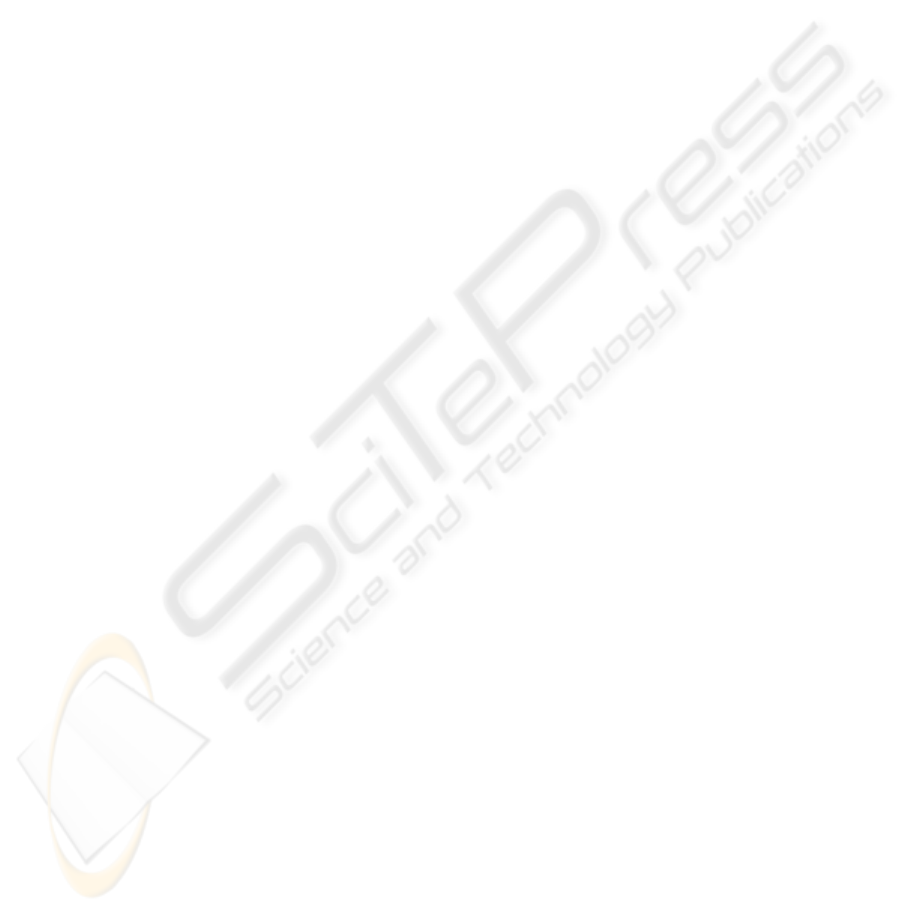
operator. Chapter 2 describes the necessity and
importance of the collaborations in the present
competitive environment and introduces the
engineering collaboration for pre-examination and
post-verification in the moldmaking process.
Chapter 3 details the web-based visualization and
conference function, which plays major roles in the
web-based engineering collaboration.
2 COLLABORATIVE
ENGINEERING
In order to survive in the present industrial
environment, large enterprises producing finished
products should focus on the more crucial stages in
the development of a product, like prerequisite
technology research, product planning, assembly
design, and marketing, etc. Most of the general
manufacturing stages, like mold fabrications and
part manufacturing, are conducted by the
collaborating enterprises. But, from the viewpoint of
large enterprises, most collaborating enterprises are
small-scale, with only low levels of manufacturing
technology.
In the case of mold fabrication, especially in
Korea, the mold makers are smaller-scale and are
struggling to meet the requirements of their
customers, which are generally large enterprises.
Large enterprises want collaborating enterprises to
invest in man-power and equipment, but small-scale
enterprises cannot afford to possess such expensive
equipments. Even worse, the most difficult problem
is to locate and maintain experts who can operate the
equipments. These kinds of equipments can be
different according to the characteristic of the
industry and the level of required technology, and in
the case of mold fabrication, these equipments are
CAE (Computer Aided Engineering) tools for
injection molding flow analysis and the 3-
dimensional inspection systems for measuring the
manufactured products. In order to cope with this
problem, we suggest the engineering collaboration
model in which 3 parties playing important functions
in developing molds, that is to say, mold makers,
mold purchasers, and expert engineers, work
together in the web environment. Three parties can
share important information such as drafts and
documents, and can also have conferences with
faraway co-workers while seeing the same screen
via the Internet. When the mold maker or the mold
purchaser requests technical assistance, the expert
engineers assist them according to their request. The
pre-investigation shows us that the injection molding
flow analysis and the 3-dimensional inspection are
the most important, but these are difficult
engineering techniques for small-scale enterprises
making molds, therefore we made them our focus
when designing and implementing the engineering
collaboration system.
2.1 Process of Mold Development
The process of mold development begins with mold
design and ends with molding trial through
machining and assembly processes. In the stage of
mold design, the recent immense development of
rheology and computation enables us to estimate the
flow of resin in the mold and the deformation of
solidified resin before making the real mold. As such,
the majority of mold purchasers order important and
high value-added molds from the mold makers who
can provide them with these CAE results – injection
molding flow analysis. After designing the molds,
mold makers complete the molds by machining the
parts and assembling them. Molding trial is the last
stage just before delivery. If the results of the
molding trial do not meet the required specifications,
the mold is moved to the factory where it is
disassembled and repaired in the proper process
according to the cause of defects. These molding
trial and repairing processes are repeated until the
mold passes all the required specifications. In the
molding trial stage, 3D inspection is not only one of
the most important criteria, but also the evidence
that helps engineers to analogize the causes of
defects and find counter-plans. The following 2
subsections present more detailed process and
function of the developed collaboration system
(Engineering Collaboration Hub).
2.2 Injection Molding Flow Analysis
Figure 1 demonstrates the process for collaborating
with faraway co-workers in the stage of injection
molding flow analysis (CAE Analysis). The related
parties need not gather in the same location and time.
Large enterprises or those performing product
design transfer design information to the
collaborating moldmaker. If the enterprise requests
the engineering collaboration hub to provide a CAE
analysis based on this information, this request is
transferred to the PM (Project Manager) at KITECH
(Korea Institute of Industrial Technology) by e-mail
and SMS (Short Message Service for mobile phone).
ICEIS 2009 - International Conference on Enterprise Information Systems
160