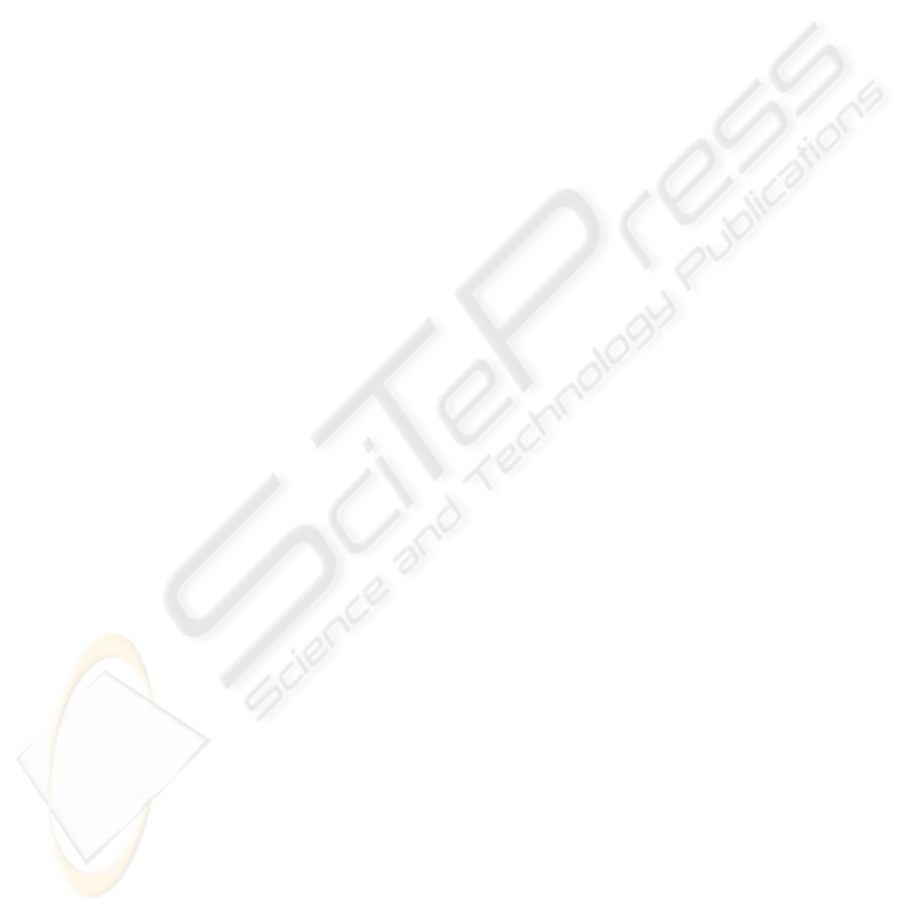
the assembly costs occurred in the assembly
planning scheme.
Traditionally, the assembly sequence is
determined by evaluating the assembly cost
objective. In this case, although a low assembly cost
can be achieved, it may cost more to disassemble the
product at the end of the product life cycle. The key
issue is that an assembly operation with a low cost
may not correspond to a disassembly operation with
the same low cost. In some cases, if a relatively low
cost is used for fixing the two specific components,
it may require a higher cost to perform the
corresponding disassembly operation for separating
the two components. As a result, an assembly
sequence with a low cost may result in a
disassembly sequence with a high cost for the same
product at the end of the product life cycle.
Therefore, a complete decision support system
must include both assembly planning and
disassembly planning. To deal with the special
characteristics of a complete product life cycle,
organizing and sequencing of assembly and
disassembly operations must be considered
concurrently in order to generate an integrated
sequence.
In the related research for assembly planning, it
can be summarized that assembly planning can be
performed in three stages: (1) assembly modelling
and representation, (2) assembly sequence
generation, and (3) assembly evaluation and
optimization. A recent review can be found in
Abdullah et al. (2003). The previous research in
assembly planning can be classified into three
categories. The first category uses rules or
knowledge bases to perform generation of different
assembly sequences such as developed in DeFazio
and Whitney (1987), Heemskerk and Van Luttervelt
(1989), Ye and Urzi (1996), and Swaminathan and
Barber (1996). The second category presents
automatic generation of feasible assembly
sequences using graph representation forms
including the research presented in de Mello and
Sanderson (1991), Santochi and Dini (1992), Lin
and Chang (1993), and Choi et al (1998). The third
category focuses on assembly analysis and
evaluation for searching the better or the optimal
assembly sequence. The research in this class
includes de Mello and Sanderson (1991), Ben-
Arieh, and Kramer (1994), Laperriere and
ElMaraghy (1996), Gottipolu and Ghosh (1997),
Tseng and Liou (2000), and Chen et al. (2004).
With a given set of components, sequencing a
given set of components may become a
combinatorial problem with an explosive number of
potential sequences. From a mathematical point of
view, this is an NP-hard problem with the number of
assembly and disassembly sequences proportional to
the factorial of number of components. From the
solution aspect, genetic algorithms (GAs) have been
proven to be effective and efficient in solving NP-
hard problems such as TSP (traveling salesman
problem). In the research by De Lit et al. (2001),
Chen et al. (2002), Marian et al. (2003), Li et al.
(2003), and Smith (2004), GA method has been
applied to find solutions in assembly planning
models.
In this research, a decision support system for a
complete life cycle management by integrating
assembly and disassembly planning is presented.
First, two graph-based models called assembly
precedence diagram and disassembly precedence
diagram are presented to represent the spatial
relationships of the components and the associated
precedence relationships of assembly and
disassembly operations. Next, two precedence
matrices called assembly precedence matrix and
disassembly precedence matrix are built for
checking the feasible sequences. Finally, several
operation cost functions are developed to evaluate
the costs of the integrated assembly and disassembly
sequences. A method using the genetic algorithm
(GA) approach is developed for finding the solutions
with an objective of minimizing the costs.
In this paper, section 2 presents the graph-based
representation models for integrating assembly and
disassembly planning. Section 3 discusses the cost
functions for evaluating the sequences. Section 4
presents a GA method for finding the solutions.
Section 5 discusses the test results with an example.
Finally, section 6 concludes this study.
2 REPRESENTATION MODELS
The input of the decision support system includes
the definitions of the components, the spatial
relationships of the components, the available
assembly and disassembly operations, and the
associated assembly and disassembly costs. Two
graph-based models are presented to represent the
integrated assembly and disassembly sequences.
The graph-based models can be summarized as
follows.
(1) Assembly precedence diagram (APD),
(2) Disassembly precedence diagram (DPD).
An assembly precedence diagram (APD) is a
directed graph showing the precedence of the
components and the associated assembly operations
(Lin and Chang, 1993). In this research, the concept
of APD is applied to represent the spatial
connectivity relationship and precedence between
A DECISION SUPPORT SYSTEM FOR INTEGRATED ASSEMBLY AND DISASSEMBLY PLANNING USING A GA
APPROACH
349