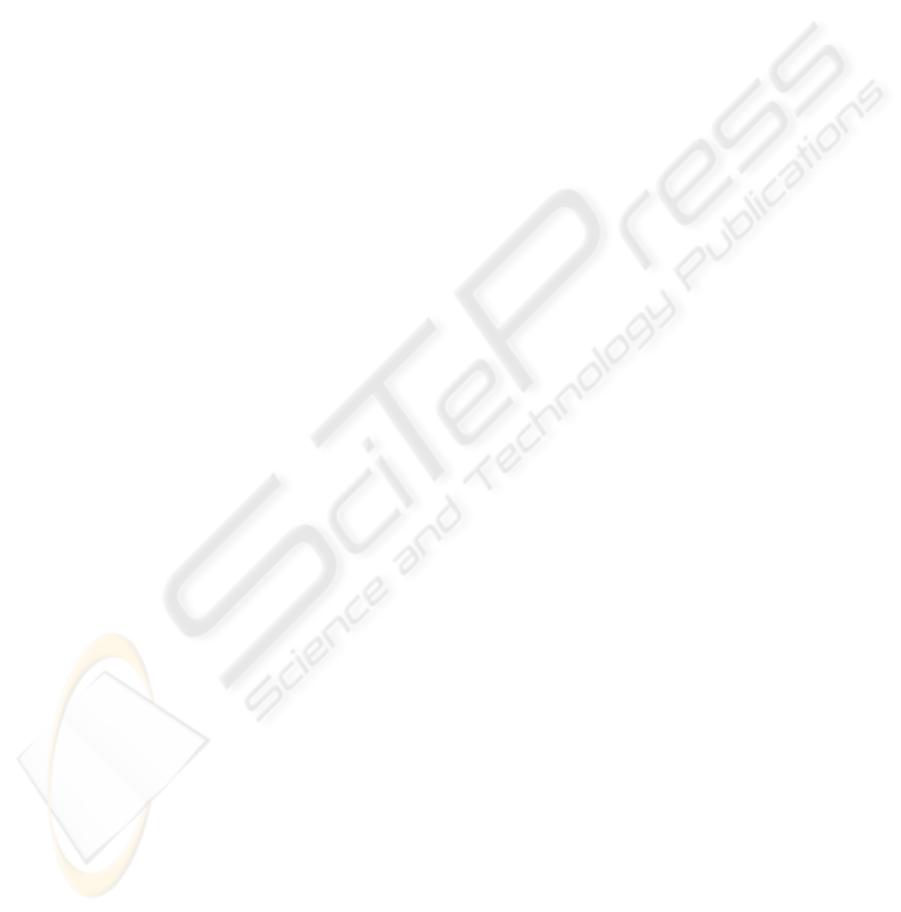
ACM Transactions on Graphics, Vol. 27, No. 3,
pp.83:1-9, August 2008.
Buades, A., Coll, B., and Morel, J. 2005. A Review of
Image Denoising Algorithms, With a New One,
Multiscale Modeling and Simulation (SIAM
interdisciplinary journal), Vol 4 (2), pp. 490 - 530.
Chantler, M., and Spense, A. 2004. Apparatus and Method
for Obtaining Surface Texture Information, Patent GB
0424417.4.
DIGITAL ICE™, Eastman Kodak Company,
http://asf.com/products/ice/FilmICEOverview/.
Efros, A., and Leung, T. 1999. Texture Synthesis by Non-
parametric Sampling. In Proceedings of IEEE
Internation Conference on Computer Vision,
September.
Fattal, R., Agrawala, M., and Rusinkiewicz, S. 2007.
Multiscale Shape and Detail Enhancement from
Multiple-light Image Collections, ACM Transactions
on Graphics, 26 (3).
Freeth, T., Bitsakis, Y., Moussas, X., Seiradakis, J.,
Tselikas, A., Mangou, H., Zafeiropoulou, M.,
Hadland, R., Bate, D., Ramsey, A., Allen, M.,
Crawley, A., Hockley, P., Malzbender, T., Gelb, D.,
Ambrisco, W., and Edmunds, M. 2006. Decoding the
Ancient Greek Astronomical Calculator known as the
Antikythera Mechanism, Nature, Vol. 444, Nov. 30,
pp. 587 – 591.
Gardner, A., Tchou, C., Hawkins, T., and Debevec, P.
2003 Linear Light Source Reflectometry, ACM
Transactions on Graphics, Vol. 22, No. 3, pp. 749-758.
Hammer, O., Bengston, S., Malzbender, T., and Gelb, D.
2002. Imaging Fossils Using Reflectance
Transformation and Interactive Manipulation of
Virtual Light Sources, Palaeontologia Electronica ·
August 23.
Hastie, T., Tibshirani, R., and Friedman, J. 2001. The
Elements of Statistical Learning - Data Mining,
Inference, and Prediction. Springer-Velag.
Hewlett-Packard G4050 Photo Scanner, 2007.
www.hp.com.
Horn, P. 1986. Robot Vision, MIT Press, ISBN 0-262-
08159-8.
Klette, R., Schluns, K., and Koschan, A. 1998. Computer
Vision: Three-Dimensional Data from Images,
Springer –Verlag.
Kschischang, F. R., Frey, B. J., and Loeliger, H. A. 2001.
Factor Graphs and the Sum-Product Algorithm, IEEE
Transaction on Information Theory, Vol. 47, No. 2.
Malzbender, T., Gelb, D., and Wolters, H. 2001.
Polynomial Texture Maps. In Proceedings of ACM
Siggraph 2001, ACM Press / ACM SIGGRAPH, New
York. E. Fiume, Ed., Computer Graphics Proceedings,
Annual Conference Series, ACM, 519-528.
Medioni, G., Lee,M., and Tang, C. 2000. A Computational
Framework for Segmentation and Grouping, Elsevier.
Onn, R., and Bruckstein, A. 1990 Integrability
Disambiguates Surface Recovery in Two-Image
Photometric Stereo, International Journal of Computer
Vision, vol. 5, pp. 105-113.
Petrovic, N., Cohen, I., Frey, B. J., Koetter, R., and
Huang, T. S. 2001. Enforcing Integrability for Surface
Reconstruction Algorithms Using Belief Propagation
in Graphical Models, 2001 IEEE Conf. on Computer
Vision and Pattern Recognition, vol. 1, pp. 743-748.
Schubert, R. 2000. Using a Flatbed Scanner as a
Stereoscopic Near-Field Camera, IEEE Computer
Graphics and Applications, pp. 38-45.
Toler-Franklin, C., Finkelstein, A., and Rusinkiewics, S.
2007. Illustration of Complex Real-World Objects
using Images with Normals, International Symposium
on Non-Photorealistic Animation and Rendering.
Tu, P., and Mendonca, P. R. S., 2003. Surface
Reconstruction via Helmholtz Reciprocity with a
Single Image Pair, Proc. of 2003 IEEE Computer
Society Conference on computer Vision and Pattern
Recognition (CVPR’03), pp. 541-547.
Yang, J., Ohnishi, N., and Sugie, N. 2003. Two Image
Photometric Stero Method, Proc. SPIE, Intelligent
Robots and Computer Vision XI, Vol. 1826, pp. 452-
463.
VISAPP 2009 - International Conference on Computer Vision Theory and Applications
50