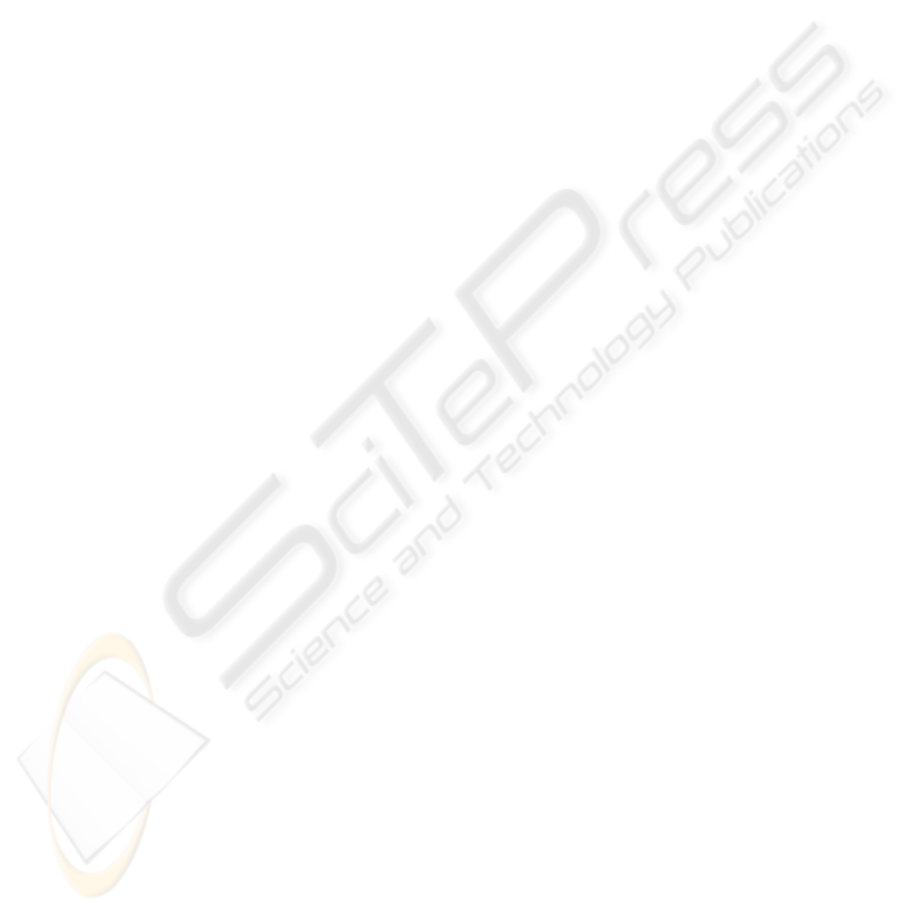
difficult for any kind of process improvement
mechanism to be employed if the process in question
cannot be properly observed. As stated in section 4,
our future research in this field will entail an
improved and more comprehensive mechanism for
recommendation provision and also a
mathematically formal model for severity
determination.
REFERENCES
Cangussu, J.W., DeCarlo, R.A., and Mathur, A.P. 2003.
Monitoring the software test process using statistical
process control: a logarithmic approach. Proceedings
of the 9th European software engineering conference
held jointly with 11th ACM SIGSOFT international
symposium on Foundations of software engineering
ESEC/FSE-11. 28, 5 (September 2003). ACM Press.
Card, D. 1994. Statistical process control for software?
IEEE Software. 11, 3 (May 1994). 95 – 97.
Cîmpan, S., and Oquendo, F. 2000. Dealing with software
process deviations using fuzzy logic based monitoring.
ACM SIGAPP Applied Computing Review. 8, 2
(December 2000). ACM Press.
Cook, J.E., and Wolf, A.L. 1998. Discovering models of
software processes from event-based data. ACM
Transactions on Software Engineering and
Methodology (TOSEM). 7, 3 (July 1998).
Cugola, G., Di Nitto, E., Fuggetta, A., and Ghezzi, C.
1996. A framework for formalizing inconsistencies
and deviations in human-centered systems. ACM
Transactions on Software Engineering and
Methodology (TOSEM). 5, 3 (July 1996). ACM Press.
