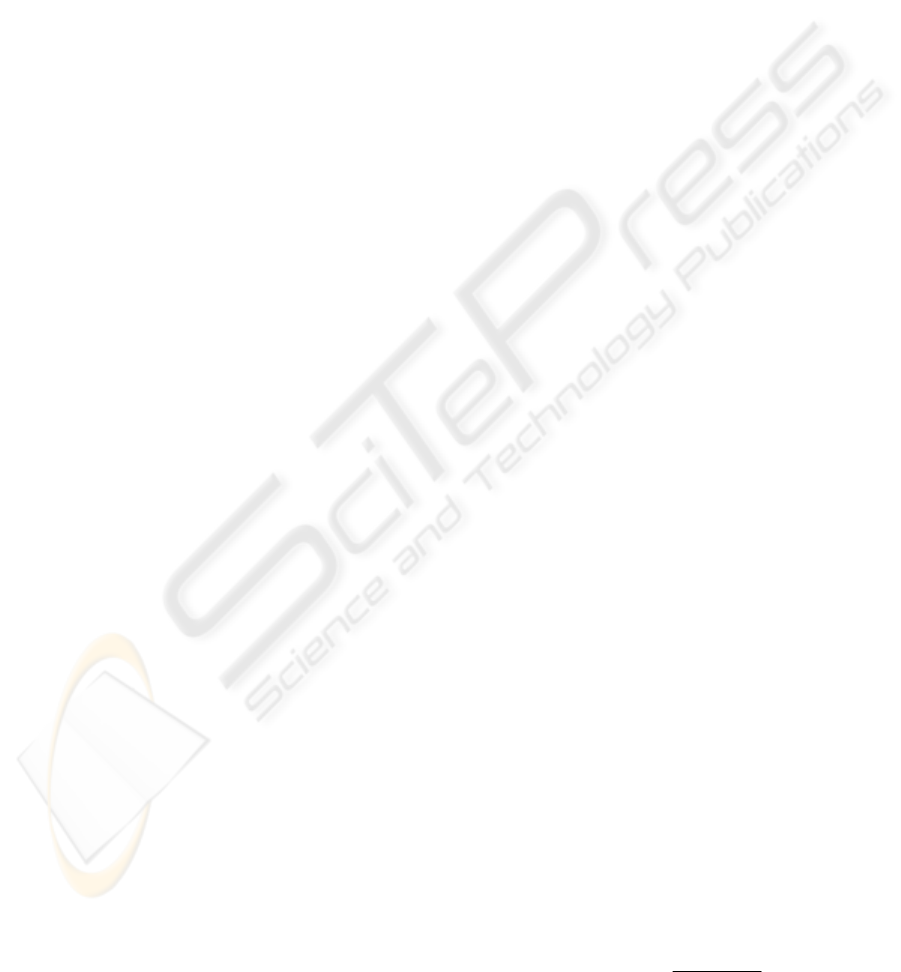
between both algorithms lie in the initialization
phase, the crossover operator, and the mutation
operator. These operators have the same goal in both
algorithms; the difference lies in the way in which
each operator is applied in the corresponding
algorithm. These operators are applied at the joint’s
path level in case of the CGA while they are applied
at the path point level in case of conventional
genetic algorithm. That is, the operators of the CGA
are of global nature while those of conventional
genetic algorithm are of local nature. In addition to
that, it is to be noted that the conventional genetic
algorithm uses the genotype and phenotype data
presentations while the CGA uses only the
phenotype data presentation. This fact requires a
coding process in conventional genetic algorithm,
which is not the case in CGA. The CGA is fully
described in (Abo-Hammour et al, 2002). The reader
is kindly asked to read this reference for the
complete details about it.
The operators of the conventional genetic
algorithm that include the initialization phase, the
crossover operator, and the mutation operator are
applied at the path point level. In relation to the
initialization phase, individuals are generated
randomly at the gene level. Conventional crossover
involves exchanging genes between each pair of
parents selected from mating pool. It is generally
applied with relatively high probability of crossover,
P
c
. Regarding the mutation operator, the bitwise
complement mutation is applied in the conventional
genetic algorithm at the gene level with some low
probability of mutation, P
m
. It is realized by
performing bit inversion (flipping) on some
randomly selected bit positions of children bit
strings.
To summarize the evolution process in
conventional genetic algorithm, an individual is a
candidate solution of the joints’ angles; that is, each
individual consists of a string of L=M* N
k
* N
s
genes. Initially, N
p
individuals are randomly
generated representing the initial population. The
population undergoes the selection process, which
results in a mating pool among which pairs of
individuals are crossed with probability P
c
. This
process results in an offspring’s generation where
every individual child undergoes mutation with
probability P
m
. After that, the next generation is
produced according to the replacement strategy
applied. This process is repeated till the convergence
criterion is met where the M
×
N
k
parameters of the
best individual are the required joints’ angles.
4 SIMULATION RESULTS
The CGA and the conventional genetic algorithm
were used to solve the Cartesian path generation
problem of 2R and 3R planar manipulators. The
initial settings of the CGA parameters are as
follows: the population size is set to 500 individuals.
The rank-based selection strategy is used where the
rank-based ratio is set to 0.1. The individual
crossover probability is kept at 0.9; the joint
crossover probability is also set to 0.9. The
individual mutation probability and the joint
mutation probability are kept at 0.9. Generational
replacement scheme is applied where the number of
elite parents that are passed to the next generation is
one-tenth of the population. The genetic algorithm is
stopped when one of the following conditions is met.
First, the fitness of the best individual of the
population reaches a value of 0.99; that is the
accumulative deviation of the end-effector, E, of the
best individual is less than or equal to 0.01. Second,
the maximum deviation at any path point of the best
individual is less than or equal to 0.001. Third, a
maximum number of 10000 generations is reached.
Fourth, the improvement in the fitness value of the
best individual in the population over 1000
generations is less than 0.01. It is to be noted that the
first two conditions indicate to a successful
termination process (optimal solution is found),
while the last two conditions point to a partially
successful end depending on the fitness of the best
individual in the population (near-optimal solution is
reached).
The initial settings of the conventional genetic
algorithm parameters are similar to those of the
CGA except those related to crossover, mutation and
coding process which are as following: the crossover
probability is kept at 0.7, the mutation probability is
kept at 0.01. The uniform crossover method is used
as the algorithm’s default crossover method. The
required accuracy of the phenotype values is set to
0.001 and binary coding scheme is used.
Due to the stochastic nature of GAs, twelve
different runs were made for every result obtained in
this work using a different random number generator
seed; results are the average values whenever
possible.
The selected Cartesian path generation problem
is of straight line shape as given by:
25.0x,0.0x
finalinitial
==
)1i(*
1N
xx
x)i(X)i,1(P
k
initialfinal
initialdcdc
−
−
−
+==
(6)
kdcdc
NiiYiP ≤≤
1,25.0)(),2(
ICINCO 2009 - 6th International Conference on Informatics in Control, Automation and Robotics
420