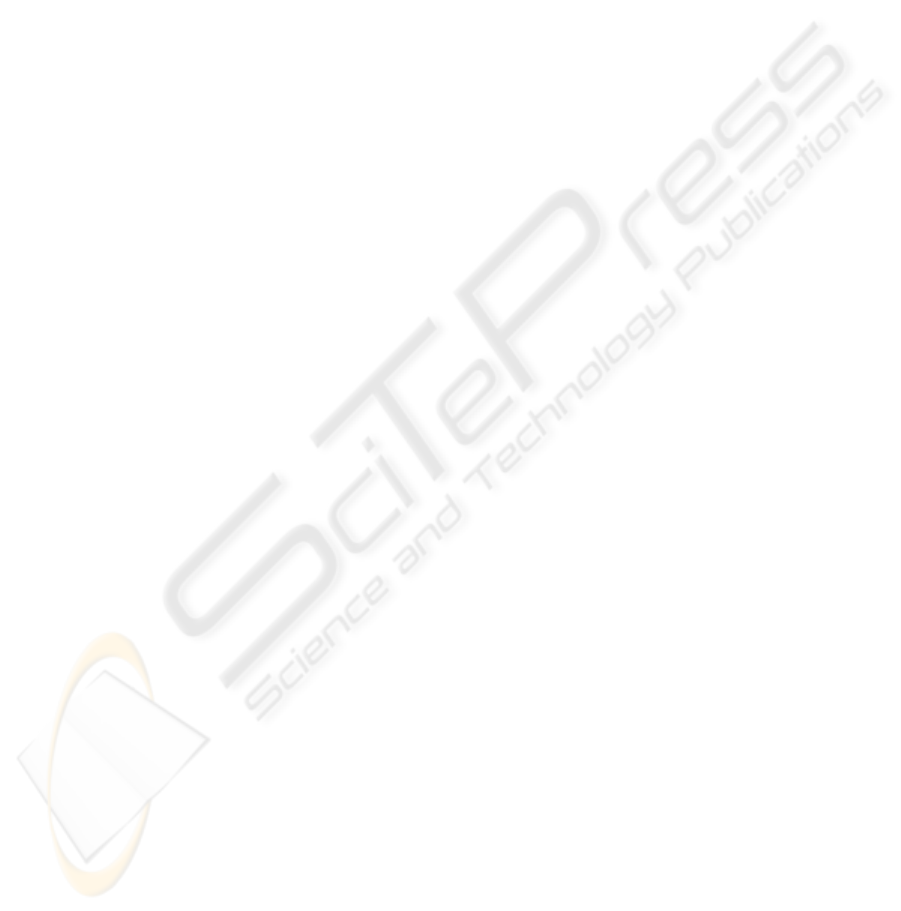
its RFID operations. IBM is responsible for the de-
sign, trial, rollout, and operation of the RFID system.
In order to minimize the financial risk involved in
realizing the RFID application, GW decided to ad-
vance in four steps. After each of these steps the con-
tinuation of the project will be re-evaluated. In the
first step, the RFID solution is designed, tested and
implemented in four distribution centres and two re-
tail stores. In the second step, the solution is rolled out
in all of GW’s retail stores. The international rollout
of the solution is initiated in the third step by equip-
ping two consolidation sites in China and Turkey with
RFID technology. In the final step, all remaining con-
solidation sites in the Far East will be included which
will enable the maximum item-level visibility that can
be achieved using RFID.
4 CONCLUSIONS
This paper described the current state of Gerry We-
ber’s RFID project. GW is one of the first companies
in the apparel industry that has decided to introduce
RFID on the item level. Based on the description of
the flow of goods and information, our case study dis-
closed the benefits GW expects from the introduction
of RFID. The case description gives insights into the
processes taking place along GW’s supply chain and
the data being exchanged between the supply chain
partners. GW has outsourced most of their logistics
operations but at the same time has to face the increas-
ing complexity of their supply chain. Therefore they
are interested in monitoring the flow of goods more
closely in order to diagnose possible exceptions re-
motely. Besides typical RFID benefits such as labour
cost and error reduction, RFID is expected to play a
key role in providing accurate monitoring data, which
will be used by sophisticated decision support sys-
tems.
