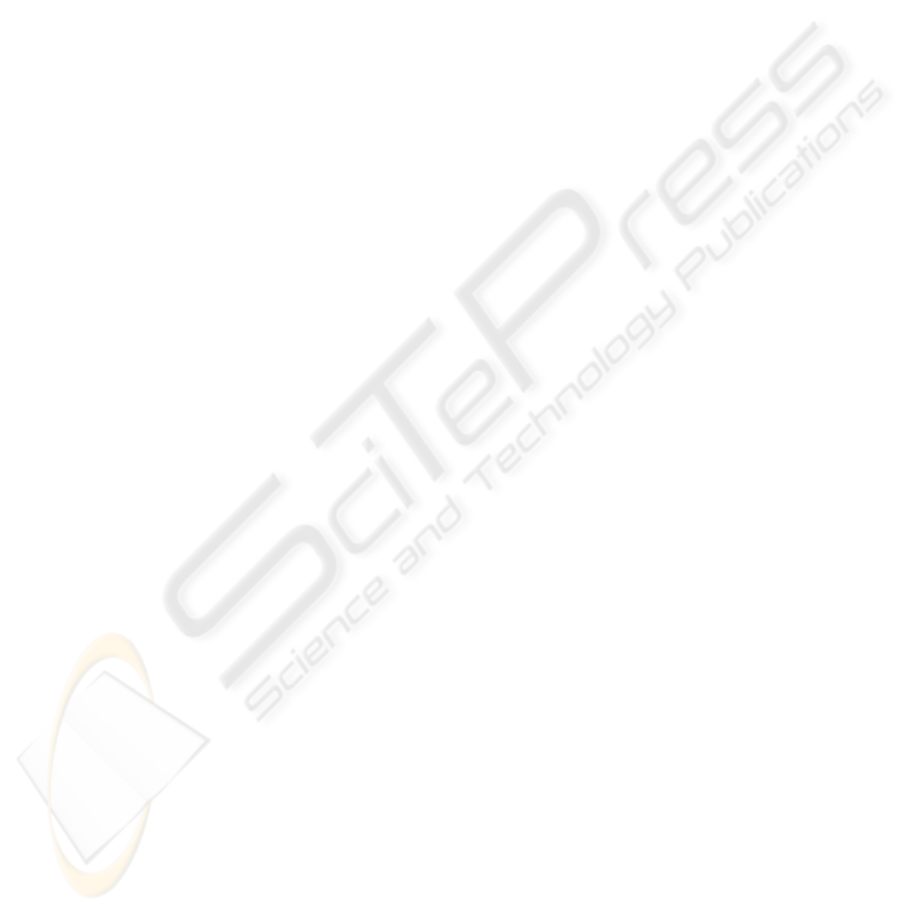
assembled in the plant f
j
. The PCT of the product A
is shown in Table 2.
4 SOLUTION USING PARTICLE
SWARM OPTIMIZATION (PSO)
A PSO algorithm is presented for simultaneously
performing assembly sequence planning and plant
assignment. The PSO algorithm is an evolutionary
computation method introduced by Kennedy and
Eberhard (1995, 1997). In PSO, each particle
moves around in the multi-dimensional space with a
position and a velocity. The velocity and position
are constantly updated by the particle’s own
experience and the experience of the whole swarm.
Given a problem, a particle can be encoded to
represent a solution. Each solution, called a particle,
flies in the search space towards the optimal
position.
A particle is defined by its position and velocity.
The position of a particle i in the D-dimension
search space can be represented as X
i
=[x
i1
, x
i2
, …,
x
id
, …, x
iD
]. The velocity of the particle i in the D-
dimension search space can be represented as
V
i
=[v
i1
, v
i2
, …, v
id
, …, v
iD
]. Each particle has its
own best position P
i
=[p
i1
, p
i2
, …, p
id
, …, p
iD
]
representing the particle’s personal best objective
(pbest) at time t. The global best particle is denoted
as p
g
and the best position of the entire swarm
(gbest) is denoted as P
g
=[p
g1
, p
g2
, …, p
gd
, …, p
gD
] at
time t. To search for the optimal solution, each
particle adjusts its velocity according to the velocity
updating equation and position updating equation.
()
()
idgdidid
old
idi
new
id
xprcxprcvwv −⋅⋅+−⋅⋅+⋅=
2211
,
(3)
where d =1, …, D, i =1, …, E (number of particles),
new
id
v
: the new velocity of i in the current iteration t,
old
id
v
: the velocity of i in the previous iteration (t - 1),
c
1
and c
2
: constants called acceleration coefficients,
w
i
: the inertia weight,
r
1
and r
2
: two independent random numbers with a
uniform distribution [0, 1],
p
id
: the best position of each individual particle i,
p
gd
: the best position of the entire swarm.
new
id
old
id
new
id
vxx +=
,
(4)
where
new
id
x
is the new position in the current
iteration t,
old
id
x is in the previous iteration (t - 1).
4.1 Encoding Scheme
In the developed encoding scheme, a particle
represents a feasible multi-plant assembly sequence.
A heuristic sequencing and assignment rule for
encoding and decoding is introduced as follows.
The position of particle i is represented by a
position matrix, denoted as X
ijk
, j = 1, …, (M+1), k =
1, …, N, where N is the number of components and
M is the number of plants. In the heuristic
sequencing rule, the values in the first row S of R
s1
,
R
s2
, …, R
sN
represent the ranked order values of the
N components in an assembly sequence.
In each column, the values from row F
1
to row
F
M
represent the ranked assignment values for plant
assignment of a component. In the heuristic
assignment rule, the component C
k
is assigned to the
plant with the smallest value in the column of R
1k
,
R
2k
, …, R
Mk
.
X
ijk
=,
⎥
⎥
⎥
⎥
⎥
⎥
⎥
⎦
⎤
⎢
⎢
⎢
⎢
⎢
⎢
⎢
⎣
⎡
MNMkMM
jk
Nk
Nk
sNskss
M
j
Nk
RRRR
R
RRRR
RRRR
RRRR
F
F
F
F
S
CCCC
""
##
""
""
""
#
#
""
21
222221
111211
21
2
1
21
(5
where i = 1, …, E, where F
j
is a plant, j =1, …, M,
and C
k
is a component, k =1, …, N,
R
sk
represents the ranked order value of a
component k,
R
jk
represents the ranked assignment value for
component k assigned to plant j.
In the heuristic rule for assembly sequencing,
the values in [R
s1
, R
s2
, …, R
sk
, …, R
sN
] are sorted in
an ascending order. The ranked order values
represent the ordered position of component C
k
in
the assembly sequence. For example, if the values
of row S are [4.5 1.1 3.2 7.6 5.3], then the ordered
positions of (C
1
, C
2
, C
3
, C
4
, C
5
) are (third, first,
second, fifth, fourth). The assembly sequence is
determined as (C
2
, C
3
, C
1
, C
5
, C
4
).
In the heuristic rule for plant assignment, in
each column of C
k
, the component C
k
is assigned to
the plant with the smallest ranked assignment value
in R
jk
, for j = 1, …, M. For example, if there are
four plants, the values of column C
2
are [3.1 5.8
1.5 6.9]
T
, then the smallest value is 1.5 of plant F
3
.
Therefore, the component C
2
is assigned to plant F
3
.
4.2 Fitness Function
The cost functions include two major items. The
assembly operational costs are mainly related to
ICEIS 2009 - International Conference on Enterprise Information Systems
126