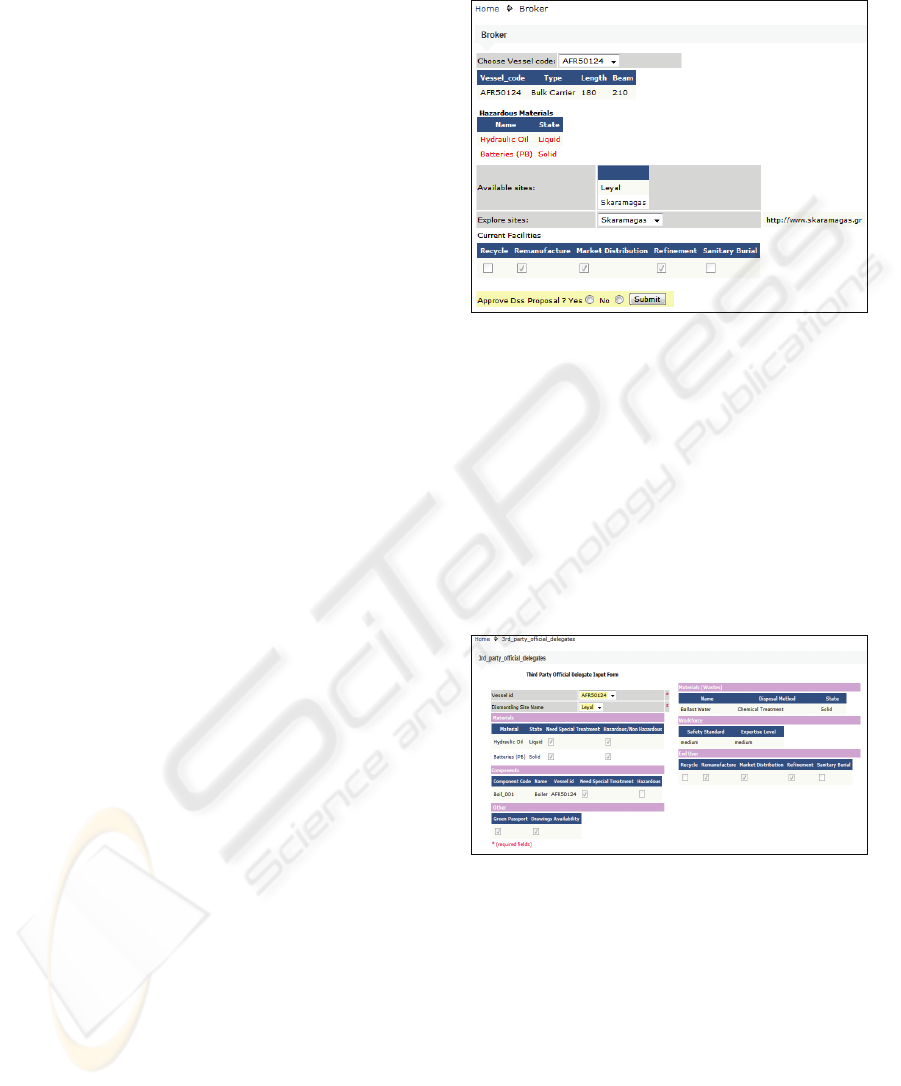
occupational safety, health, cost and energy effective
issues.
Large databases, built in Microsoft® Access, are
linked with Microsoft® Excel tables, which in turn
are exploited by the Extend simulation software,
where a generic model of the dismantling process
taking place at a ship yard has been designed. The
dismantling process comprises a series of
hierarchically structured sub-activities, for which all
necessary parameters have been taken into account
(including capacities, resources, average demand
and dismantling rate). The end user has the
capability to populate fields in a user-friendly web
interface and obtain the results of a dynamic analysis
on appropriate output interfaces.
2.1 DSS Architecture
As mentioned above, the proposed system exploits a
simulation model built in Extend simulation
software, which is installed in a server. Components
of the simulation model are connected through
ODBC (Open Database Connectivity) technology
with the database. A runtime development kit
allows the simulation model to run at the
background, without (direct) user interference. In
this way, any user who is not familiar with
simulation modeling can run the model directly from
the web interfaces, without having the burden to deal
with simulation technicalities.
The system’s interfaces have been designed by
exploiting an open source Content Management
System (CMS). Their content consists of html pages,
dynamic asp pages, forms, icons and forums to
support communication among users. Moreover,
other features offered through those features include
document repositories, flowcharts, and support for
information search. Depending on user’s requests,
some outputs are the outcome of simple data
processing (e.g. comparisons, matching, etc.), while
some others are the result of modeling simulations.
Records can be easily withdrawn from a data
repository, while new documents, guidelines and
regulations can be uploaded or downloaded in the
database through an appropriate link.
2.2 DSS Web interfaces
The system aims at serving the following types of
users; i) dismantling site owners, ii) broker
companies, iii) third party official delegates, and iv)
environmental and energy related organizations.
Users have the ability to populate the databases,
select from predefined data and models, obtain
results based on selected inputs and retrieve
information from historical records.
Figure 1: Broker input page.
A broker company can see in advance all the
available (and suitable) yards to dismantle
environmentally and cost effectively a vessel,
provided that the characteristics, properties and
functions of the particular vessel are known (Fig. 1).
The system will propose the “best fit” yard found,
showing its characteristics in detail. The system
compares all technical, environmental, occupational,
and recycling characteristics of the existing yards
(stored in the database) with the characteristics of
the vessel that needs to be dismantled.
Figure 2: Third party official delegate input page.
Third-party delegates (i.e. European Union IMO,
ILO, etc.) want to assure the compliance of a
vessel’s dismantling process against environmental,
safety and energy guidelines. These requests, which
are time irrelevant, are handled through the
appropriate information processing (matching). For
example, a user can indicate a specific vessel that is
about to be dismantled in a specific yard (see Figure
2), and automatically know if some materials will
not be able to be treated or disposed safely, or what
the chances of a human accident are due to
inadequate safety conditions at this yard. Moreover,
INTEGRATING SIMULATION INTO A WEB-BASED DECISION SUPPORT TOOL FOR THE COST EFFECTIVE
PLANNING OF VESSEL DISMANTLING PROCESSES
545