The case shows how the ROI of RFID hardware
can be improved by closing the tag loop and ef-
ficiently combining RFID with extant technologies
such as EAS. Two RFID use cases that play a cru-
cial role in the implementation of GW’s RFID strat-
egy were analyzed: the virtual association and the
goods issue process. The corresponding advantages
and challenges were outlined. The approach of using
RFID in a closed loop and integrating it with extant
EAS processes is not necessarily restricted to the ap-
parel industry. It could also be applied to other retail
products of relatively high sales value (e.g. consumer
electronics). In our opinion, the approach of increas-
ing the ROI of item-level tagging outlined in this pa-
per has the potential to foster the diffusion of large-
scale item-level RFID applications. If more RFID
transponders are sold their price will eventually drop
due to the economies of scale realized in their pro-
duction. This in turn will eventually also make open
loop applications economically viable. Although GW
will start to use RFID transponders in a closed loop,
the system architecture that is currently being imple-
mented can easily be expanded to an open-loop appli-
cation: when GW’s wholesale customers start calling
for RFID tagging, GW will be ready to serve their re-
quest.
REFERENCES
Chappell, G., Durdan, D., Gilbert, G., Ginsburg, L., Smith,
J., and Tobolski, J. (2003). Auto-ID in the Box: The
Value of Auto-ID Technology in Retail Stores. Tech-
nical Report, Auto-ID Lab MIT.
Chawathe, S. S., Krishnamurthy, V., Ramachandran, S., and
Sarma, S. (2004). Managing RFID Data. In Proceed-
ings of the Thirtieth International Conference on Very
Large Data Bases, pages 1189–1195.
Gaukler, G. M. and Seifert, R. W. (2007). Trends in Sup-
ply Chain Design and Management: Technologies and
Methodologies, chapter Applications of RFID in Sup-
ply Chains. Springer London Ltd.
G
¨
unther, O. and Spiekermann, S. (2005). RFID and the
Perception of Control: The Consumer’s View. Com-
munications of the ACM, 48(9):73–76.
IDTechEx (2007). RFID Forecasts, Players and Opportu-
nities 2007-2017. http://www.idtechex.com/forecasts.
Last visited: 11/15/2008.
Juels, A. (2006). RFID Security and Privacy: a Research
Survey. IEEE Journal on Selected Areas in Commu-
nications, 24(2):381–394.
Lee, H. and
¨
Ozer, O. (2007). Unlocking the Value of RFID.
Production and Operations Management, 16(1):40–
64.
Loebbecke, C. and Huyskens, C. (2007). Towards Standard-
izing Success: RFID in Fashion Retailing. In Proceed-
ings of the 20th Bled Conference.
Ngai, E. W. T., Moon, K. K., Riggins, F. J., and Yi,
C. Y. (2008). RFID Research: An Academic Litera-
ture Review (1995-2005) and Future Research Direc-
tions. International Journal of Production Economics,
112(2):510–520.
Schmitt, P. and Michahelles, F. (2008). Economic Impact
of RFID. Report, BRIDGE Project.
Strassner, M. (2005). RFID im Supply Chain Management.
Deutscher Universit
¨
ats-Verlag, Wiesbaden, Germany.
Voss, C., Tsikriktsis, N., and Frohlich, M. (2002). Case Re-
search in Operations Management. Int. Jounal of Op-
erations & Production Management, 22(2):195–219.
Wu, N. C., Nystrom, M. A., Lin, T. R., and Yu, H. C. (2006).
Challenges to Global RFID Adoption. Technovation,
26(12):1317–1323.
ICEIS 2009 - International Conference on Enterprise Information Systems
102