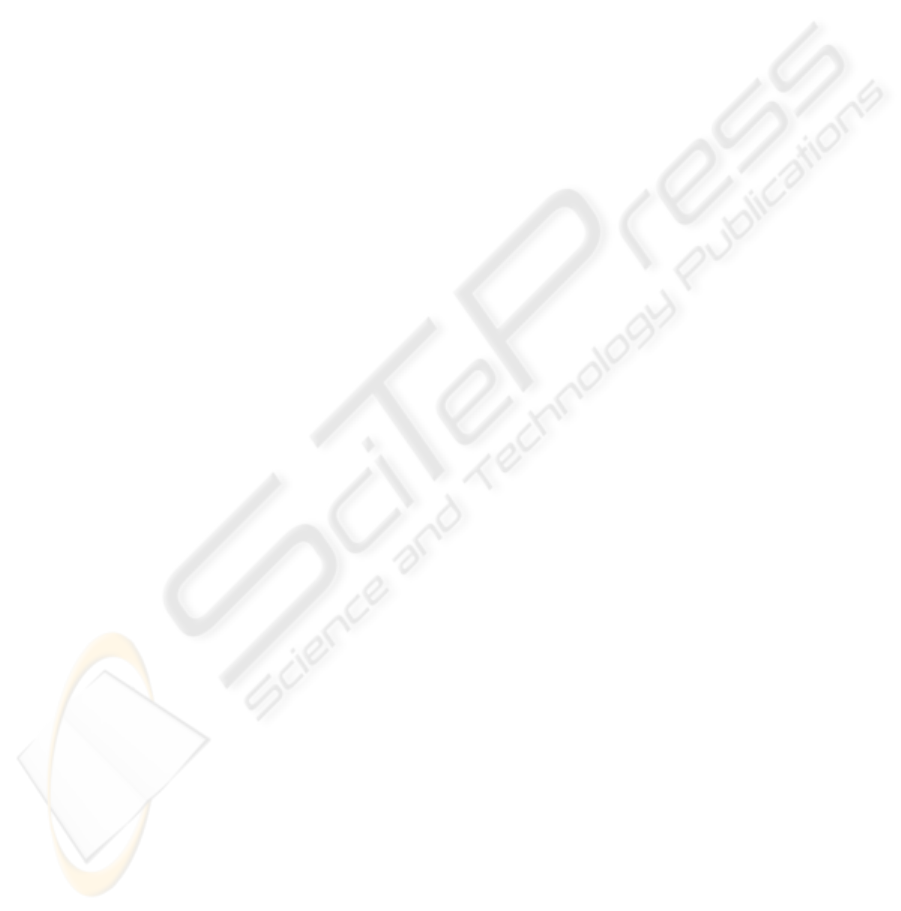
and computationally inexpensive. Moreover, by lin-
ear constraints, the evolution converged extremely
fast and the training time was largely reduced. It
is an essential advantage for physical robot learning,
minimizing possible damage to the robot. It reduced
the human work as well as generating evolutional re-
sults varied a lot in different experiences. Through
experiments which took about 60 minutes each, we
achieved several high performance sets of gait param-
eters which differ a lot from each other. The proposed
method generated a speed of 478mm/s which is faster
than the previous known gaits.
One of the useful aspects of the proposed method
is that the high-dimensional parameter set is opti-
mized in an effective way. In order to reduce the
dimension, we approach a linear constraint for the
parameters. Under this constraint, the locus can be
optimized fast. Another contribution of our method
is the combination of the two algorithms, GA and
APSO. The result shows that the strategy has better
global searching capability and local searching capa-
bility than using each algorithm only.
