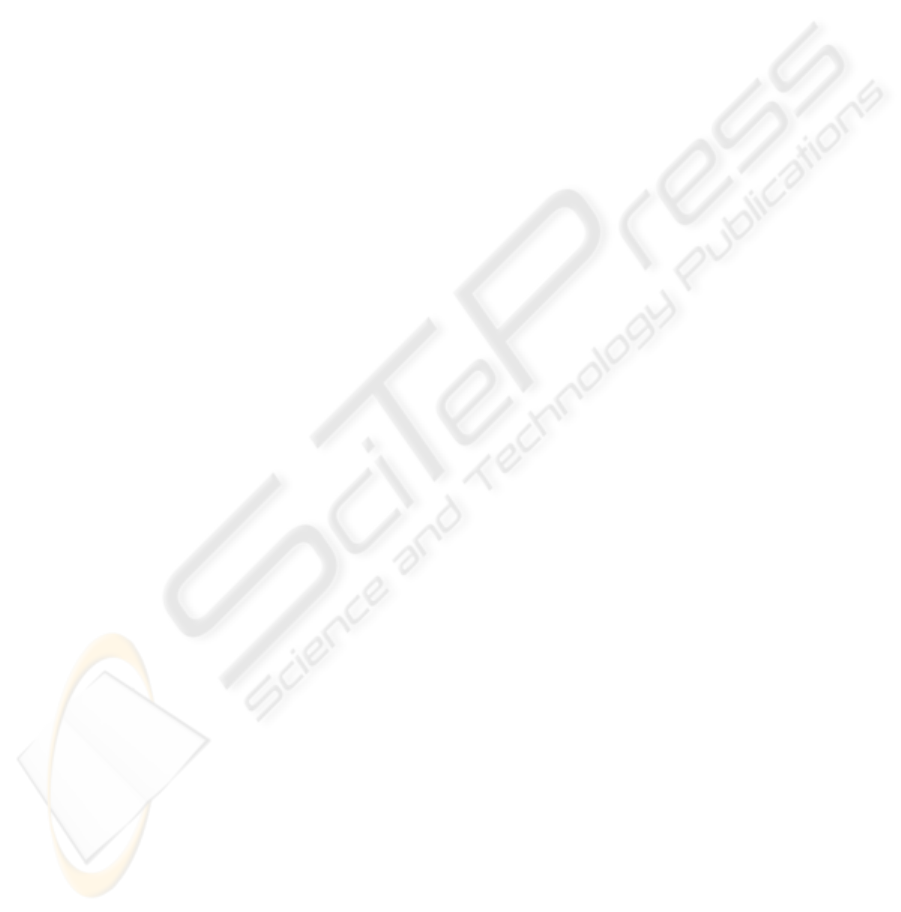
IDs, hence, is mandatory, in order to effectively transmit the measured value. This is
done in a non-direct way, without modifying the RFID internal logic.
Such a theoretical approach, here generically called “multi-ID”, can be practically
implemented by following at least two different strategies: on one side the “multi-
chip” tags strategy, with RFID tags consisting of only one antenna and many chips,
each one with its own ID code (see Fig. 2). On the other, the “multi-tag” strategy,
where each ID is transmitted with a different tag controlled by appropriate RF inte-
grated switches. Both of them have been realized and tested by the authors. Even
though some interesting differences could be discussed, for the sake of brevity we
omit here any further detail and we indifferently refer in the following to multi-ID S-
Tag, regardless to the actually implemented strategy.
In Figure 2, for instance, the data measured from a sensor is used to control the inte-
grated RF switches which select the appropriate IDs to be transmitted. Actually, the
S-Tag being a general-purpose device, the sensor signal must be preventively quan-
tized through an ad-hoc circuit embedded in the S-Tag. Of course, the number n of
bits used for the quantization must be equal to the number of IDs. It is evident that 2
n
-
1 different configurations are admissible, so that n must be accurately chosen depend-
ing on the desired accuracy.
In Fig. 3, the illustrative scheme of the realized S-Tag is sketched. The circuit repre-
sents a 4-tag RFID transponder that allows 15 ON/OFF tag combinations (2
4
-1, one
of them being not allowed) corresponding to 15 different sensor parameter values. In
particular, the four tags we used belong to the family Gen 2 Squiggle™ ALN-9540
EPC Class 1 (860-960 MHz). Each tag is activated/de-activated by high frequency
switches, operating with 2 switching pins controlled by 4 pins of a CMOS integrated
circuit. All four inverters are then controlled by a 6-pin connector, that is directly
connected to the external sensor system. This is composed of a sensor circuit with a
digital output (e.g. a temperature probe) and a control software that has been imple-
mented ad hoc for this application.
3 Results
In order to test the proposed S-Tag in a practical application, the case of the remote-
healthcare previously introduced in Section I and represented in Fig. 1, is considered.
More specifically, the body-temperature of a patient is remotely monitored through a
temperature probe (a thermometer) connected to the S-Tag (tagged patient). It is
worth highlighting, though, that for the sake of brevity, reported results are focused
only to temperature detection, but there is no restriction neither in the number of
sensors, nor in the sensor typology. Details related to other parameters (such as pres-
sure, pH) will be given in the oral presentation. In Fig. 4 some results showing the
time variations of temperature in correspondence of an ideal situation (for clarity
purposes, temperature has been varied faster than reality, the temperature of a patient
being supposed to normally vary much slower) are graphed. Provided that the model
seems to respond in a very good way to the fast temperature variations, this is no
doubt true also in the slower case. Here, the RFID reader is supposed to be at differ-
ent distances from the tagged patient and temperature variations are imposed by an
178