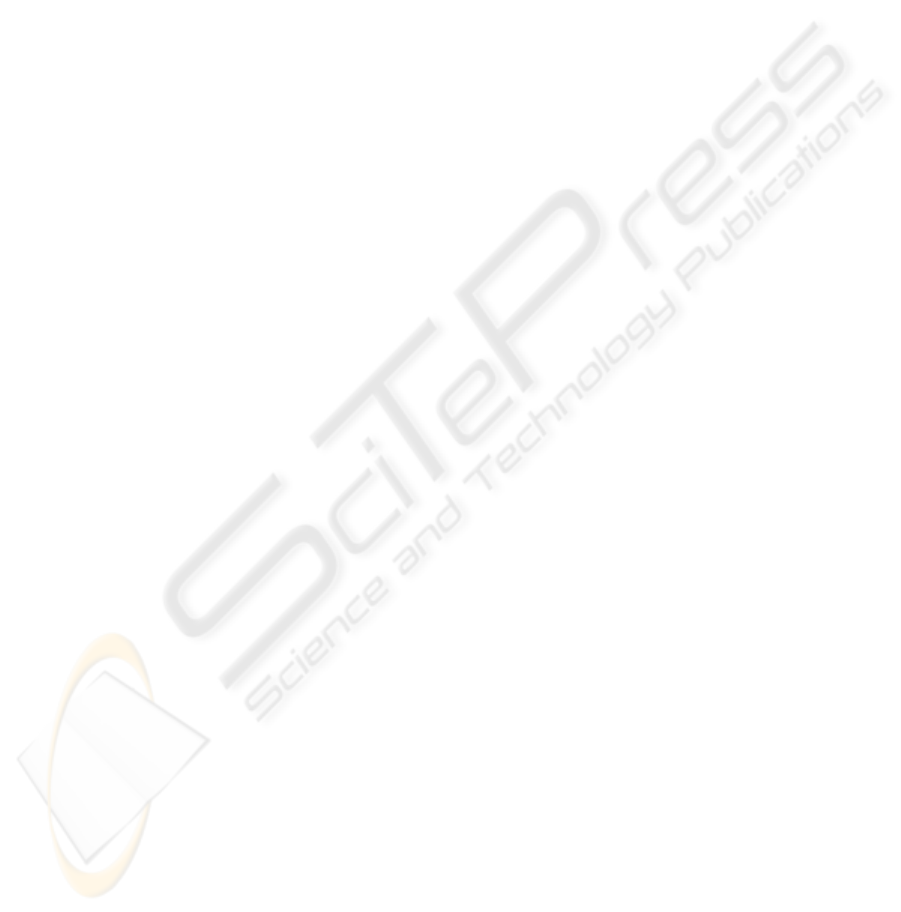
dependent on the network speed. In the shared 3D
manipulation method, however, the system
performance of operation sharing is somewhat
irrelevant of the network speed. The comparison of
“scenario i” and “scenario i +
α
” shows that the
performance of operation sharing mainly depends on
the hardware performance of clients.
In Table 1, T
d
is the average time delay for an
interaction delivery to the other party, and T
c
is the
converging time for maintaining consistency when
dependent operations are carried out simultaneously.
When the two clients are simultaneously involved in
viewing transformation, object manipulation, or
object selection, the test result shows that there is
correlation between the operation type and the
converging time. Since consistency is guaranteed
when independent operations are performed, the
converging time is the same as T
d
. However, for
dependent operations, the converging time (T
c
) is
larger than T
d
since the client of a higher priority
sends a synchronization signal.
5 CONCLUSIONS
We have presented an efficient method for sharing
the manipulation of 3D objects and their viewing
environment over the network. Based on the
proposed method, we have also developed a
collaborative mobile maintenance system that can
support effective communication between a
maintenance expert and a less-experienced operator
at an interactive speed over the Internet.
Compared with other conventional techniques
for modeling and processing 3D objects, the
problem of data sharing over the network entails
different ways of representing and manipulating the
3D models. In the current work, we have considered
only a small number of state variables to be shared
over the network. According to our experiment
results, the network capacity of today can deal with
sharing a reasonably large number of state variables
at an interactive speed. Thus we can apply the
proposed approach to considerably more complex
3D models over the network. Nevertheless, the data
structure for representing and manipulating these
network-sharable 3D models would considerably be
different from conventional ones.
We believe that techniques for procedural
modeling of complex 3D objects will play an
important role in this new direction of research in
geometric modeling and processing. In future work,
we will investigate a systematic way of utilizing
previous techniques for procedural modeling in
various important applications of 3D data sharing
over the network.
REFERENCES
CDMA USB Modem CCU-550. Online at
http://www.cmotech.com/eproduct6-1.htm, accessed
on 10. Nov. 2008.
Chen, L., Song, Z., and Feng, L., 2004. “Internet-enabled
Real-time Collaborative Assembly Modeling via an e-
Assembly System : Status and Promise,” Computer-
Aided Design, 36, pp 835-847.
Choi, C.-T., Lee, K.-H., Shin, K.-T., Hong, K.-S., and Ahn,
H.-S., 1999. “Automatic Landing Method of a
Reclaimer on the Stockpile”, IEEE Transactions on
System, Man, and Cybernetics-Part C : Applications
and Reviews, Vol. 29, No. 1, Feb., pp.308-314.
Hamza-Lup, F.G., and Rolland, J.P., 2004. “Scene
Synchronization for Real Time Interaction in
Distributed Mixed Reality and Virtual Reality
environments,” Presence: Teleoperators & Virtual
Environments, Special Issue: Collaborative Virtual
Environments, Volume 13, Issue 3, MIT Press,
Cambridge, MA, USA, June.
Linebarger, J.M., and Kessler, G.D., 2004. "Concurrency
Control Mechanisms for Closely Coupled
Collaboration in Multithreaded Peer-to-Peer Virtual
Environments," Presence: Teleoperators and Virtual
Environments, Vol. 13, Issue 3, pp. 296-314, Jun.
Nishino, H., Utsumiya, K., Sakamoto A., Yoshida, K., and
Korida, K., 1999. “A method for sharing interactive
deformations in collaborative 3D modeling,”
Proceedings of ACM VRST, pp. 116-123, Dec.
Palazzi, C.E., Ferretti, S., Cacciaguerra, S., and Roccetti
M., 2004. “On Maintaining Interactivity in Event
Delivery Synchronization for Mirrored Game
Architectures”, Proc. of NIME’04, pp. 157-165, Dallas,
TX, USA.
Pang, A., and Wittenbrink, C., 1997. “Collaborative 3D
Visualization with CSpray,” IEEE Computer Graphics
Applications, 17(2), pp.32–41.
Wang, J.F., Tse, P.W., He, L.S., and Yeung, R.W., 2004.
“Remote sensing, diagnosis and collaborative
maintenance with Web-enabled virtual instruments
and mini-servers,” International Journal of Adv.
Manufacturing Technology, pp. 764-772.
SHARED MANIPULATION OF 3D OBJECTS FOR COLLABORATIVE MOBILE MAINTENANCE
289