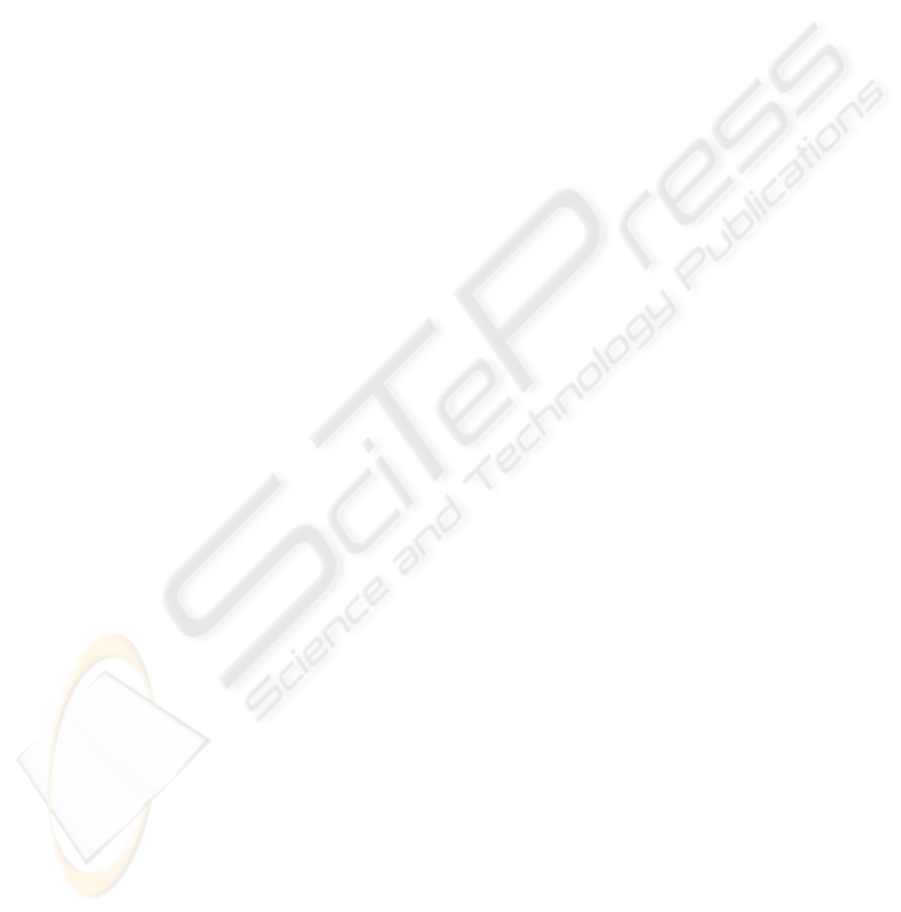
4 CONCLUSIONS
Advances in digital control have allowed the power
electronics of servo amplifiers to be manipulated in
a way that will improve servomechanism precision
without modification to the mechanical plant.
A previously developed hybrid PID + Impulse
controller which does not require the mechanism to
come to a complete stop between pulses has been
modified to further improve accuracy in the presence
of stick-slip friction. This modification transitions
the decay of the impulse torque command at higher
velocities. Many experimental tests showed that this
innovation provided substantial additional
improvement in the mechanism’s position accuracy
in comparison with other control strategies. This has
been demonstrated on a servomechanism which is
typical of those used to control each axis of
industrial mechanisms such as a robot arm.
Future work is proceeding on optimising the
parameters using a method generic to any
mechanism, which does not rely on trial and error
and is applicable to a greater rang of trajectories.
REFERENCES
Armstrong-Hélouvry, B., 1991, “Control of Machines with
Friction” Kluwer Academic Publishers, 1991, Norwell
MA.
Armstrong-Hélouvry, B., Dupont, P., and Canudas de
Wit, C., 1994, “A survey of models, analysis tools and
compensation methods for the control of machines
with friction” Automatica, vol. 30(7), pp. 1083-1138.
Canudas de Wit, C., Olsson, H., Åström, K. J., 1995 ”A
new model for control of systems with friction” IEEE
Tansactions on Automatic Control, vol. 40 (3), pp.
419-425.
Dahl, P., 1968, “A solid friction model” Aerospace Corp.,
El Segundo, CA, Tech. Rep. TOR-0158(3107-18)-1.
Dahl, P, 1977, “Measurement of solid friction parameters
of ball bearings” Proc. of 6
th
annual Symp. on
Incremental Motion, Control Systems and Devices,
University of Illinois, ILO.
Hojjat, Y., and Higuchi, T., 1991 “Application of
electromagnetic impulsive force to precise
positioning” Int J. Japan Soc. Precision Engineering,
vol. 25 (1), pp. 39-44.
Johannes, V. I.., Green, M.A., and Brockley,C.A., 1973,
“The role of the rate of application of the tangential
force in determining the static friction coefficient”,
Wear, vol. 24, pp. 381-385.
Johnson, K.L., 1987, “Contact Mechanics” Cambridge
University Press, Cambridge.
Kato, S., Yamaguchi, K. and Matsubayashi, T., 1972,
“Some considerations of characteristics of static
friction of machine tool slideway” J. o Lubrication
Technology, vol. 94 (3), pp. 234-247.
Li, Z, and Cook, C.D., 1998, ”A PID controller for
Machines with Friction” Proc. Pacific Conference on
Manufacturing, Brisbane, Australia, 18-20
August,
1998, pp. 401-406.
Ogata, K., Modern Control Engineering. 1990,
Englewood Cliffs, New Jersey: Prentice Hall.
Olsson, H., 1996, “Control Systems with Friction”
Department of Automatic Control, Lund University,
pp.46-48.
Popovic, M.R., Gorinevsky, D.M., Goldenberg, A.A.,
2000, “High precision positioning of a mechanism
with non linear friction using a fuzzy logic pulse
controller” IEEE Transactions on Control Systems
Technology, vol. 8 (1) pp. 151-158.
Rabinowicz, E., 1958, “The intrinsic variables affecting
the stick-slip process,” Proc. Physical Society of
London, vol. 71 (4), pp.668-675.
Richardson, R. S. H., and Nolle, H., 1976, “Surface
friction under time dependant loads” Wear, vol. 37
(1), pp.87-101.
van Duin, S., 2006, “Impulse Control Systems for
Servomechanisms with Nonlinear Friction”, Ph.D.
dissertation, University of Wollongong.
van Duin, S, Cook, C., Li, Z., Alici, G., 2007, “A modified
impulse controller for Improved Accuracy of Robots
with Friction”, Proceedings International Conference
on Informatics in Control, Automation and Robotics,
Angers, France.
Yang, S., Tomizuka, M., 1988, “Adaptive pulse width
control for precise positioning under the influence of
stiction and Coulomb friction” ASME J .od Dynamic
Systems, Measurement and Control, vol. 110 (3), pp.
221-227.
TRANSITION VELOCITY FUNCTION FOR IMPULSE CONTROL SYSTEMS
221