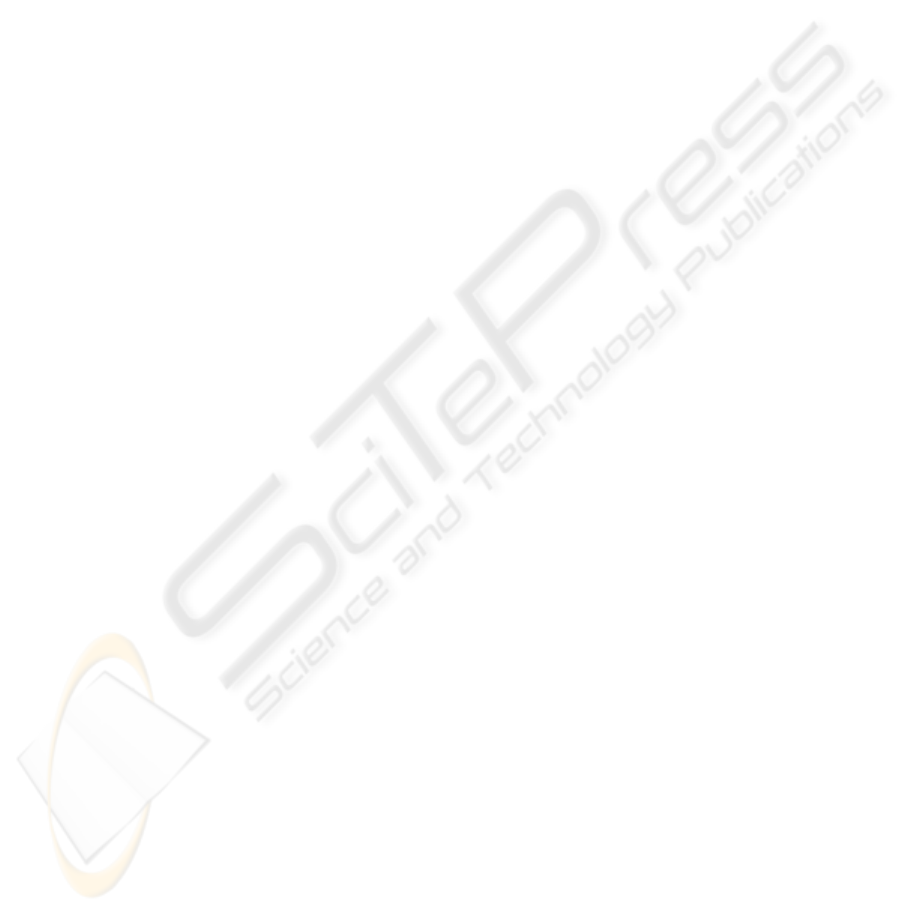
problem is that the evolutionary (or genetically)
evolved fuzzy controllers might perform optimal
only under the conditions involved in the evolution
process. In this paper we examine the performance
of evolutionary optimized controllers in contrast to
heuristically designed fuzzy controllers. For
comparisons purposes we test the controllers in
conditions different from the ones they have been
designed for. In this way, some useful insights
regarding the design robustness of the evolutionary
tuned fuzzy controllers may be drawn.
The rest of the paper is organized as follows.
Section 2 describes the evolutionary fuzzy
scheduling concept that is used for WIP
minimization. Two control approaches are
presented: the distributed and the supervised one.
Section 3 describes the comparison scenarios and
presents experimental results for production lines
and networks. Issues for discussion and remarks as
well as suggestions for further development are
presented in the last section.
2 EVOLUTIONARY-FUZZY
SCHEDULING
A production network consists of machines
(operation stations) and buffers (storage areas).
Items are received at each machine and wait for the
next operation in a buffer with finite capacity. WIP
may increase because of unanticipated events, like
machine breakdowns and potential consequent
propagation of these events. For example, a failed
machine with operational neighbours forces to an
inventory increase of the previous storage buffer. If
the repair time is big enough, then the broken
machine will either block the previous station or
starve the next one. This “bottleneck” effect will
propagate throughout the system.
Clearly, production scheduling of realistic
manufacturing plants must satisfy multiple
conflicting criteria and also cope with the dynamic
nature of such environments. Fuzzy logic offers the
mathematical framework that allows for simple
knowledge representations of the production
control/scheduling principles in terms of IF-THEN
rules. The expert knowledge that describes the
control objective (that is WIP reduction) can be
summarized in the following statements
(Tsourveloudis et al, 2000, Tsourveloudis et al.,
2006):
If the surplus level is satisfactory then try to
prevent starving or blocking by increasing or
decreasing the production rate accordingly,
else
If the surplus is not satisfactory that is either too
low or too high then produce at maximum or zero
rate respectively.
In fuzzy logic controllers (FLCs), the control
policy is described by linguistic IF-THEN rules
similar to the above statements. The essential part of
every fuzzy controller is the knowledge acquisition
and the representation of the extracted knowledge
with certain fuzzy sets/membership functions.
Membership functions (MFs) represent the
uncertainty modelled with fuzzy sets by establishing
a connection between linguistic terms (such as low,
negative, high etc) and precise numerical values of
variables in the physical system. The correct choice
of the MFs is by no means trivial and plays a crucial
role in the success of an application. If the selection
of the membership functions is not based on a
systematic optimization procedure then the adopted
fuzzy control strategy cannot guarantee minimum
WIP level.
The evolutionary-fuzzy synergy attempts to
minimize the empirical/expert design and create
MFs that fit best to scheduling objectives
(Tsourveloudis et al., 2006). In this context, the
design of the fuzzy controllers (distributed or
supervisory) can be regarded as an optimization
problem in which the set of possible MFs constitutes
the search space. Evolutionary Algorithms (EAs) are
seeking optimal or near optimal solutions in large
and complex search spaces and therefore have been
successfully applied to a variety of scheduling
problems with broad applicability to manufacturing
systems (Tedford and Lowe, 2003). The objective is
to optimize a performance measure which in the
EAs context is called fitness function. In each
generation, the fitness of every chromosome is first
evaluated based on the performance of the
production network system, which is controlled
through the membership functions represented in the
chromosome. A specified percentage of the better
fitted chromosomes are retained for the next
generation. Then parents are selected repeatedly
from the current generation of chromosomes, and
new chromosomes are generated from these parents.
One generation ends when the number of
chromosomes for the next generation has reached
the quota. This process is repeated for a pre-selected
number of generations.
2.1 Distributed Evolutionary-fuzzy
Control
The architecture of the distributed evolutionary-
fuzzy WIP control scheme is extensively discussed
ON THE WORK-IN-PROCESS CONTROL OF PRODUCTION NETWORKS
223