Dowson, M., Nejmeh, B., and Riddle, W. 1990. Concepts
for Process Definition and Support. Proceedings of the
6
th
International Software Process Workshop
(Hakodate, Japan, October 28-31 1990). IEEE
Computer Society Press.
Ferrin, D.M., Miller, M.J., and Muthler, D. 2005. Six
Sigma and simulation, so what's the correlation?
Proceedings of the 37th conference on Winter
simulation (December 2005). WSC '05. Winter
Simulation Conference.
Florac, W.A., and Carleton, A.D. 1999. Measuring the
Software Process: Statistical Process Control for
Process Improvement, Addison-Wesley.
Florac, W.A., Carleton, A.D., and Barnard, J.R. 2000.
Statistical Process Control: Analyzing a Space Shuttle
Onboard Software Process. IEEE Software. 17, 4
(July/Aug 2000). 97 - 106.
Herlocker, J.L., Konstan, J.A., Terveen, L.G., and Riedl,
J.T. 2004. Evaluating collaborative filtering
recommender systems. ACM Transactions on
Information Systems (TOIS). 22, 1 (January 2004).
ACM Press.
Huo, M., Zhang, H., and Jeffery, R. 2006. An Exploratory
Study of Process Enactment as Input to Software
Process Improvement. Proceedings of the 28th
International Conference on Software Engineering
(Shanghai, China, May 2006). ICSE '06. ACM Press.
Jalote, P., and Saxena, A. 2002. Optimum control limits
for employing statistical process control in software
process. IEEE Transactions on Software Engineering.
28, 12 (Dec. 2002), 1126 – 1134.
Lantzy, M.A. 1992. Application of statistical process
control to the software process. Proceedings of the
ninth Washington Ada symposium on Ada:
Empowering software users and developers (July
1992). ACM Press.
McNee, S.M., Riedl, J., and Konstan, J.A. 2006. Work-in-
progress: Making recommendations better: an analytic
model for human-recommender interaction. Extended
abstracts on Human factors in computing systems
(April 2006). CHI '06. ACM Press.
Radice, R. 2000. Statistical Process Control in Level 4 and
Level 5 Software Organizations Worldwide. The
Twelfth Annual Software Technology Conference, Salt
Lake City, Utah, May 4, 2000.
Reese, J.D., and Leveson, N.G. 1997. Software deviation
analysis. Proceedings of the 19th international
conference on Software engineering (May 1997).
ACM Press.
Rezgui, Y., Marir, F., Cooper, G., Yip, J., and Brandon, P.
1997. A Case-Based Approach to Construction
Process Activity Specification. Intelligent Information
Systems (December 8-10, 1997) IIS '97. 293 – 297.
Rombach, H.D. 1990. Specification of software process
measurement. Proceedings of the 5th international
software process workshop on Experience with
software process models (October 1990). IEEE
Computer Society Press.
Thompson, S., Torabi, T., and Joshi, P. 2007. A
Framework to Detect Deviations during Process
Enactment. 6th IEEE International Conference on
Computer and Information Science (Melbourne,
Australia, July 11–13, 2007). IEEE Computer Society
Press.
Thompson, S., and Torabi, T. 2007. A Process
Improvement Approach to Improve Web Form Design
and Usability. The 3rd Ubiquitous Web Systems and
Intelligence Workshop (Regensburg, Germany,
September 3-7, 2007). UWSI 2007 Colocated with
DEXA 2007.
VanHilst, M., Garg, P.K., and Lo, C. 2005. Repository
mining and Six Sigma for process improvement.
Proceedings of the 2005 international workshop on
Mining software repositories. 30, 4 (May 2005). MSR
'05. ACM Press
Wang, Q., Jiang, N., Gou, L., Liu, X., Li, M., and Wang,
Y. 2006. BSR: a statistic-based approach for
establishing and refining software process
performance baseline. Proceedings of the 28th
International Conference on Software Engineering
(Shanghai, China, May 2006). ICSE '06. ACM Press.
DETERMINING SEVERITY AND RECOMMENDATIONS IN PROCESS NON-CONFORMANCE INSTANCES
133