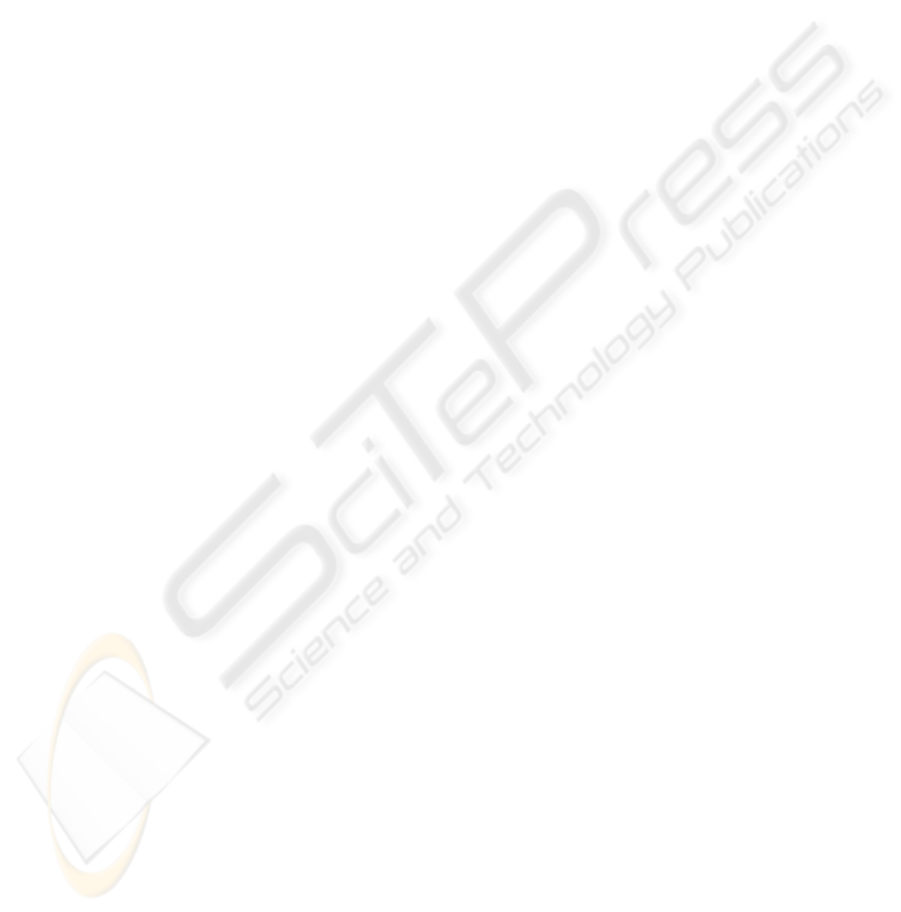
DIFFERENTIAL-DRIVE STEERING SYSTEM USING PLANETARY
GEARING FOR OMNIDIRECTIONAL MOBILE ROBOT
Hideo Kitagawa
Department of Electronic Control Engineering, Gifu National College of Technology
Kamimakuwa, Motosu, Gifu, Japan
Takashi Ohno, Yuki Ueno, Kazuhiko Terashima
Department of Production Systems Engineering, Toyohashi University of Technology
Hibarigaoka, Tempaku, Toyohashi, Japan
Keywords:
Mobile robots, Movement, Robot kinematics, Vehicles, Wheels, Ride comfort.
Abstract:
Holonomic omnidirectional mobile robot is useful with its high mobility in narrow or crowded area, and
omnidirectional robot equipped with normal tires is desired for difference excess, vibration suppression and
ride comfort. Caster-drive mechanism using normal tire has been developed to realize a holonomic omni-
diredctional robot, however, there remains some problems. This paper presents effective systems to control
the caster-drive wheels of omnidirectional mobile robot. Differential-Drive Steering System (DDSS) using
planetary gearing is proposed to improve the operation ratio of motors. DDSS generates driving and steering
torque effectively from two motors. Simulation results show the proposed system is effective for holonomic
omnidirectional mobile robots.
1 INTRODUCTION
An omnidirectional robot is highly maneuverable in
narrow or crowded area including residences, offices,
warehouses and hospitals. It can be applied to an
autonomous mobile robot in a factory, a wheelchair
and so on. Several kinds of omnidirectional mobile
robots and their applications have been developed by
(West, 1992), (Pin, 1994), (Damoto, 2002) and (Kita-
gawa, 2008). However, these robots realized their
omnidirectional motion by using special wheels such
as mechanum wheels, ball wheels, omni-disks and
omni-wheels.
To improve the ride comfort, vibration suppres-
sion, slippage reduction and ability of difference ex-
cess, omnidirectional robots equipped with normal
tires have been strongly required. (Arai, 1981) pro-
posed an omnidirectional vehicle equipped with nor-
mal tires. However, it was a non-holonomic vehicle
which has to adjust the direction of wheels before
changing the moving direction of vehicle.
Holonomic omnidirectional vehicles, which can
move in any direction without changing the direc-
tion of tires beforehand, equipped with normal tires
include dual-wheel type by (Wada, 2000) and caster-
drive(active-caster) type by (Wada, 1996).
The dual-wheel type has problems as follows.
Number of wheels is limited to two, and it is impos-
sible to get high friction or to adapt a rough terrain
by synchronous drive of many wheels. Moreover, a
passive wheel is needed to stabilize the posture of ve-
hicle.
The caster-drive wheel has offset between the
steering axis and the center of wheel. The wheel
can move in any direction by controlling the steer-
ing axis and the driving wheel independently by using
two motors. A holonomic omnidirectional motion of
a robot can be realized by using two or more caster-
drive wheels.
However, the caster-drive wheel has a problem as
follows. When the vehicle is in steady motion includ-
ing straight motion and rotation with constant curva-
ture, only the driving motor works and the steering
motor becomes idle. When the vehicle changes its
moving direction, high load is applied to the steering
motor. Therefore, high power is required both for the
driving and steering motor. It causes increase of mass.
The aim of our research is to develop a holonomic
omnidirectional mobile robot with caster-drive wheel
minimizing the motor power by using the interference
of output of two motors. New gearing mechanism is
proposed to realize the interference.
171
Kitagawa H., Ohno T., Ueno Y. and Terashima K. (2009).
DIFFERENTIAL-DRIVE STEERING SYSTEM USING PLANETARY GEARING FOR OMNIDIRECTIONAL MOBILE ROBOT.
In Proceedings of the 6th Inter national Conference on Informatics in Control, Automation and Robotics - Robotics and Automation, pages 171-176
DOI: 10.5220/0002191101710176
Copyright
c
SciTePress