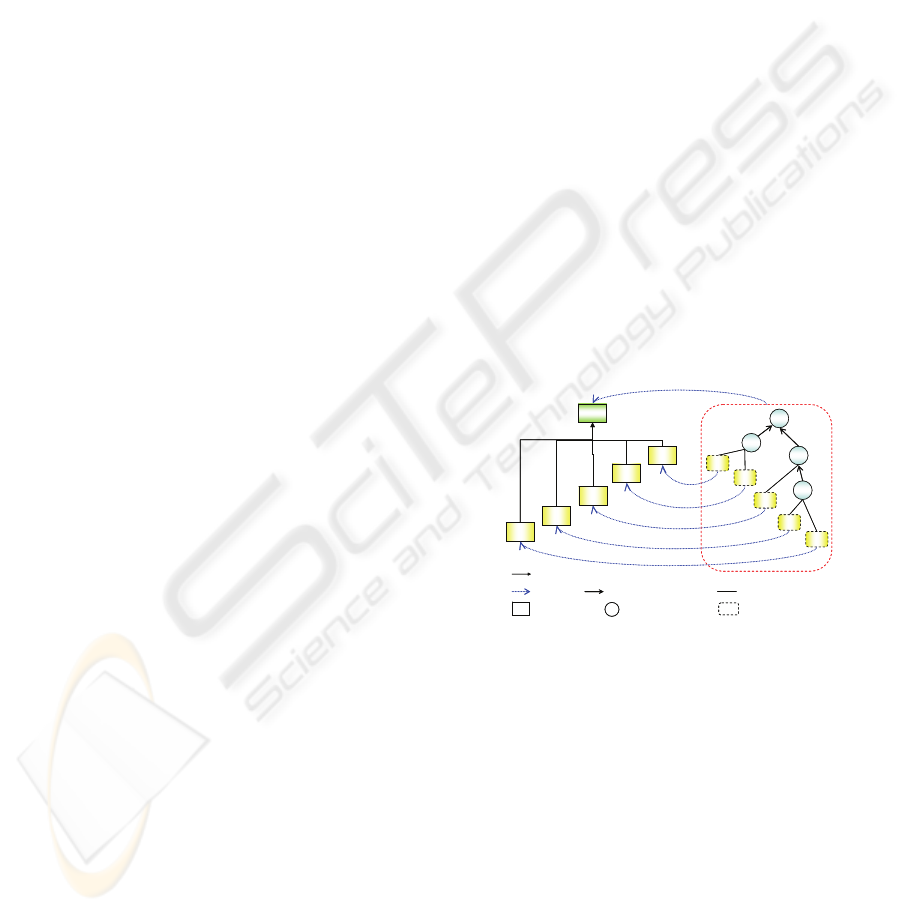
and hierarchical PNs (Fehling, 1993). In the
following two sections, an overview of PPbPC and
an industrial example which we use to demonstrate
the modelling of PPbPC based on the proposed
formalism are introduced, respectively.
2 OVERVIEW OF PPBPC
2.1 Process Platform
In relation to a product family, a process family
refers to a set of production processes which fulfil
all individual products belonging to the family
(Zhang, 2007). As with the common product
structure assumed by all products in a family, a
common process structure is inherent in the
corresponding process family. In essence, a process
platform entails a conceptual structure and overall
logical organization of a process family in relation to
a product family. It provides a generic umbrella to
capture and utilize commonality in planning
production processes for the product family. More
specifically, a process platform is underpinned by an
integrated product-process structure common to both
the product and process families. Thus, a process
platform includes all design data pertaining to the
product family, e.g., assemblies, parts, design
parameters, value instances, and these of the process
family, e.g., operations, manufacturing resources
(i.e., machines, tools, fixtures, jigs, etc), setups.
These product and process family data are organized
by following the material requirement links (i.e., the
links among material inputs, operations and product
outputs) in general, the mapping relationships
enabled by design parameters and their value
instances in particular (Zhang et al., 2007).
2.2 Production Configuration
Within a process platform, for a given member of
the associated product family, production
configuration takes the BOM (i.e., bill of materials)
and a list of product specifications of a given
product as inputs. The proper process elements, such
as abstract processes for individual product items
(including the end-product), operations, machines,
tools, fixtures, estimated cycle times, and setups are
then selected. Subsequently, these selected process
elements are arranged into feasible production
processes, where the abstract processes are replaced
with process details, for producing the given end-
product. Both selection and arrangement are subject
to constraints among product and process data.
Finally, evaluation of the configured multiple
feasible production processes takes place to
determine the most appropriate one.
In line with the fact that the hierarchical
structure of a product can be regarded as a collection
of independent product items organized at different
levels of abstraction, production configuration is an
iterative process of configuring process for each
product item specified in the BOM along the
hierarchical structure per se. At each configuration,
only the child items at the immediate lower level are
considered. It starts with the end-product at the top
level of the hierarchy. The results are: 1) abstract
processes for the immediate child items - be they
parts or assemblies, 2) assembly operations
involving these child items and WIPs (work in
processes), 3) manufacturing resources required to
complete the corresponding operations, estimated
cycle times and setups, and 4) precedence
relationships between operations. Fig. 1 shows
production configuration for an item: PI, which has
five immediate child items: A, B, C, D and E.
According to the input specifications, five abstract
processes for the five child items are selected first;
the assembly operations along with manufacturing
resources joining the child items are specified and
ordered into a sequence.
PI
A
B
C
D
E
O4
O3
O2
O1
: Product item; : Assembly operation;
: Abstract process
: Produce; : Operations precedence; : Material input
P
E
P
D
P
A
P
B
P
C
: Parent-child releationship
PI
A
B
C
D
E
O4
O3
O2
O1
: Product item; : Assembly operation;
: Abstract process
: Produce; : Operations precedence; : Material input
P
E
P
D
P
A
P
B
P
C
: Parent-child releationship
Figure 1: Configuring process elements in production
configuration.
After the configuration process for an end-
product, configuration continues to the child items at
the immediate lower level. Each child item, in turn,
is treated as an end-product, and its abstract process
specified previously is refined accordingly. The
complete production process for the product is
formed by replacing the abstract processes at higher
levels with the refined processes at lower levels.
Thus, complete production processes consider all
processes for child items listed in products’ BOMs
and cover all operations starting from these
involving raw materials.
ICEIS 2009 - International Conference on Enterprise Information Systems
6