In the future, we will compare different high-
performance gait parameters and analyze the dynam-
ics model of the robot to obtain further understand-
ing of the relation between parameter and its perfor-
mance. In this study, we find that the gait actually
executed by the robot differs significantly from the
one that we design. There are several possible rea-
sons. The most important one is the interaction with
environment prevents the implement of some strokes
of robot legs. Although with learning approach, fac-
tors that cause the difference between actual gait and
planned gait do not have to be taken into considera-
tion. However, we assume that if the planned gait and
actual gait can conform to each other, AIBO will walk
more stable with high speed. In order to solve the
problem, the analysis of dynamics between the robot
and the environment is necessary. In the gait learn-
ing procedure of current study, we only evolve fast
forward gait and choose forward speed as the fitness.
Later on, we will try to learn effective gaits in other
directions, for example, gaits for walking backward,
sideward and turning. We also consider exploring op-
timal omni-directional gaits. With gaits working well
at all directions, robots will be able to perform more
flexibly and reliably.
ACKNOWLEDGEMENTS
The authors gratefully acknowledge the con-
tribution of the team members of the sharP-
KUngfu Robot Team. Part of the source code
and videos can be found on the web page
http://www.mech.pku.edu.cn/robot/fourleg/
REFERENCES
R. M. Alexander, A. S. Jayes, A dynamic similarity hypoth-
esis for the gaits of quadrupedal mammals, J. Zoology,
vol. 201, pp. 135-152, 1983.
R. M. Alexander, A. S. Jayes, R. F. Ker, Estimates of energy
cost for quadrupedal running gaits, J. Zoology, vol.
190, pp. 155-192, 1980.
S. Collins, A. Ruina, R. Tedrake, M. Wisse, Efficient
bipedal robots based on passive dynamic walkers, Sci-
ence, vol. 307, 2005, pp. 1082-1085.
P. Holmes, R. J. Full, D. Koditschek, J. Guckenheimer, The
dynamics of legged locomotion: Models, analyses,
and challenges, SIAM Review, vol. 48, no. 2, 2006,
pp. 207-304.
G. S. Hornby, M. Fujita, S. Takamura, T. Yamamoto, O.
Hanagata, Autonomous evolution of gaits with the
Sony quadruped robot, Proceedings of the Genetic
and Evolutionary Computation Conference, vol. 2,
1999, pp. 1297-1304.
M. J. Quinlan, S. K. Chalup, R. H. Middleton. Techniques
for improving vision and locomotion on the Sony
AIBO robot. Proceedings of the 2003 Australasian
Conference on Robotics and Automation, 2003.
M. J. Quinlan, Nubots team robocup 2005. Technical report,
2005.
M. H. Raibert, Legged robots that balance, MIT Press,
Cambridge, 1986.
C. Reynolds, Flocks, herds, and schools: A distributed be-
havioral model, Comp. Graph., vol. 21, no. 4, pp. 25-
34, 1987.
C. Rong, Q. Wang, Y. Huang, G. Xie, L. Wang, ”Au-
tonomous evolution of high speed quadruped gaits us-
ing particle swarm optimization”, Lecture Notes in Ar-
tificial Intelligence, 5399, Springer-Verlag Berlin Hei-
delberg, 2009.
T. R
¨
ofer, H. D. Burkhard, U. D
¨
uffert, J. Hoffmann, D.
G
¨
ohring, M. J
¨
ungel, M. L
¨
otzsch, O. v. Stryk, R.
Brunn, M. Kallnik, M. Kunz, S. Petters, M. Risler, M.
Stelzer, I. Dahm, M. Wachter, K. Engel, A.Osterhues,
C. Schumann, J. Ziegler, GermanTeam RoboCup
2004. Technical report, 2004.
T. R
¨
ofer, H. D. Burkhard, U. D
¨
uffert, J. Hoffmann, D.
G
¨
ohring, M. J
¨
ungel, M. L
¨
otzsch, O. v. Stryk, R.
Brunn, M. Kallnik, M. Kunz, S. Petters, M. Risler,
M. Stelzer, I. Dahm, M. Wachter, K. Engel, A.
Osterhues, C. Schumann, J. Ziegler, GermanTeam
RoboCup 2005. Technical report, 2005.
ICINCO 2009 - 6th International Conference on Informatics in Control, Automation and Robotics
172