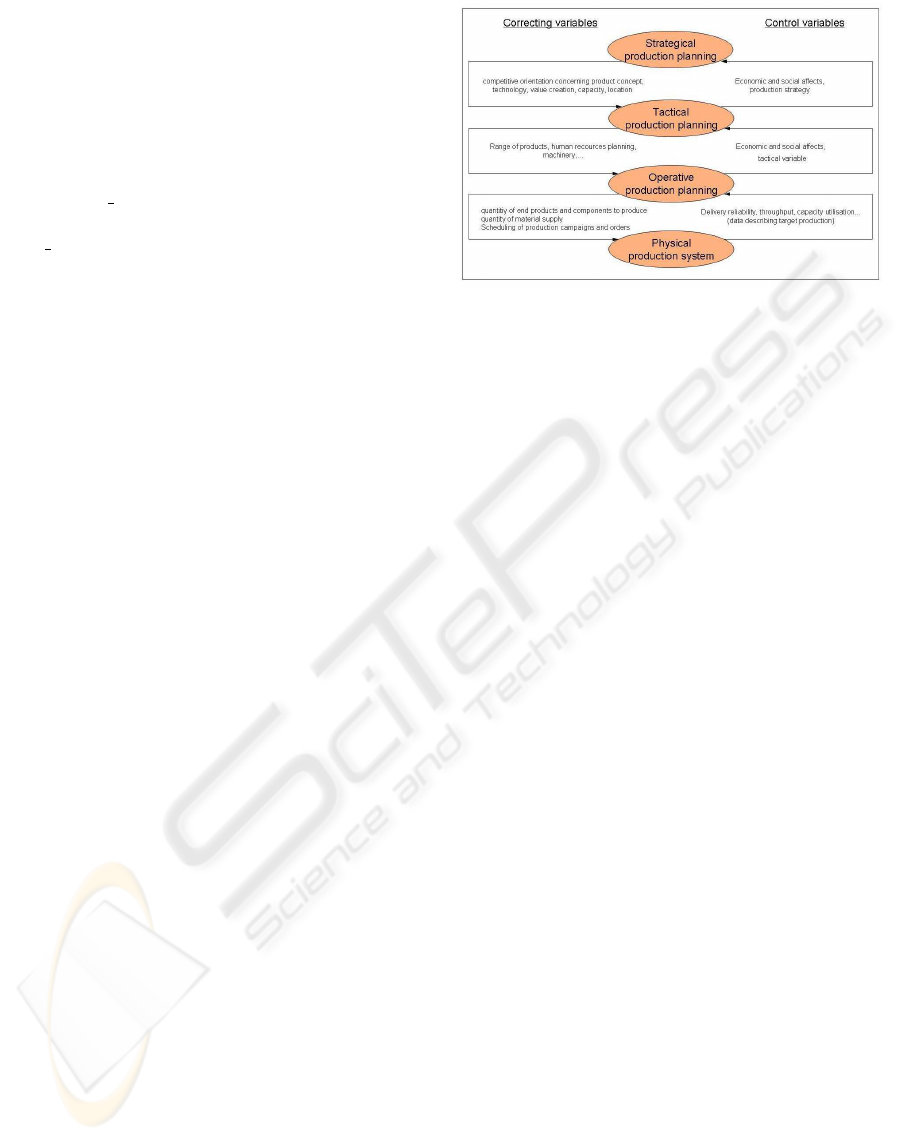
processes, mostly data driven and often not modeling
the business processes they should. ERP systems like
APO (Bartsch and Bickenbach, 2002) or APS (Ad-
vanced Planning and Scheduling) are suitable for a
rough planning, only. Big software companies have
adopted the strategy to provide integration mecha-
nisms for MES-level solutions (SAP, 2004) like the
presented solution.
MasDISPO xt, a decentralised agent based ap-
proach, is the proposed solution of this paper. In Mas-
DISPO xt, every order is modeled as an agent. The
agent calculates and observes its own schedule from
order entry, across rough and detailed planning, and
monitors the production up to the point of delivery.
It responds to changes during planning, scheduling
and production by dynamically adapting the sched-
ules. Also, each aggregate of any factory is also mod-
eled as an agent which also calculates its schedule au-
tonomously based on further local knowledge and re-
strictions.
The complete production chain is very complex
and could not be addressed with the appropriate de-
tail in the context of only one paper. Therefore, this
paper concentrates on the horizontal and vertical in-
tegration of solutions provided for detailed planning
into a global perspective regarding rough planning
and the other way round. As a presetting, rough plan-
ning influences detailed planning and vice versa a re-
arranged detailed planning might impact the rough
layer – probably on several manufacturing levels. Ex-
isting ERP solutions cannot provide such integrations
very suitable – the motivation for the presented ap-
proach.
2 PLANNING AT SAARSTAHL AG
Steel production in general is a very complex, dy-
namic and disassembling process. It starts inside the
blast furnace as hot metal and ends up in vast number
of products of different kinds. On each manufacturing
step, there are lots of restrictions regarding quality,
size, dimension and others which determine the cam-
paigns and batch units on each processing step. Of
course, time restrictions also have to be kept. Hence,
a delay on a certain step might have cascading effects
along different branches of further processing. As
mentioned, the average order backlog of Saarstahl is
about 17500 – each order composed of several order
position and each position with up to 50 processing
steps. Hence, it is a challenge to keep planning and
scheduling under control.
Competitive orientation concerning product con-
cepts, technology and others are discussed per annum
Figure 1: Control Cycle of planning influences and depen-
dencies.
and give a direction for human resource planning or
machinery on a tactical level. In planning levels re-
garding sales, the global production capacities for the
different production phases are booked. After that,
the planning process continues by planning at lower
levels. For each factory, the global planning level pro-
vides the lower level with a set of orders for a speci-
fied time horizon. These assigned orders are planned
in more detail while going down in planning levels
down to physical production systems. All these in-
fluences are correcting variables from ’above’ often
given just once.
On the other hand, physical production systems
might have any delays which has to adopted by
the planning system above. Delivery reliability or
throughput are measured constantly and influence the
next level above. These control variables go up to the
strategical planning on highest level. A cycle of inter-
dependencies as shown in figure 1 is created. Flexibil-
ity across these different layers is needed to guarantee
a flexible planning and production process.
The planning horizon on highest level is quite
rough, the closer it gets down to production the
shorter the horizon is. To realise this exchange of in-
formations, smooth interfaces between the acting sys-
tems are needed. On a higher level planning level,
usually normal ERP-systems are used. These systems
probably also support also provide a adavnced plan-
ning system (APS) for a rough planning. Beneath, a
so called MES is used for a detailed planning. The
last level is the automation level covered by ’SPS’
or ’SCADA’ (Supervisory Control and Data Acqui-
sition). A smooth vertical integration of these acting
systems is needed to guarantee a fast exchange of in-
formations which is especially needed in steel pro-
duction since materials are often molten between two
different processing steps and might not cool down.
Saarstahl is a historically grown company. Hence,
a lot of obsolete legacy systems are running. In-
ICEIS 2009 - International Conference on Enterprise Information Systems
348