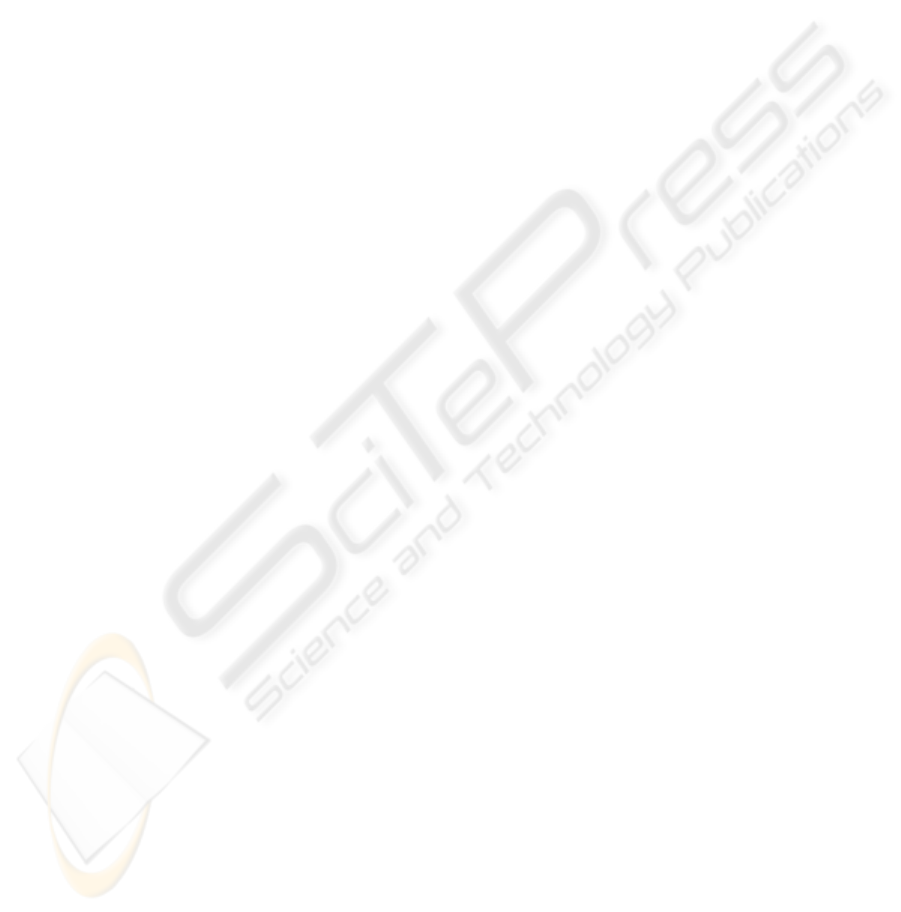
DETECTION OF A FAULT BY SPC AND IDENTIFICATION
A Method for Detecting Faults of a Process Controlled by SPC
Massimo Donnoli
DSEA – Dept. Electrical Systems and Automation, University of Pisa, Italy
Keywords: Statistical process control, Multivariate Hotelling statistic, System identification.
Abstract: A method for detecting the nature of a fault of a process controlled by SPC ( Statistical Process Control) is
presented. The method use the integration of SPC , traditional APC (Automatic Process Control) and the
System Identification technique . By a statistical on line control of the parameters of a transfer function and
the identification of the transfer function itself, the case of a fault due to a change in the system is
recognised. An algorithm called ‘batch control’ for the implementation of the method in a real plant is
proposed.
1 INTRODUCTION
The objective of Statistical Process Control (SPC) is
to detect situation of change of the natural behaviour
of a process by monitoring on line the key product
variables and detecting the cause of the fault,
indicating which variable or group of variables
contributes to the signal.
A lot of technique has been developed especially
due to the large and different areas where the SPC
could be applied.
If, traditionally, the SPC has been developed
especially to monitor the complicated processes of
chemical plants, after that, the big growth of the
information technology in the industries and the
large amount of process measures collected in the
data base of the control systems, has allowed the
implementation of SPC on almost every kind of
plant. By the way the common goal for the most
application is still to monitor the quality of the
process, treating the manufacturing process itself as
a black box, of which we know the inputs and
outputs, ignoring the others information of the
nature of the process.
In fact traditionally SPC and APC (Automatic
Process Control) have been developed in parallel
and only in the last years there has been works
where researchers have made the integration of the
two areas ( Tsung,1999).
Another point to remark is that the traditional
SPC approach, that is still the most diffused in many
kind of industries, is essentially the univariable SPC:
by the implementation of control charts like
Shewhart, Cusum, etc.. we look the magnitude of the
deviation of each variable independently of all
others as they are perfectly independent in the
process.
But the being ‘in control’ of a process is
essentially a multivariable property : in the modern
industrial processes the variables are non
independent of one another and only if the
simultaneous state of them all is in the joint
confidence region defined for the system, we could
say that the system is in control : by examining one
variable at time with the traditional charts it could
be that every variable is in the correct range but the
common state is not (Kourti & MacGregor,1994).
For this have been developed multivariable
methods that can treat all the variables
simultaneously.
The principal is the Hotelling or
2
statistic : it
transforms the state of all the variables in the
calculation of the value of a single variable which
can be monitor for detecting faults.
If this is a great effort to solve the problem in a
very useful way, on the other hand we have now the
problem to detect the cause of the fault, the variable
responsible.
This paper is organized as follows: in the next
section the basic concepts of SPC multivariable, the
Hotelling statistic and the interpretation of a
2
value are recalled. In sections 3 and 4 the main
advantages of SPC - APC integration and SPC -
System Identification integration are presented.
371
Donnoli M. (2009).
DETECTION OF A FAULT BY SPC AND IDENTIFICATION - A Method for Detecting Faults of a Process Controlled by SPC.
In Proceedings of the 6th International Conference on Informatics in Control, Automation and Robotics - Intelligent Control Systems and Optimization,
pages 371-375
DOI: 10.5220/0002203603710375
Copyright
c
SciTePress