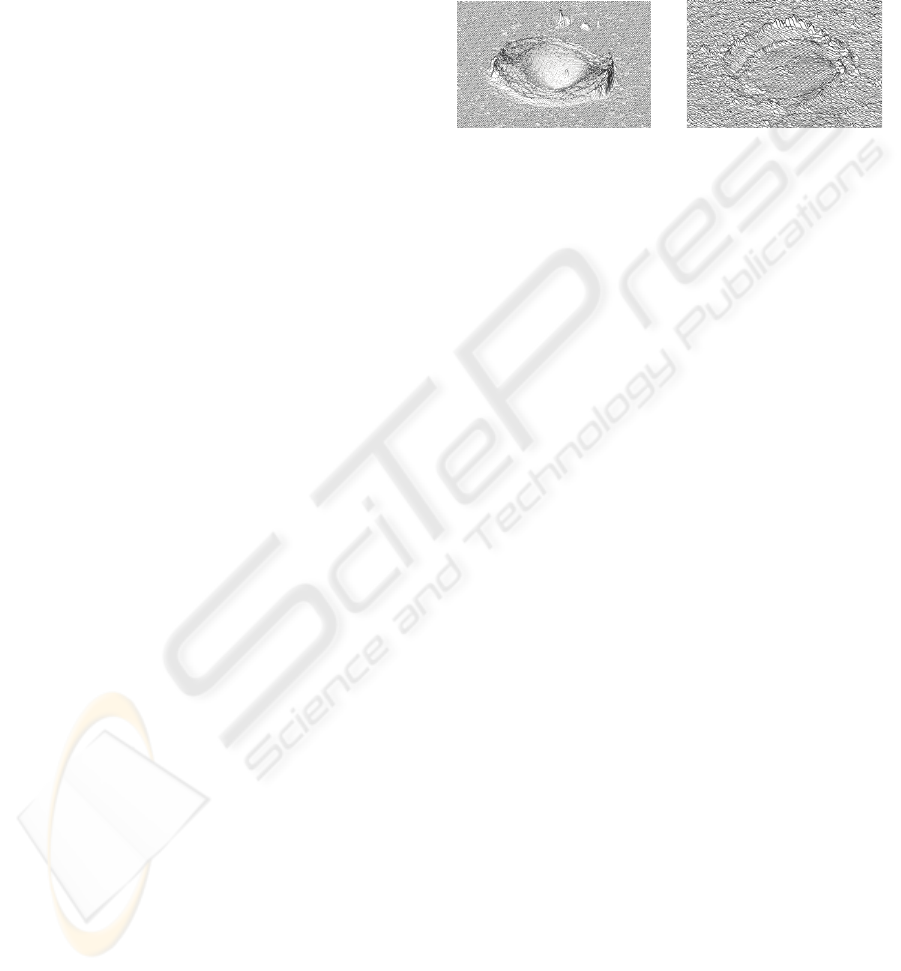
2.2 Simulation Approach
As it was described in (Hájková and Herout, 2008),
we decided to use for the simulation the application
approach.
The pulses are extracted from input data for
given combination of used material and laser setting.
The basic technique of simulation of samples
burning is to place selected pulses gained from input
data on the surface of the unburned material. The
format of the pulse is designed for the simplest
usage as possible and it offers the ability of direct
pulse application on the surface of the material (as it
was described in the previous sections).
The simulation itself requires solving of many
problems (e.g. heating of the material during
repetitive burning of laser ray into one point of the
material, influence of the material surface roughness
on the laser ray reflection or inaccuracies caused by
starting and finishing laser motion).
For the correct function of the simulation the
system has to be verified. During the verification the
burned samples are compared with the real ones,
which are gained by the same method as it was
described in Section 2.1. To test and evaluate the
system in a more global way a broad range of
samples has to be simulated and compared. An
automatic verification is used for speeding it up.
3 METHODS FOR AUTOMATIC
PULSE DETECTION
Pulse detection is used as a part of data
preprocessing. The task of detection is to define the
area of the material surface which was affected by
the laser burning as exactly as possible. Pulse
detection can be done of course manually but for the
speedup and simplification of the whole preparation
process, the system has to prepare maximum of parts
self-containedly. But the precision and accuracy has
to be preserved as well with the automation process.
That is why we have to develop appropriate
algorithm for pulse detection.
The main problem is the roughness of the basic
material surface. As it can be seen in
Figure 3 for
some materials, such as for a steel in
Figure 3a, the
surface is quite smooth. Another situation comes in
the case of cermet (
Figure 3b), where the protrusions
on the material surface are more noticeable.
Moreover, for all types of material also local
roughnesses which are not specific for the material
can appear. Such defects need not to be visible on
the material surface by naked eye, but thanks to the
height resolution of real sample scanning, they are
included in the description of the sample and are the
source of problems during the pulse auto-detection.
Local roughness can be seen in
Figure 3a on the
upper side of the sample.
a) b)
Figure 3: a) Surface of steel with relatively smooth
surface; local defect can be seen on the upper side of the
sample. b) Surface of cermet sample with globally higher
roughness of the surface.
The user is able to distinguish roughness or
defects of the material during the manual pulse
detection, but for the automatic method it is very
difficult to differentiate these inaccuracies from the
border of the pulse. Chosen methods have to be
precise enough, but very precise methods are already
slow. Quickly working methods are unfortunately
inaccurate. That is why we have to find a
compromise and to create a new method designed
right for this task.
3.1 Global Extremes Method
The first version of detection algorithm goes from
unmodified sample surface. The algorithm starts
from points with the minimal and maximal height.
These points are supposed to be in the area of the
burned pulse that should be detected. From their
position columns of height map to the left and to the
right side are inspected and the height difference of
points in each single column (it means the difference
between the maximal and minimal value in the
column) is counted. If the value does not exceed
given height limit, an inspection in the direction is
finished. After cutting of columns on the left and
right side of the pulse, the same process of border
searching is started for rows. Horizontal borders are
appointed.
There is a question how to gain the value of
difference height limit. This is one of problems of
this algorithm. If we do not want to set the constant
manually we have to explore the sample
automatically, for example during its loading into
the system. We can suppose that borders of the
sample are not modified by the burning and that is
why they represent the original material surface and
ICSOFT 2008 - International Conference on Software and Data Technologies
188