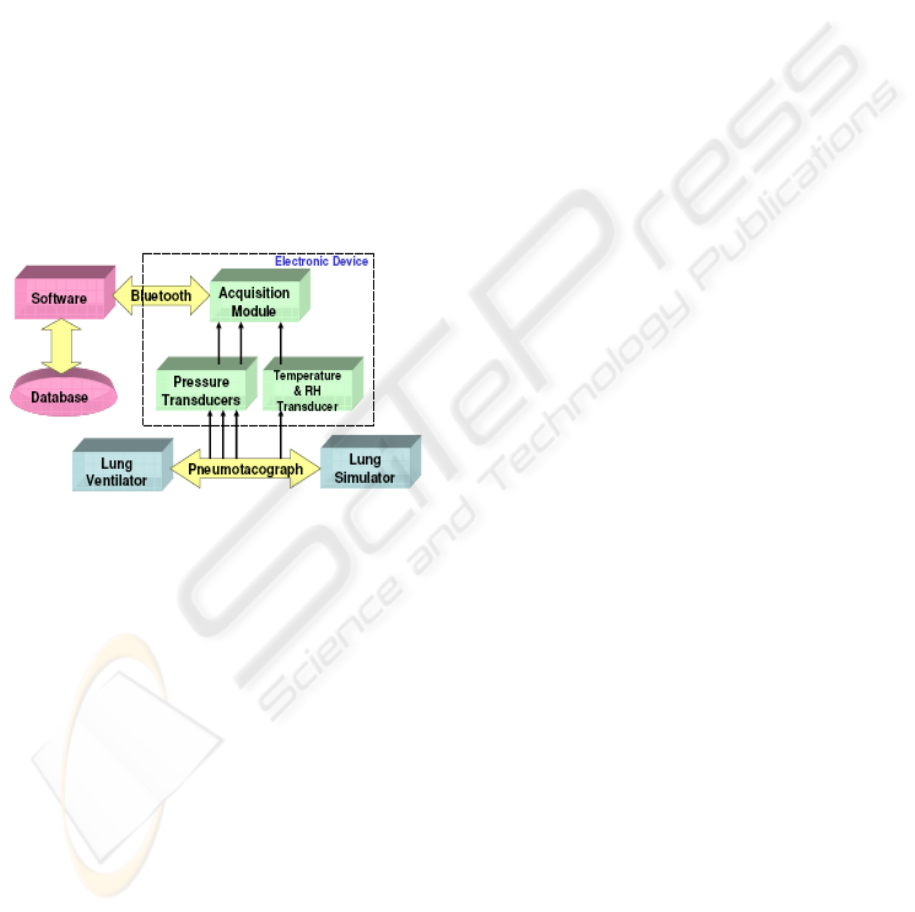
evaluate the LV are calculated. All data are stored in
a database.
2 MATERIALS AND METHODS
The Figure 1 depicts a block diagram of the
developed system and shows how it is connected to
the LV and lung simulator (LS). The LS acts as a
physiological load (resistance and compliance) for
the LV under assessment.
The developed system consists of an electronic
device that periodically measures the temperature
and relative humidity (RH) of the air inside the duct
that connects the LV to the LS as well as the flow
and the pressure waveforms generated by the LV.
The acquired data are sent to a PC microcomputer
via radio frequency (RF). The PC shows the sampled
data on the screen as well as parameters required by
the IEC 60601-2-12.
Figure 1: Block diagram of the system developed to assess
LV performance. It also shows how the system is
connected to the LV and LS.
The next sections describe each block of the
developed system.
2.1 Transducer Module
The transducer used to measure temperature and
relative humidity (RH) is the SHT75 (Sensirion Inc,
2007). It measures temperature from -40 to 123.8°C
(accuracy: ±0.5°C; resolution: 0.01°C) and RH from
0 to 100%RH (accuracy: ±1.8%RH; resolution:
0.03%RH). These transducers have a calibration
certificate issued by the manufacturer.
Due to its small size (0.42 x 4.88 x 2.5 mm), it is
possible to insert the transducer into the air duct that
connects the LV to the LS.
The SHT75 yields the measurements in digital
format (14 bits) via a 2-wire protocol. This is a
bidirectional protocol that allows the sensor to
receive data such as commands to carry out the
measurements.
Before connecting the LV to the LS, the sensor is
exposed to the environment, allowing the system to
register the local temperature and RH.
To sample the flow and pressure produced by the
LV, two DC030NDC4 pressure transducers are used
(Honeywell Inc., 2008). The DC030NDC4 measures
the differential pressure applied to its inputs in a
range of ±76.2cmH
2
O. It has a sensitivity of
52.36mV/cmH
2
O, producing a voltage output of
2.25V ± 2.0V.
An acrylic apparatus containing an obstacle is
placed between the LV and LS to create resistance to
the gas flow (pneumotacograph - PT). The pressure
drop across the resistance, measured by one of the
transducers, is proportional to the flow velocity
(Doeblin, 1990). The Figure 2 shows how the
transducer inputs are connected to the PT apertures
as well as a front view of the flow resistance. The
pressure drop is positive for inspiratory flow and
negative for expiratory flow.
To relate the A/D converter voltage input (that is,
the amplified and filtered differential pressure
transducer voltage output) to flow, 40 different flow
rates (20 positive and 20 negative) were applied to
the PT and to a calibrated flow meter (Fluke
Biomedical VT-Plus; uncertainty of ±1,1l/min for
the -70 to +70l/min range). They were connected in
series to allow the comparison of their
measurements. An illustration of the experimental
setup is shown in Figure 3. A polynomial of seventh
order was fitted to the experimental points (voltage
input versus flow rate measured by the calibrated
meter) to allow inferring measures for flow rates not
evaluated. Using the polynomial, the flow
measurements obtained with the developed system
have an uncertainty of ±4.4l/min.
The second transducer, connected to a third
aperture of the acrylic device, measures the
difference between the atmospheric pressure and the
one within the air duct.
To calibrate this transducer, 35 pressure values
(from 0 to 37.1cmH
2
O) were applied to the
transducer and, in parallel, to a calibrated meter
(Fluke Biomedical BP-Pump 2; uncertainty:
±0.2cmH
2
O for a range from 0 to 120cmH
2
O). The
conditioned voltage output of the transducer (as
supplied to an A/D input) and the pressure readings
obtained from the calibrated meter were annotated.
From these values, a first order polynomial
between voltage and pressure was obtained.
BIODEVICES 2009 - International Conference on Biomedical Electronics and Devices
162