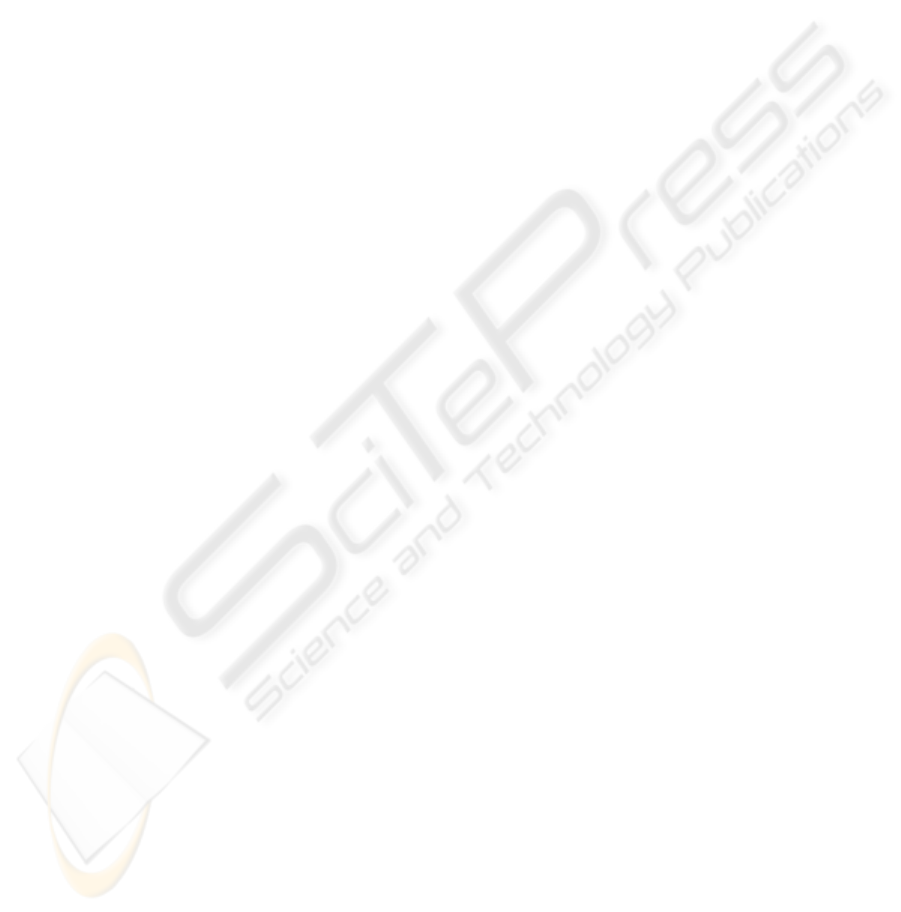
(plant management) module. Maintenance plans are
developed with a 12 months time horizon and
include a list of tasks for the same period. At the
start of each month, monthly work requests are
released. There is a budget allocated for carrying out
these maintenance activities. However, there is little
provision of emergency repairs, for example if the
failure at the station requires replacement of small
component or a minor treatment; it is attended to by
the maintenance crew at the station. However, in
case of major failure, maintenance requires approval
from various levels as well as needs commissioning
of expertise and resources and therefore takes time.
OzDrop differentiates between maintenance and
asset ownership, i.e. work is executed by
maintenance crew, whereas asset ownership is the
mandate of another function. Consequently, there
are multiple versions of the same information within
the organization. Furthermore, these versions have
their own bias and standard of quality. Although the
organisation is aware of the potential of quality
information, yet there is little emphasis made on
recording and capturing correct and complete
information. For example, a maintenance engineer
summarised the situation as under, ‘maintenance
crew is not technically qualified or capable to
operate an IT system. They consider it as an add-on
to maintenance work, something that just has to be
recorded. At the end of the day they will not be
judged on what information they entered. Their
performance is evaluated on the quality of their
maintenance work’ - Maintenance Engineer.
Maintenance information, however, is crucial for
asset lifecycle management, as it provides the basis
for lifecycle cost benefit analysis, remnant lifecycle
calculations, as well as for asset refurbishment,
upgrade, and overhauls. However, like other
functions, maintenance information is not exchanged
with other lifecycle functions. In addition, the main
focus is on capturing maintenance execution
information with little provision for integrating this
information with financial information.
Consequently, there is no way of calculating the cost
of failure as well as real costs incurred on
maintaining the asset. OzDrop’s finance manager
noted that, ‘There is fixed maintenance cost which is
the routine day to day maintenance, and then there
is what we call renewals program or refurbishment
program. This is what you would call the irregular
lumpy parts of your maintenance over the life cycle
of the asset. We have always separated out
refurbishment or renewals program from
maintenance program. Most organizations will
clump it together because you have to clump it
together to get any kind of resource planning, but
yes, we are not using the financial indicators as
input into reinvestment or investment in assets’ -
Finance Manager.
4.5 Operational Responsiveness
IS in OzDrop are primarily being used for recording
information or what could be best described as
recording what the organisation has done. This
information is seldom used for more high profile
purposes, such as organisational integration,
planning, and executive decision support. The
prevailing silo approach has affected departmental
efficiency as well as functional integration.
Management at OzDrop takes a deterministic view
of technology and aims more at the perceived
benefits from technology than the cause and effect
relationships that enable these benefits. User
training has traditionally been a weak area at
OzDrop. Little training is provided and even that is
aimed at training managers and supervisors rather
than the staff who use the system on daily basis. The
idea is that the supervisory staff (with the help of IT
department) train functional staff. In these
circumstances it is obvious that staff do not feel
comfortable with using major platforms such as
SAP, and business units in OzDrop are more
inclined towards using internally developed
spreadsheets and databases. Due to little information
exchange the company faces substantial knowledge
drain.
Senior management is not technology savvy and
therefore does not rely on IT for asset lifecycle
decision support. Even otherwise information lacks
quality and there is no way of managing the
important asset lifecycle learning. OzDrop depends
a lot on the tacit knowledge (particularly for
maintenance) and at present more than 65% of the
staff at OzDrop are within 10 years of retirement
age, which means substantial amount of intellectual
capital loss. A senior manager from OzDrop
attributes this to the culture of the company and
summarises that, ‘it has a lot to do with culture. Our
culture is wrestling with fundamental issues. Some
would argue that we are in an asset based industry
and not an intellectual property based industry or
anything like that. Certainly true to say that there is
a difference of opinion in the organisation as to how
asset portfolio should be managed through IS.
Perhaps people are not trained or skilled for the
organisation to change. IS implementation needs to
be addressed a little more strategically. We have to
try to convert people from break down heroes into
more strategic thinkers’ - Group General Manager.
IS BASED ASSET MANAGEMENT - An Evaluation
297