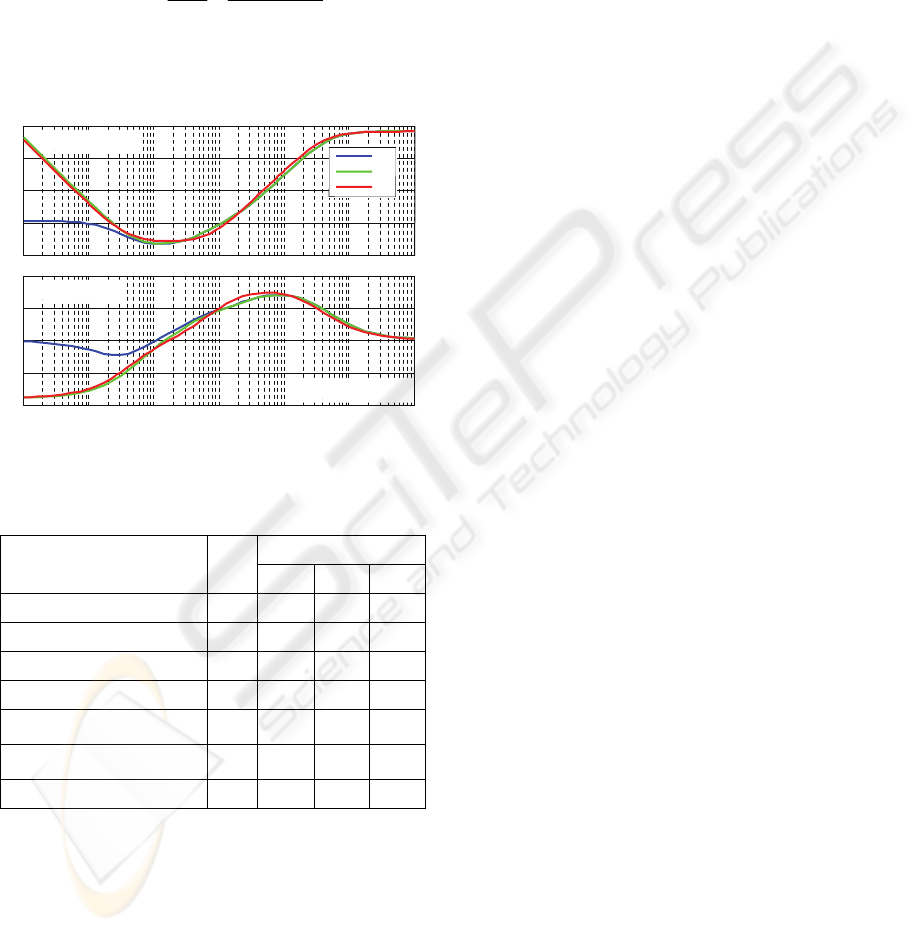
Figure 12 shows the mold level when the delay
changes during bulging whose frequency is 0.05Hz.
Using
2
M , the performances remain better than
those of the PID.
2
M can also be approached by a PID control law
(see Figure 13 for the Bode diagrams) as follows:
⎟
⎠
⎞
⎜
⎝
⎛
+
++=
s
s
s
M
0.00251
12.037.0
151.0
3
Finally, the performances of all the versions of
the Aström’s modified Smith predictor are summa-
rized and compared with those of the PID in Table 2.
Figure 13: Bode diagrams of all the versions of Aström
predictor.
Table 2: Performances of the proposed control laws.
Specifications PID
Aström predictor
1
M
2
M
3
M
Cutoff frequency (rad/s) 1.06 1.3 1.3
1.41
Gain margin (dB) 8.7
10.1 9.9 10.4
Phase margin (°) 66
54 46 42
Delay margin (s) 1.1
0.75 0.61 0.52
)(max
11
]Hz1.003.0[
ω
jB
∈
(dB)
9
7.2 8.1 7.1
)(mi
11
]Hz1.003.0[
ω
jB
∈
(dB)
8
2 -1.1 -0.6
Steady state error % outflow
0
small 0 0
5 CONCLUSIONS
This paper presents an effective method based on
∞
H control theory combined with the Aström’s
modified Smith predictor which enhances the
disturbance rejection performance compared to the
conventional Smith predictor. This one cannot
indeed be utilized in the mold level control process
since it leads to a steady state error as a response to a
step disturbance.
Using simple tuning rules, the level error was
reduced compared to the PID control with regards to
robust stability. Moreover, this technique allows
shaping the disturbance rejection independently
from the closed loop response time which is not the
case for PID. Further improvements may include
additional features as the introduction of observers
and feed-forward actions.
REFERENCES
Kurokawa, T., Kato, Y., Kondo T., 1992. Development of
CC mold level adaptive control system. Current
Advances in Materials and Processes, 5(2):354.
Matoba, Y., Yamamoto, T., Tozuda, M., Watanabe, T.,
Tomono, H., 1990. Instrumentation and control
technology for supporting high-speed casting. In 9
th
PTD Process Technol. Conf. Proc.
Jabri, K., Mouchette, A., Bèle, B., Godoy, E., Dumur, D.,
2008a. Disturbances estimation for mold level control
in the continuous casting process. In 5
th
International
Conference on Informatics in Control, Automation and
Robotics ICINCO, Funchal, Portugal.
Yoon, U-S., Bang, I.-W., Rhee, J.H., Kim, S.-Y., Lee, J.-
D., Oh, K.H., 2002. Analysis of mold level hunching
by unsteady bulging during thin slab casting. ISIJ
International, 42(10):1103-1111.
Thomas, B.G., Bai, H., 2001. Tundish nozzle clogging –
application of computational models. In 18
rd
PTD
Conf. Proc., Baltimore (US).
Lim, D.J., Jeong, H.S., Hong, D.H., 1990. A Study on the
Mold Level Control of Continuous Casting System.
Chen, Y.D., Tung, P.C., Fuh, C.C., 2007. Modified Smith
predictor scheme for periodic disturbance reduction in
linear delay systems. Journal of Process Control,
17:799-804.
Aström, K.J., Hang, C.C., Lim, B.C., 1994. A new smith
predictor for controlling a process with an integrator
and long dead-time. IEEE Trans. on Automatic
Control, 39(2):343-345.
Guanghui, Z., Feng, Q., Huihe, S., 2007. Robust tuning
method for modified Smith predictor. Journal of
Systems Engineering and Electronics, 18(1):89-94.
Zhang, F., Hosoe, S., Kouno, M., 1991. Synthesis of
robust output regulators via H
∞
control. In 13
th
SICE
Symp. Dynamical Syst. Theory.
Glover, K. et al, 1988. State space formula for all
stabilizing controllers that satisfy an H
∞
norm bound
and relations to risk sensitivity. Systems and Control
Letters, 11:167-172.
Jabri, K., Mouchette, A., Bèle, B., Godoy, E., Dumur, D.,
2008b. “Suppression of periodic disturbances in the
continuous casting process”. In Proc. Multi-
conference on Systems and Control MSC, San Antonio
(US).
10
-2
10
-1
10
0
10
1
10
2
10
3
10
4
-10
0
10
20
30
10
-2
10
-1
10
0
10
1
10
2
10
3
10
4
-100
-50
0
50
100
M1
M2
M3
Frequency (rad/sec)
Magnitude (dB)
Phase (degree)
PERIODIC DISTURBANCES REDUCTION IN THE CONTINUOUS CASTING PROCESS BY MEANS OF A
MODIFIED SMITH PREDICTOR
115