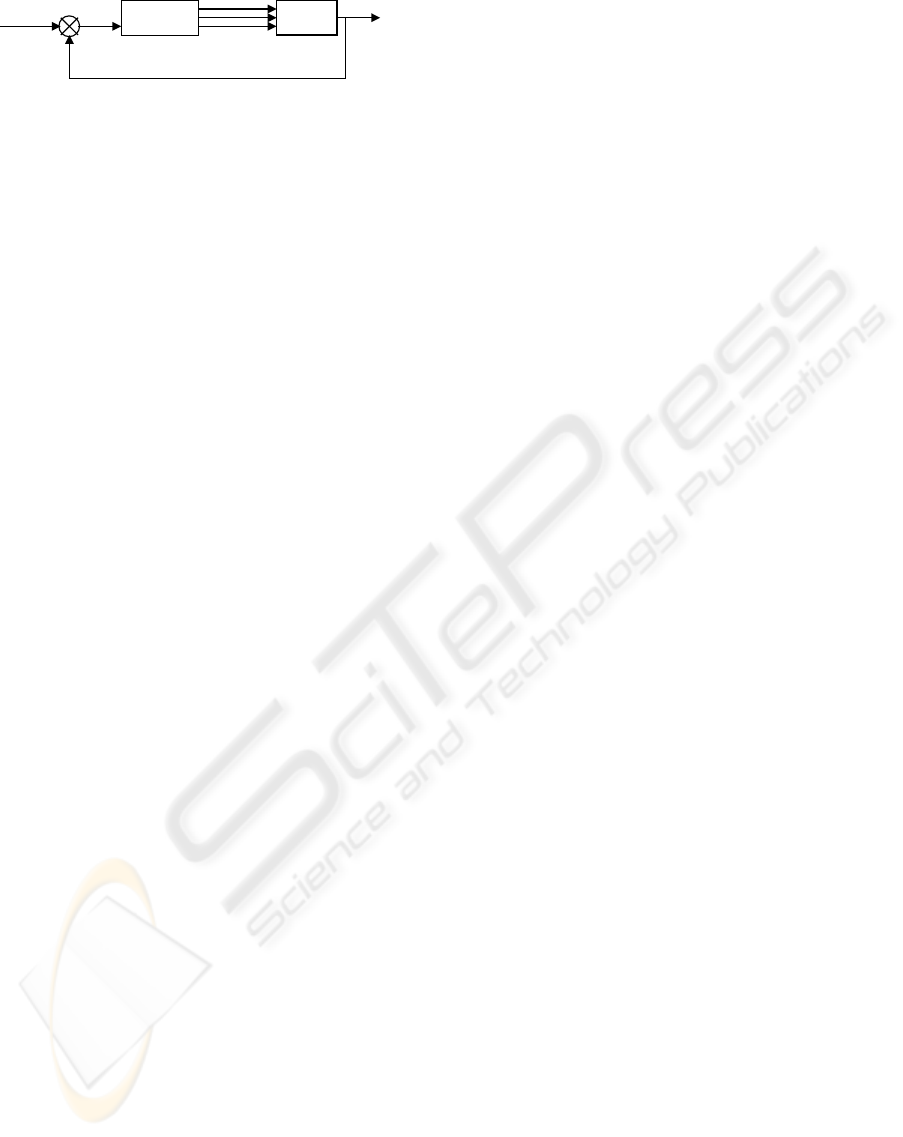
Figure 6: A dryer control diagram.
It has been verified that it is more effective to
switch the two flames of the burner than modifying
the speed of the rolls. The combination of an
ON/OFF control of burner with a PID control
actuating in roll speed makes it possible to achieve
an optimal control of humidity grain in these dryers.
In spite of this good behaviour of this type of
controls, we are developing robust control due to
long delays and disturbances in some cases. A work
of an implemented robust control in a similar
process can be viewed in (Cárdenas, 2003).
Simulations test show that the robust controller
performed well over a wide range of drying
conditions.
4 CONCLUSIONS
Process automation and supervision seem to promise
significant potential for development in the future.
The efficency of dryers has been increased
significantly. This has been achieved by making
them larger, more space efficient and by increasing
control and supervision systems. The incorporation
of these controls has also made itpossible to reduce
the grain humidity before it is stored into silos. In
addition, data collection and analysis, as well as
product traceability, ensures optimum quality for
customers and tools to enhance profitability.
The control method provide a new solution for
grain drying process.
Advanced controllers are being simulated with
good results and we expect to implement them in the
factory in the future for a better optimal energy
consumption.
ACKNOWLEDGEMENTS
This work was supported in part by “Programa
Nacional de Recursos y Tecnologías
Agroalimentarias”, (PROFIT) from the Spanish
Technology and Science Ministry.
REFERENCES
Bremner, H., 1997. An application of model-based fuzzy
control to an industrial grain dryer. Transactions of the
Institute of Measurement and Control, volume 19, nº4,
pages 185-191.
Balas, G., J. C. Doyle, K. Glover, A. Packard and R.
Smith., 1994.
μ
-Anaysis and Synthesis Toolbox for use
with MATLAB. The Mathworks.
Cárdenas, C., Garcia, J.D., Baeyens E., Olmos J.D., 2003.
Robust controllers for granulation processes in the
food industry. AFOT 03 Congress.
Chunyu, Z., Qinglei, C. et al., 2007. A model predictive of
a grain dryer with four stages based on recurrent fuzzy
neural network. In Springer Berlin, editor, Lectures
Notes in Computer Science, volume 4491, pages 29-
37.
De Dios, C. A. (1996). Secado de granos y secaderos.
Organización de las Naciones Unidas para la
agricultura y la Alimentación. Santiago, Chile
Guofang, L., Zhihuai, M., 2006. An intelligent controller
for grain dryer. American Society of Agricultural and
Biological Engineers. Paper nº 066197.
Janeiro, J., Moya, E., Garcia, D., Calvo, O., Cardenas, C.,
2006. Remote Supervisión and Maintenance of
Industrial Proceses. ICINCO´07 Congress.
Qiang, L., Bakker-Arkema, F.-W., 2001. Automatic
control of crossflow grain dryers, Part2: Design a
model-predictive controller. Journal of agricultural
engineering reseach.volume 80. nº2, pp 173-181.
Silva, J., Alves, G.R, Alves, B.M., 2003. A scale model of
a grain storage tower equipped with micro web
servers. International Journal of online engineering
Srzednicki, G., Hou, R., Driscoll, H. R., 2005.
Development of a control system for in-store drying of
paddy in Northeast China. Journal of Food
Engineering, volume 77, Issue 2, pages 386-377.
Zhang, Q., Litchfiled. 1993. Fuzzy logic control for a
continuos crossflow grain dryer. Journal of Food
Process Engineering. Volume 16, pages 59-57.
Cadder., 1992. Computer control system for continuous
and semi-continuous grain dryers. Result 106.
Building and industry publications.
CONTROL
PLANT
Humidity Reference
Feeding Time
Second flame ON/OFF
Roll Speed
Error
+
-
Measured Humidity
ICINCO 2009 - 6th International Conference on Informatics in Control, Automation and Robotics
408