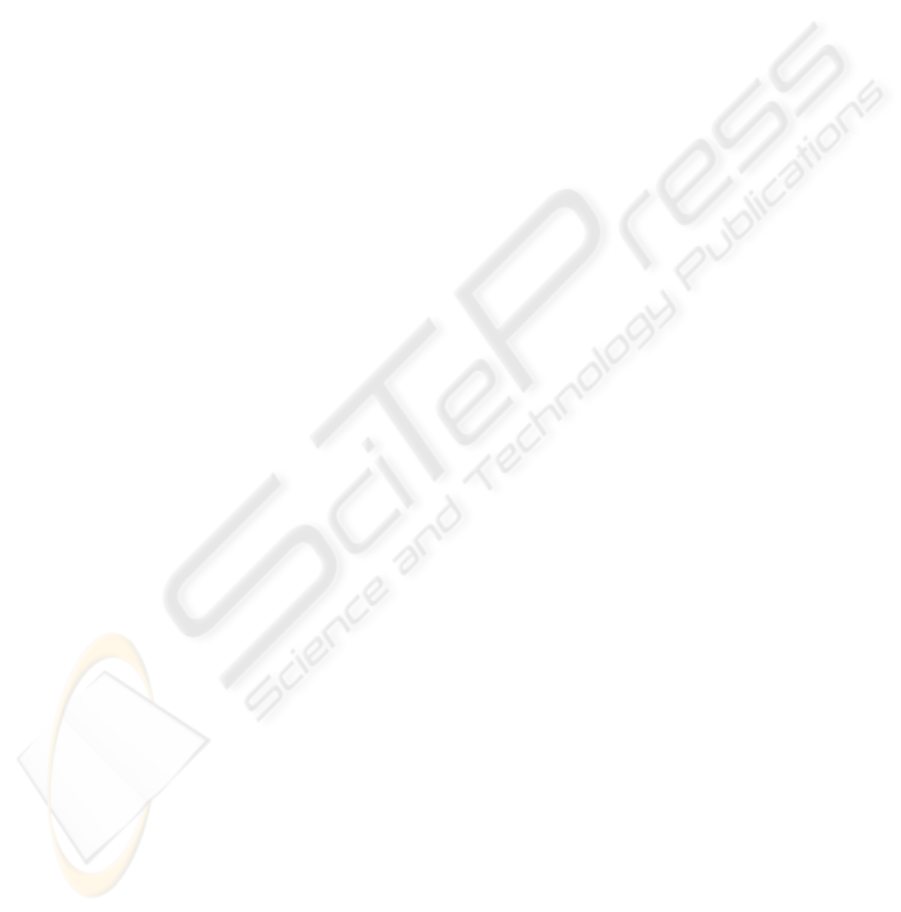
signals. The measured dynamic range is 10µs.
Several researchers have reported the design of
TDC for PET imaging systems. An integrated
CMOS sub-nanosecond TDC has been developed
under the aid of flash ADC technology. The time
resolution is reported as 312.5ps (Brian K. Swann et
al., 2004). In addition, a 224ps-resolution TDC
based on DLL technology was reported for liquid
Xenon PET (Bourrion and Gallin-Martel, 2006). The
prototype chip of such TDC included a single DLL
with 128 delay cells. It was difficult to deal with the
mismatch of long-chain delay cells. For obtaining
smaller time resolution, a new architecture based on
a hierarchical delay processing structure was
proposed for next generation PET imaging (Yousif
and Haslettl, 2007). A prototype chip was fabricated
in 0.13µm CMOS process and ran at a clock of
500MHz. Although high resolution was obtained, a
faster technology was needed due to the high-
frequency clock utilized in the chip.
Few studies have been done on development of a
TDC that a better resolution obtained by using either
a faster technology for PET imaging applications.
However, a two-level conversion scheme based on
an array of DLLs is a good solution for this
challenge. The original proposals of TDC based on
array of DLLs have been published in (Christiansen,
1996), (Mota and Christiansen, 1998). A resolution
of 89.3ps was realized with a clock frequency of
80MHz (Mota and Christiansen, 1998). In this
paper, we present the design of a TDC based-on an
array of low-jitter DLLs for PET imaging system.
The results agree with the design of TDC’s in
(Christiansen, 1996) and (Mota and Christiansen,
1998). The better results are achieved because low-
jitter DLLs are employed and the relatively
advanced CMOS technology (0.35µm) is utilized.
The resolution of 71ps with a clock frequency of
100MHz is obtained from our prototype chip.
In Section 2 of this paper, the principle of
measurement and proposed architecture are
described. In Section 3, the description of circuits is
given. In Section 4, a prototype chip of TDC and
experimental results are described. Section 5
concludes the paper.
2 OPERATIONAL PRINCIPLE
AND PROPOSED
ARCHITECTURE
TDC systems are designed to measure the time
interval from START to STOP signal. For large time
interval, a counter is employed to counter numbers
when a reference clock is used. The measured time
equates to the counted number multiple by the
period of the clock. The resolution of TDC is
depended on the period of reference clock. If smaller
time tap is needed, a high-frequency clock needs to
be employed. Another solution is two-level
conversion scheme. The counter is employed for
coarse conversion and a multiphase sampling
technology is proposed for fine conversion. The
multiphase generators are designed to generate
multiphase delayed in one period of the reference
clock. The state of multiphase will be asserted,
registered and converted to binary codes.
A delay-locked loop (DLL) is usually employed
as a multiphase generator. In the DLL, the reference
clock is propagated through voltage-controlled delay
line (VCDL). The output signal at the end of the
delay line is compared with the reference clock. If
the delay difference from integer multiples of clock
period is detected, the closed loop will automatically
correct it by changing the delay time of VCDL. A
DLL can be locked to one clock if the initial delay of
VCDL is located between 0.5T
clk
and 1.5 T
clk
(Chang
et al., 2002).
Figure 1 shows the operational principle of TDC
for small animal PET imaging system. The system is
reset with a cycle period of 10µs. The reset signal,
so called as Hit_clear in Figure 1, is the START
signal of TDC. A “Hit” signal generated by extern
pulse of an event is the STOP signal. The time
interval between the falling edge of Hit_clear and
the rising edge of Hit are measured by TDC chip. In
coarse conversion level, a counter is utilized to count
numbers. The counter commences to count at the
falling edge of Hit_clear and is interrupted while a
rising edge of “Hit” signal arrives. The last number
is read out as coarse data . In fine conversion step,
the delayed clock is generated by multiphase
generator. The state of the multiphase is readout by
rising edge of Hit signal. The acquisition data is then
converted to binary code. The total time can be
described as,
T
tdc
= N
c
× T
ref
+ N
f
× T
bin
(1)
Where, T
tdc
is the total time measured by TDC;
N
c
and N
f
are coarse and fine data, respectively; T
ref
and T
bin
are reference clock period and bin size of
TDC, respectively.
In the architecture based on two-level conversion
scheme, multiphase generators become the key part
of the whole design. As a solution, an array of DLLs
is proposed. An important advantage of array of
DLLs is that better resolution (less than 100ps) can
IMAGAPP 2009 - International Conference on Imaging Theory and Applications
172