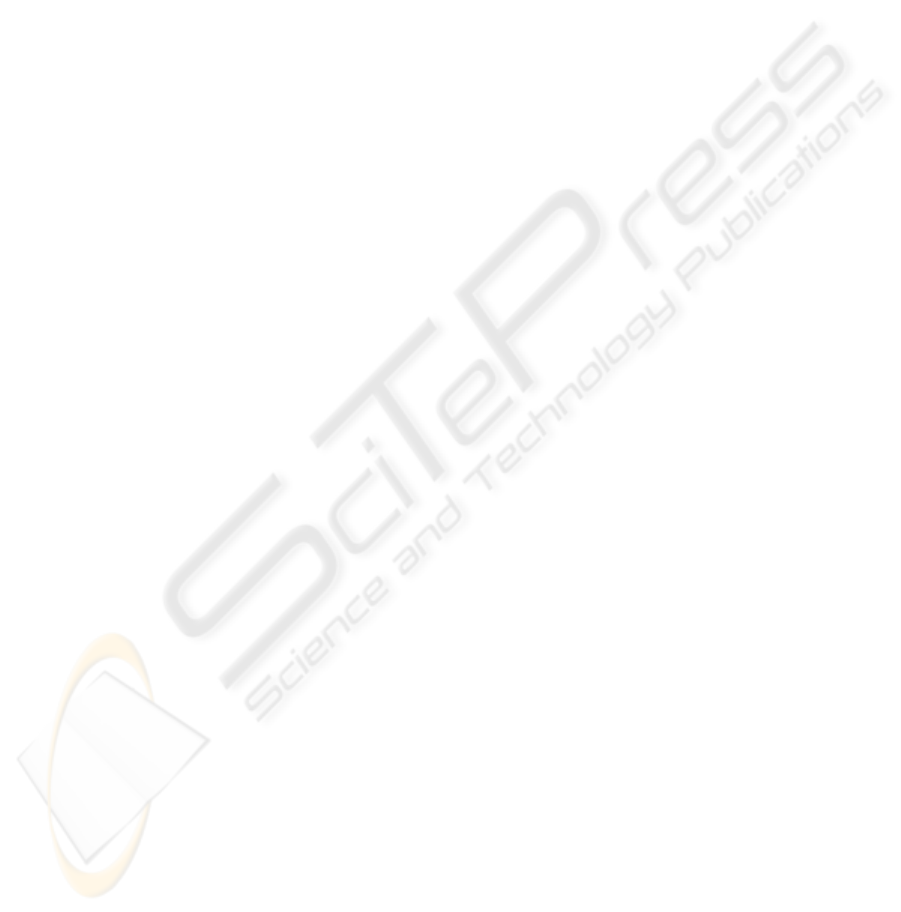
sensitivity functions as well, the generalization to
nonlinear processes (Cottenceau et al., 2001;
Johanyák and Kovács, 2007; Savaresi et al., 2006;
Andrade-Cetto and Thomas, 2008; Giua and Seatzu,
2008; Precup et al., 2008a; Dolgui et al., 2009)
including MIMO servo systems, and the mapping of
the results from the linear case onto the parameters
of the fuzzy controllers in the framework of state
feedback fuzzy control systems. The convergence
analysis of all IFT algorithms is needed.
ACKNOWLEDGEMENTS
The paper was supported by the CNMP & CNCSIS
of Romania. The first and fifth authors are doctoral
students with the “Politehnica” University of
Timisoara, Romania, and also SOP HRD
stipendiaries co-financed by the European Social
Fund through the project ID 6998.
REFERENCES
Andrade-Cetto, J., Thomas, F., 2008. A wire-based active
tracker. IEEE Transactions on Robotics. 24, 642-651.
Åström, K. J., Hägglund, T., 2000. Benchmark systems for
PID control. In Preprints of IFAC PID’00 Workshop.
Terrassa, Spain, 181-182.
Barut, M., Bogosyan, S., Gokasan, M., 2008.
Experimental evaluation of braided EKF for sensorless
control of induction motors. IEEE Transactions on
Industrial Electronics. 55, 620-632.
Costas-Perez, L., Lago, D., Farina, J., Rodriguez-Andina,
J. J., 2008. Optimization of an industrial sensor and
data acquisition laboratory through time sharing and
remote access. IEEE Transactions on Industrial
Electronics. 55, 2397-2404.
