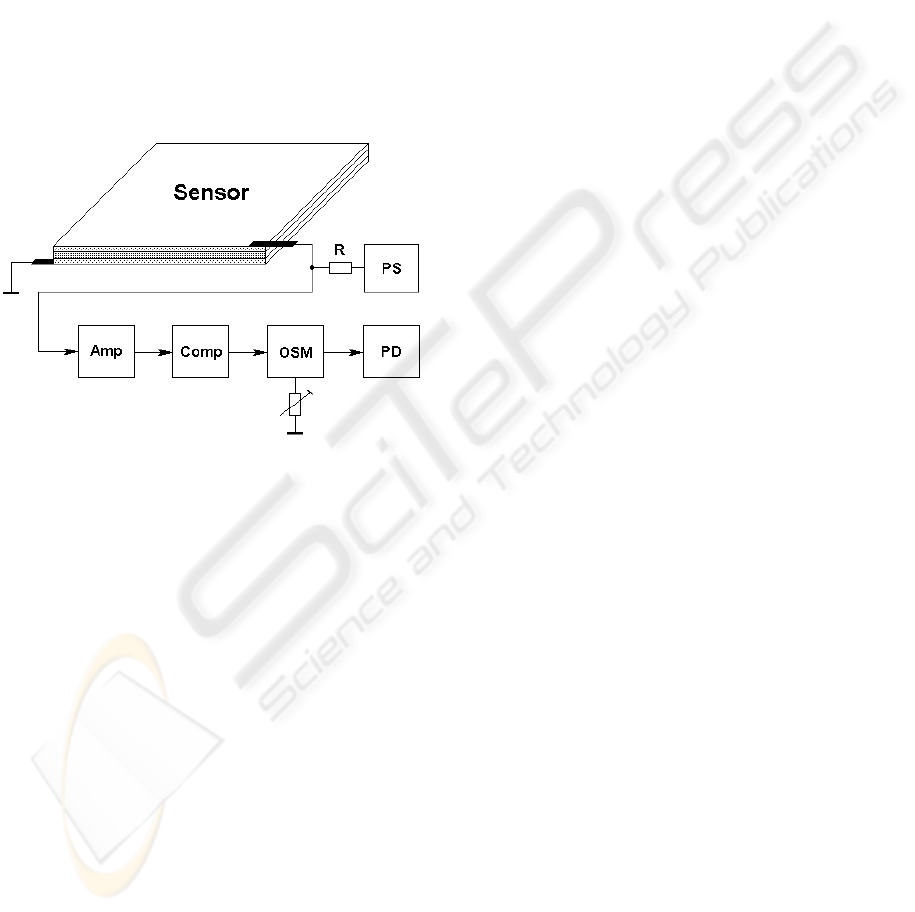
ACKNOWLEDGEMENTS
These elements are necessary to avoid noise from
induced currents and to flatten the wavefronts. The
first stage amplifies the signal in linear mode. The
second stage works in saturation mode. The output
of the amplifier is connected to the comparator
(Comp), which forms sharp wavefronts.
The research has been supported by Latvian
National Research program in Materials Science.
The authors are thankful to Mr. Dmitrij Jakovlew
from the Institute of Biomaterials and Biomechanics
of the Riga Technical University for the TEM
investigations.
These signals are passed to the differential circuit
and they form a sharp pulse, which is passed further
to the one-shot multivibrator (OSM).
The duration of the pulse of the OSM is
adjustable. The OSM is necessary to form the
determined length of pulse which is independent
from AEP sensor element deformation time. The
output of OSM is connected to performing device
PD (indicator/counter or actuator).
REFERENCES
Knite, M., Podins, G., Zike, S., Zavickis, J., Tupureina, V.,
2008. Elastomer – carbon nanostructure composites as
prospective materials for flexible robotic tactile
sensors. In Proc. of 5
th
International Conference on
Informatics in Control, Automation and Robotic, 1:
234-238.
Knite, M., Teteris, V., Polyakov, B., Erts, D., 2002.
Electric and elastic properties of conductive
polymeric nanocomposites on macro- and nanoscales.
Materials Science & Engineering C, 19: 5-19.
Knite, M., Teteris, V., Kiploka, A., Klemenoks, I., 2004.
Reversible tenso-resistance and piezo-rezistance
effects in conductive polymer-carbon nanocomposites.
Advanced Engineering Materials, 6: 742-746.
Qu, S., Wong, S., C., 2007. Piezoresistive behaviour of
polymer reinforced by expanded graphite. Composites
Science and Technology, 67, 231-237.
Li, X., Levy, C., Elaadil, L., 2008. Multiwalled carbon
nanotube film for strain sensing. Nanotechnology, 19:
045501 (7pp).
Figure 5: Block diagram of pressure-sensitive indication
circuit with completely elasto-plastic sensing element.
Sakale, G., Knite, M., Teteris, V., Tupureina, V., 2009.
Polyisoprene – nanostructured carbon composite
(PNCC) material for volatile organic compound
detection, Proc. of the International Scientific
Conference on Biomedical electronics and Devices
(BIODEVICES 2009), Porto, Portugal, 117.
4 CONCLUSIONS
Completely flexible polyisoprene – high-structured
carbon black all-elasto-plastic sensing element has
been designed, prepared and examined.
Job, A.E., Oliveira, F.A., Alves, N., Giacometti, J.A.,
Mattoso, L.H.C., 2003. Conductive composites of
natural ruber and carbon black for pressure sensors.
Syntetic metals, 135-136: 99-100.
The sensor element was composed of two
electrically conductive composite layers (electrodes)
and piezoresistive PNC layer (active element)
between them. A method for curing three-layer
hybrid composite for pressure sensing application
was developed. The joining in-between conductive
flexible electrodes and sensitive sensor material was
remarkably improved.
Knite, M., Klemenok, I., Shakale, G., Teteris, V., Zicans,
J., 2007. Polyisoprene-carbon nano-composites for
application in multifunctional sensors, Journal of
Alloys and Compounds, 434-435: 850-853.
Roldughin, V., I., Vysotskii, V., V., 2000. Percolation
properties of metal-filled films, structure and
mechanisms of conductivity, Progres in Organic
Coatings, 39: 81-100.
Hybrid three-layer polyisoprene/high-structure
carbon black composite has shown good pressure
sensing properties. Functioning model of low-
pressure-sensitive indication circuit which can turn
on suitable actuator has been made.
ICINCO 2009 - 6th International Conference on Informatics in Control, Automation and Robotics
412