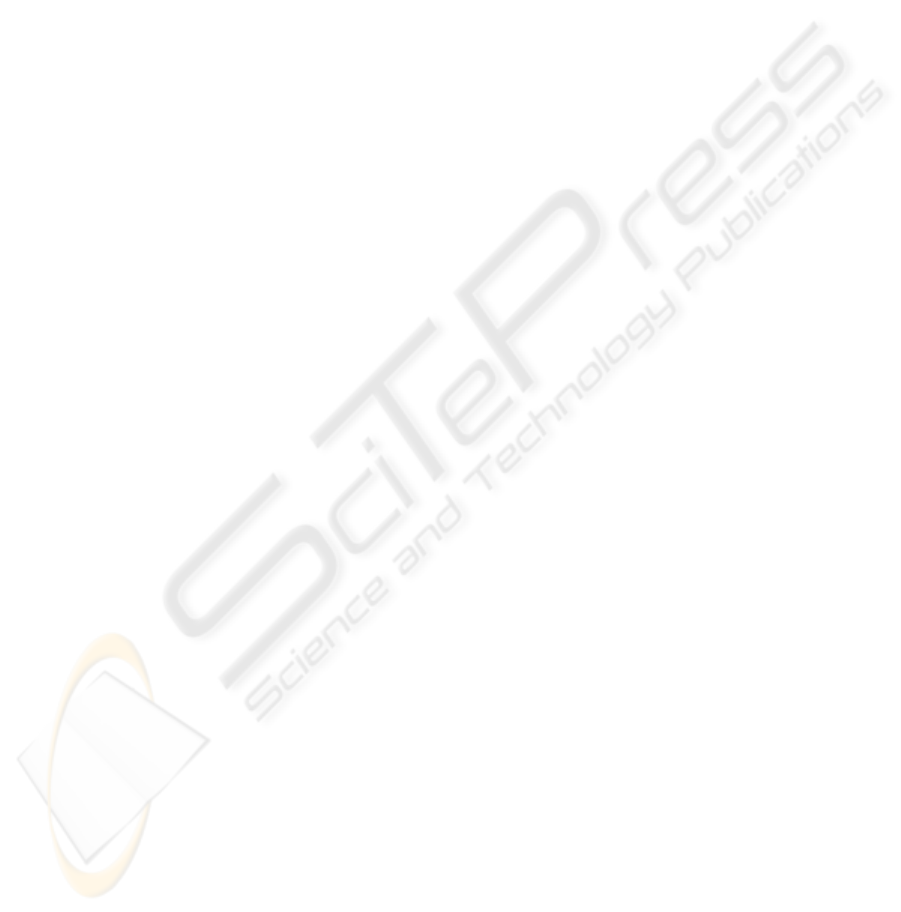
4. Modification and extension may be necessary
to tailor for reverse distribution.
For illustrative purposes, let us suppose that a
computer manufacturer (called Apple hereafter)
selling hardware to end-users intends to recycle used
computers from its customers. Customers who wish
to return the computer will dispose their computer at
the various initial collection points and Apple will
employ logistics providers to collect the disposed
computer from the initial collection points.
Given the limited space at the initial collection
points, returned products should be collected and
shipped to the centralized collection centre as soon
as possible and the components collected should be
determined as soon as the returned products reaches
the centralized collection center.
At the centralized collection center, components
that can be reused may be redistributed after minor
cleaning or refurbishing while defective components
will undergo recycling processes. With the above
situation as a model, we wish to address the
following issues:
1. Location of initial collection point such as to
cover the largest possible population in an area.
2. Location of centralized collection center such
that transportation from initial collection point
to the centralized collection center is minimum.
3. Method to obtain component information most
efficient and timely from the returned product
to determine for its quantity and quality.
4 MODEL DESIGN
4.1 Framework of Reverse Logistics
Reverse logistics is the management of material flow
opposite to the conventional supply chain flow
(Fleischmann et al., 1997). It encompasses logistic
activities to transform used products from end users
back to usable products again.
Reverse logistics management involves 3 main
stages:
1. Distribution planning aspects – This stage
involves physical transportation of used
products from end users back to the producers.
2. Transformation – The recovery of returned
product back to usable product. There are
several ways of transformation including:
Direct reuse, Repair, Recycling and
Remanufacturing.
3. Inventory Management – This is to manage
inventory level and to integrate supply flow
from both the traditional supply chain and also
from reverse logistics (Fleischmann et al.,
1997).
Dimensions of Reverse Logistics. There are
many instances of reuse criteria. These can be
classified as motivational, items recovered, forms of
reuse and the actors that are involved in the process.
Reuse motivation can be due to economical and also
ecological. In terms of economical, usually
machinery parts can be reused with slight repairs
and this saves cost as compared to manufacturing a
new part. As for ecological concerns, companies are
increasingly being pressured to take back all their
sales materials for recycling purposes in order to be
eco-friendly.
As for different types of materials recovered, the
forms of reuse may vary as well. The different forms
of reuse includes:
• Direct Reuse. Returned materials can be
reused directly without major repairs except for
cleaning. Examples of such products are bottles
and containers.
• Repair. This process is to restore failed
products into working order. However, the
performance of the repaired product might be
reduced.
• Recycling. This process recovers material
without conserving any of the initial product
structure. Commonly recycled items are scraps,
paper and glass.
• Remanufacturing. This process differs from
recycling in that the recovered product retains
its original characteristics. Examples are
automotive engines and machines.
Finally, there are also different actors involved in
reverse logistics. Actors play different parts in the
reverse logistics process such as collection, testing
and product recovery. Due to the different actors
involved in reverse logistics, integrating reverse and
forward logistics pose a major challenge.
As stated in the problem definition section, there
are many challenges in designing an optimum
reverse logistics management system and integrating
forward and reverse logistics. Most of the problems
arose mainly due to uncertainties in the reverse flow
of materials both in terms of quantity and quality
and also the timeliness of the information gathered.
Below, we propose a model that integrates RFID
technology into the reverse logistics framework to
eliminate the uncertainties involved in the process.
Furthermore, we will also employ genetic algorithm
optimization technique to determine the optimum
location for the initial collection point so as to
maximize user coverage and reduce logistics cost
involved in the process.
DESIGN A REVERSE LOGISTICS INFORMATION SYSTEM WITH RFID
295