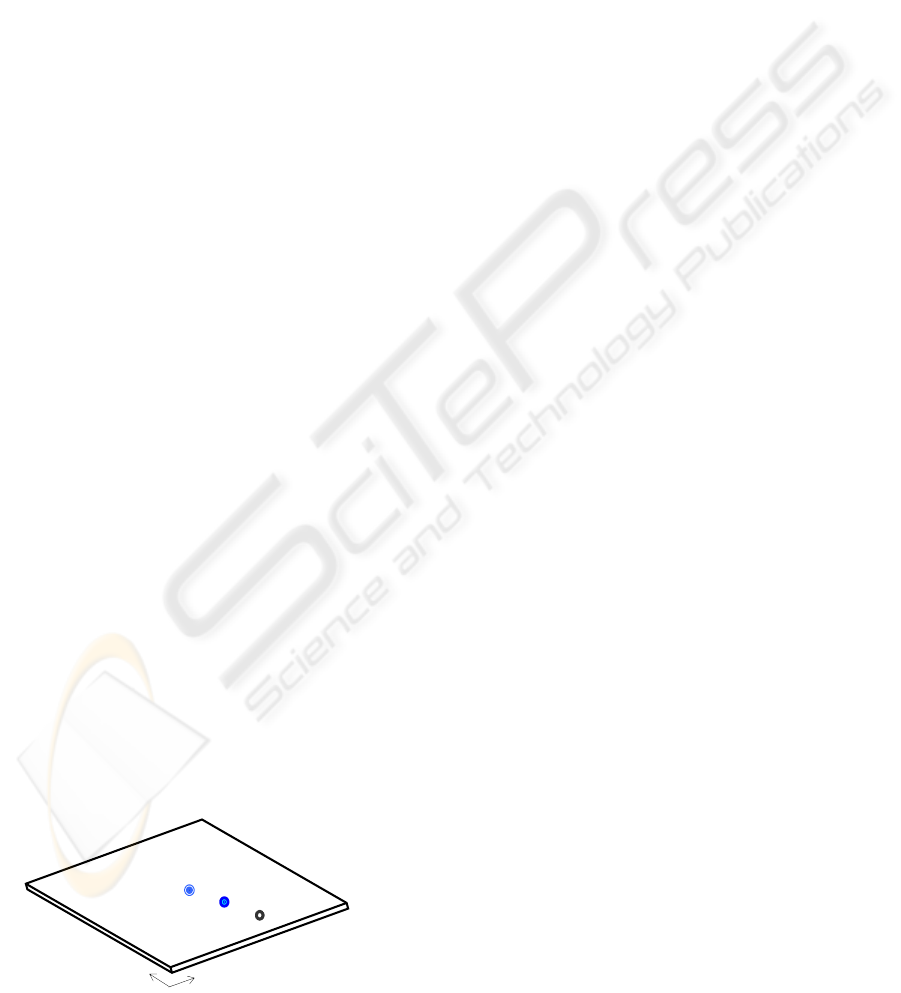
the algorithms in modeling the system using various
excitation signals such as finite duration step,
random and pseudo random binary signal (PRBS).
Results and discussions of the model validity
through input/output mapping, mean square of
output error and frequency domain response are also
presented. Parametric modelling is also confirmed
with convergence of fitness values and time run.
Finally, the paper is concluded in Section 5.
2 THE FLEXIBLE PLATE
SYSTEM
Dynamic simulation of a plate structure using the
finite differences (FD) method is considered in this
paper. The finite difference method is used to
discretise the governing dynamic equation
considered with no damping and the lateral
deflection of plates is obtained using central finite
difference method. It then transformed into state
space equation as the following equation.
W
i,j,k+1
= (A+2
ijk
)W
i,j,k
+ BW
ijk
+ CF (1)
Where 2
ijk
represents the diagonal elements of (2/c),
C=(
Δ
t
2
/
ρ
), c=-DC, and W
i,j,k+1
is the deflection of
grid points i = 1, 2,……, n+1 and j = 1, 2,.., m+1 at
time step k+1. W
i,j,k
and W
ijk
are the corresponding
deflections at time steps k and k-1 respectively. A is
constant (n+1)(m+1) x (n+1)(m+1) matrix whose
entries depend on physical dimensions and
characteristics of the plate, B is a diagonal matrix of
-1 corresponding to W
i,j,k
and C is a scalar related to
the given input and
is an (n+1)(m+1) x 1 matrix
known as the forcing matrix. The algorithm is
implemented in Matlab/SIMULINK with applied
external force or disturbance into all clamped edges
plate. Twenty two equal divisions of plate elements
with dimension 1.0mm× 1.0mm× 0.00032m is
measured at the detection and observation points
(Figure 1). Parameters of the plate considered
comprise mass density per area, ρ = 2700 kg/m
2
,
Young’s Modulus, E = 7.11 x 10
10
N/m
2
, second
moment of inertia, I = 5.1924 x 10
-11
m
2
and Poisson
ratio, υ = 0.3 with sampling time 0.001.
Detector
Observer
Primary Source
(12Δx, 12Δy)
(14Δx, 10
y)
(17Δx, 7Δy)
y
Δx = 45.455 mm
Δy = 45.455 mm
12Δx, 12Δy
17Δx, 17Δy
14Δx, 14Δy
Figure 1: The flexible plate system.
3 REAL CODED GENETIC
ALGORITHM
In most of practical engineering problems, the real-
coded GA is more suitable than the binary-coded
GA, as transformations from real number to binary
digits may suffer from loss of precision. Genetic
operations are very important to the success of
specific GA applications. In this work, real-coded
representation is used to determine the model order
of the plant and subsequently identify parametric
model of the system. The initial population is
created randomly within [-1,1] range. The main
three genetic operators involved are described
below.
3.1 Selection
Selection is the process of determining the number
of times or trials a particular individual in the
population is chosen for reproduction (Chipperfield,
1994). The process includes two steps, namely
selection probability and sampling algorithm.
Selection probability is concerned with
transformation of raw fitness values into real as
expected of an individual to reproduce. Sampling
algorithm reproduces individuals based on the
selection probabilities computed before. This
process is repeated as often as individuals must be
chosen. There are many methods reported such as
roulette wheel selection, stochastic universal
sampling and tournament selection, etc. The
stochastic universal sampling (SUS) method is used
in this work that randomly copies chromosomes and
simulates N equally distributed pointers. SUS is a
simpler algorithm, and as individuals are selected
entirely on their position in the population, SUS has
zero bias. After selection has been carried out, the
construction of the intermediate population is
complete and the crossover and mutation operators
are then applied.
3.2 Crossover (Recombination)
Crossover produces new individuals that have some
parts of both parent’s genetic material (Chipperfield,
1994). However, Mühlenbein et. al (1991) have
distinguished between recombination and crossover.
The mixing of the variables was called
recombination and the mixing of the values of a
variable was named crossover. Line recombination
employed in this work performs an exchange of
variable values between the individuals. By using a
real-valued encoding of the chromosome structure,
REAL-CODED GENETIC ALGORITHM IDENTIFICATION OF A FLEXIBLE PLATE SYSTEM
125