Cottenceau, B., Hardouin, L., Boimond, J.-L., Ferrier, J.-
L., 2001. Model reference control for timed event
graphs in dioids. Automatica. 37, 1451-1458.
Denève, A., Moughamir, S., Afilal, L., Zaytoon, J., 2008.
Control system design of a 3-DOF upper limbs
rehabilitation robot. Computer Methods and Programs
in Biomedicine. 89, 202-214.
De Santis, A., Siciliano, B., Villani, L., 2008. A unified
fuzzy logic approach to trajectory planning and
inverse kinematics for a fire fighting robot operating in
tunnels. Intelligent Service Robotics. 1, 41-49.
Dolgui A., Guschinsky, N., Levin, G., 2009. Graph
approach for optimal design of transfer machine with
rotary table. International Journal of Production
Research. 47, 321-341.
Giua, A., Seatzu, C., 2008. Modeling and supervisory
control of railway networks using Petri nets. IEEE
Transactions on Automation Science and Engineering.
6, 431-445.
Gomes, L., Costa, A., Barros, J. P., Lima, P., 2007. From
Petri net models to VHDL implementation of digital
controllers. In Proceedings of 33
rd
Annual Conference
of the IEEE Industrial Electronics Society (IECON
2007). Taipei, Taiwan, 94-99.
Hjalmarsson, H., 1999. Efficient tuning of linear
multivariable controllers using Iterative Feedback
Tuning. International Journal of Adaptive Control and
Signal Processing. 13, 553-572.
Hjalmarsson, H., Birkeland, T., 1998. Iterative Feedback
Tuning of linear time-invariant MIMO systems. In
Proceedings of 37
th
IEEE Conference on Decision and
Control. Tampa, FL, 3893-3898.
Hjalmarsson, H., Gevers, M., Gunnarsson, S., Lequin, O.,
1998. Iterative Feedback Tuning: theory and
applications. IEEE Control Systems Magazine. 18, 26-
41.
Hjalmarsson, H., Gunnarsson, S., Gevers, M., 1994. A
convergent iterative restricted complexity control
design scheme. In Proceedings of 33
rd
IEEE
Conference on Decision and Control. Lake Buena
Vista, FL, 1735-1740.
Horváth, L., Rudas, I. J., 2004. Modeling and Problem
Solving Methods for Engineers. Burlington, MA:
Academic Press, Elsevier.
Isermann, R., 2003. Mechatronic Systems: Fundamentals.
Berlin, Heidelberg, New York: Springer-Verlag.
Jansson, H., Hjalmarsson, H., 2004. Gradient
approximations in Iterative Feedback Tuning for
multivariable processes. International Journal of
Adaptive Control and Signal Processing. 18, 665-681.
Johanyák, Z. C., Kovács, S., 2007. Sparse fuzzy system
generation by rule base extension. In Proceedings of
11
th
International Conference on Intelligent
Engineering Systems (INES 2007). Budapest,
Hungary, 99-104.
Kovács, G. L., 2006. Management and production control
issues of distributed enterprises. In Proceedings of
PROLAMAT 2006 IFIP TC5 International
Conference. Shanghai, China, 11-20.
Orlowska-Kowalska, T., Szabat, K., 2008. Damping of
torsional vibrations in two-mass system using adaptive
sliding neuro-fuzzy approach. IEEE Transactions on
Industrial Informatics. 4, 47-57.
Petres, Z., Baranyi, P., Korondi, P., Hashimoto, H., 2007.
Trajectory tracking by TP model transformation: case
study of a benchmark problem. IEEE Transactions on
Industrial Electronics. 54, 1654-1663.
Pfeiffer, D., Stephens, R. I., Vinsonneau, B., Burnham, K.
J., 2006. Iterative Feedback Tuning applied to a ship
positioning controller. In Proceedings of 18
th
International Conference on Systems Engineering
(ICSE 2006). Coventry, UK, 353-358.
Precup, R.-E., Preitl, S., Fodor, J., Ursache, I.-B., Clep, P.
A., Kilyeni, S., 2008a. Experimental validation of
Iterative Feedback Tuning solutions for inverted
pendulum crane mode control. In Proceedings of 2008
Conference on Human System Interaction (HSI 2008).
Krakow, Poland, 536-541.
Precup, R.-E., Preitl, S., Rudas, I. J., Tomescu, M. L., Tar,
ITERATIVE FEEDBACK TUNING APPROACH TO A CLASS OF STATE FEEDBACK-CONTROLLED SERVO
SYSTEMS
47