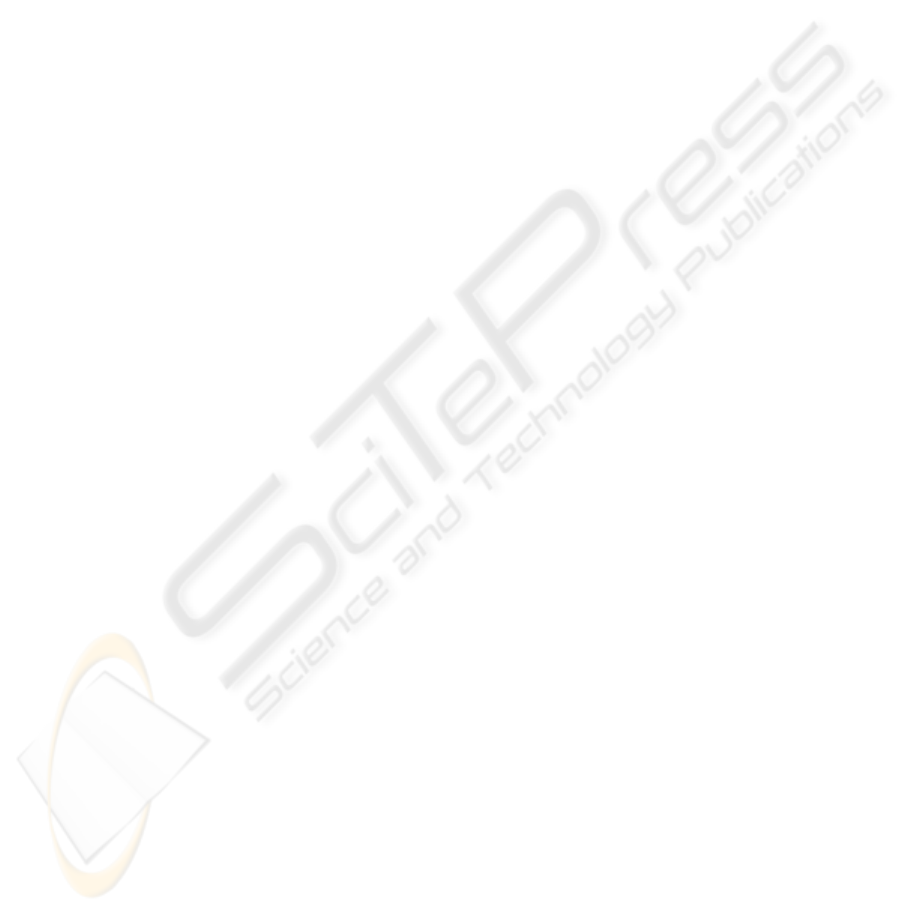
which is considerably more complex than the retail one, from a temperature control
point of view.
3 Technological Solutions for the Cold Supply Chain
The most interesting technological solutions available to monitor the cold supply
chain are the Time Temperature Indicators (TTI), the Data Loggers, the semi-passive
RFId (Radio Frequency Identification) tags and the Wireless Sensor Networks
(WSN).
TTIs are smart labels that help verify whether perishable goods have been exposed
to harmful temperatures during their transit or storage. Placed directly on the
packaging of each single product, they provide an easy-to-read visual indication of the
accumulated time and temperature history of a product. [5]. In order to assure an
acceptable level of reliability, TTIs require a preliminary study on how the product
deteriorates and on how the TTI responds to a temperature change. Although applied
directly on product and so enabling continuous control of the cold chain, real-time
management is not possible, since actions can be taken only after the problem has
occurred. Moreover, the intensity of the problem is not measured, and a small break
of the cold chain will be reported in the same way as a severe one.
Data Loggers are probably the most widespread tool for temperature monitoring.
They are medium-sized electronic devices, with a separate power source (e.g. vehicle
battery) that collect and record data over time. Unlike the TTIs, the Data Loggers
support real-time response, and alarms can be generated. The main disadvantage is
that they monitor the temperature of air and not that of product, being positioned on
the containers. Moreover, they do not provide any information on what happens when
and where the Data Loggers are not present (e.g. loading/unloading activities).
Radio Frequency Identification (RFId) is an automatic identification technology
with which data can be stored and remotely retrieved data using small devices called
RFId smart tags. For temperature monitoring, semi-passive tags have to be used, with
a small battery on board to power the sensor, while the communication ability still
relies on passive RF data exchange. Their working principle is similar to that of a
Data Loggers but, being much smaller and power independent, they can be physically
put onto products: cost reasons make it impossible to tag each single product, but with
a careful selection of tag positioning a continuous monitoring capability can be
achieved. Moreover, they can use RF communication for a quick data download, even
if a specific hardware and software infrastructure has to be put in place to interrogate
the tags (with a reading distance of about 5-7 meters for UHF semi-passive tags); in
this regard, they do not allow for real time control, since they have to be interrogated
to communicate that a temperature shock has occurred [6].
Wireless Sensor Networks are mesh networks consisting of spatially-distributed
autonomous tags (nodes) endowed with sensors to monitor any physical parameters of
their environment cooperatively. Sensor nodes are very small computers consisting of
a processing unit with limited computational power and memory, one or more
sensors, a wireless communication device and a power source (e.g. a battery) [6]. As
for the RFId semi-passive tags, the nodes are very small, and can be put within the
shipped batch, even though not on each single product, and data can be automatically
151