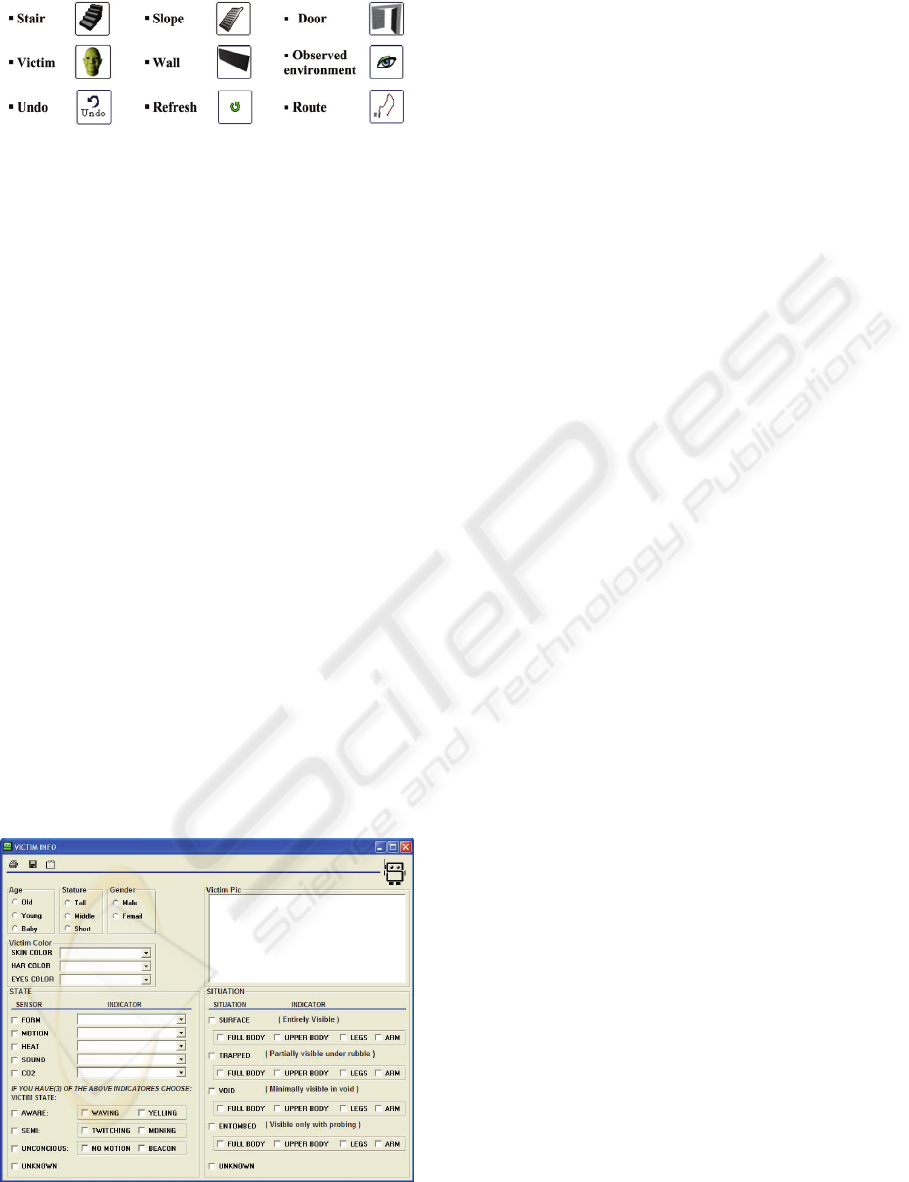
Figure 13: Symbols which are used in map generating.
Whenever the operator realizes that at the place
where the robot locates or at its surroundings, there
is a stair, wall, door, slope, or a victim, it can locate
a symbol of what it observes on the route map.
By using observed environment button and while
navigating the robot, the operator will mark the
places visited by the robot to prevent the repetitive
visiting and then, saves time. For returning to the
previous situation the operator just need to press
undo button.
While working, whenever the robot and the
computer are disconnected or whenever major errors
in the coordinates data or the data provided by
sensors are observed which may caused as a result of
robot damage, the operator can select the manual
mapping choice to illustrate the route. In this way,
he can enjoy the benefits of software in controlling
the robot and will face fewer errors.
In case that operator uses each of the above
objects in a wrong place, the software has the ability
to delete the object by a right click or to replace it by
a left click. The places in white colour show that
they are observed by the operator.
While observing an injured person, and placing
its symbol on the route map, another form will
appear for the operator in which the operator should
enter the related data to be recorded and also to be
used for the next reportages.
Figure 14: Form for recording the victim data.
9 CONCLUSIONS
Height adjustment and suspension systems enrich
the robot to go through the entirely destructed
buildings; however, it is not possible for it to cross
some obstacles such as steps. Robot mapping system
acts perfectly inside the buildings, but in the open
areas or the rubble it needs to improve. In the
improvement plan, these limitations must be
removed. In its final version, laser scanner and radio
positioning will be installed. The received
information plus the other sensors data result in a
better mapping achievement. It order to accelerate
its movement on the steps and through the obstacles,
some changes will be applied on the wheels and the
motion system.
ACKNOWLEDGEMENTS
Prof. Caro Lucas.
Dr. Soleiman Farshid Fam.
Dr. Sayyed Hassan Mir Hosseini.
REFERENCES
Heiraty, P., Aghajani, A., Chitsazan, M., 2008. The
applied knowledge of designing and building robot.
Azarakhsh publishing company. Tehran, 1
st
edition.
Borenstein, J., Everett, H. H., Feng, L., 1996. Where am I?
Sensors and Methods for Mobile Robot Positioning.
The University of Michigan. Michigan, 1
st
edition.
Ko, Albert., Y. K. Lau, Henry., 2009. Robot Assisted
Emergency Search and Rescue System With a Wireless
Sensor Network. International Journal of Advanced
Science and Technology field. Vol. 3, February.
Sandin, P. E., 2003. Robot Mechanisms and Mechanical
Devices Illustrated. McGraw-Hill Company. New
York, 1
st
edition.
Jacoff, A., Messina, E., Evans, J., 2000. A Standard Test
Course for Urban Search and Rescue Robots,
Intelligent Systems Division. National Institute of
Standards and Technology.
Jacoff, A., Messina, E., Evans, J., 2000. Experiences in
Deploying Test Arenas for Autonomous Mobile
Robots, Intelligent Systems Division. National Institute
of Standards and Technology.
RoboCup and AAAI rescue robot competition rules, 2008.
PROMOTION IN RESCUE ROBOT - According to the Experience Gained by Participating in Bam Earthquake Rescue
Operation
201