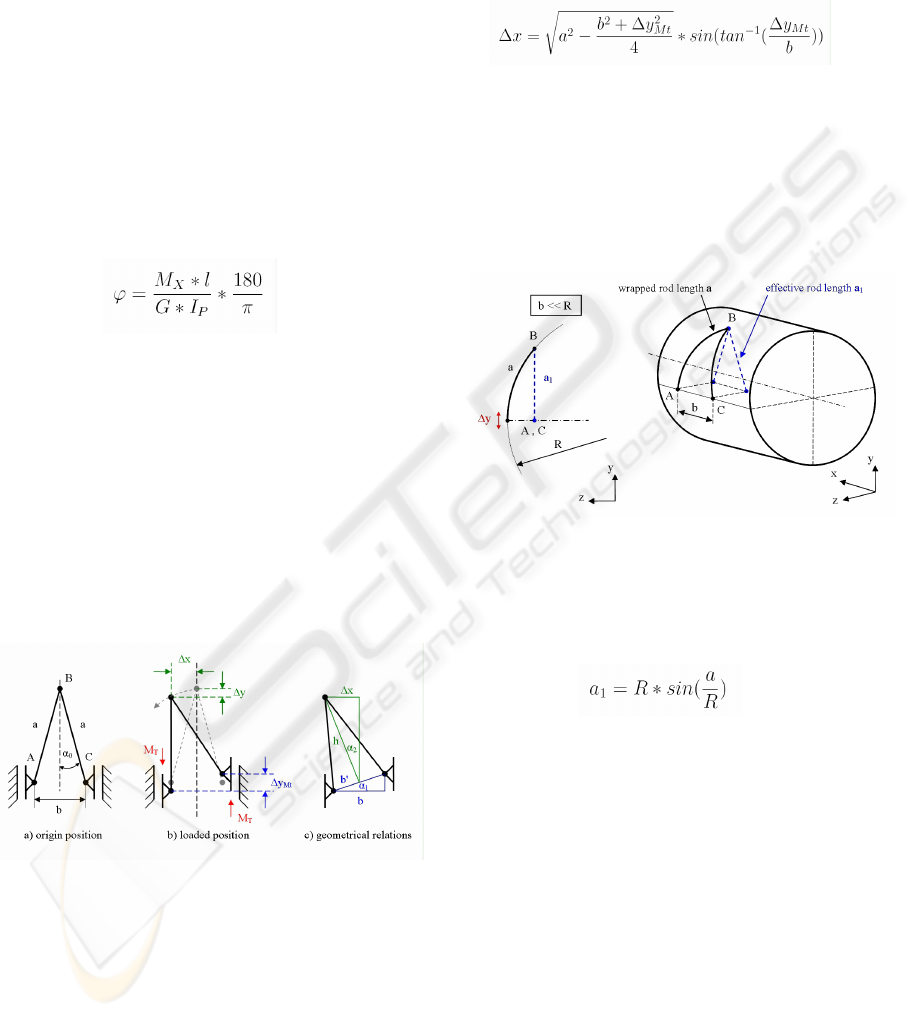
3 SENSOR OPTIMIZATION
This chapter describes the basic kinematical
principle and the FEM-optimization of the torque
sensor geometry (Marik, 2008). Optimization
criteria are the translational movement Δx, but also
the costs for manufacturing and assembling.
3.1 Kinematical Principle
Basically the sensibility of the torque sensor depends
on the translation ∆x which is directly linked to the
current torsion angle. The formal correlation of the
torsion angle (φ), the torque (Mx), the length of the
casing (l), the modulus of rigidity (G) and the polar
area moment (Ip) is shown in equation (1).
(1)
In most cases the shaft diameter, the external
torque, the material of the shaft and the possible
casing length are given values and cannot be
changed. Concerning the example of an 18mm
diameter steering shaft, a torsion angle φ from 0.05
to 0.06 degrees leads to a twist movement on the
shaft surface of 0.02mm. According to that point the
only way to achieve a maximum ∆x is to optimize
the design of the mechanical sleeve.
The simplified function model of the sleeve is a
two rod system with three revolute joints. Figure 4
shows the situation on a flat surface to demonstrate
the geometrical relationships more easily.
Figure 4: Simplified function model of the sleeve on a flat
surface.
Two rods with the length (a) are connected to
each other at joint (B) and to the surrounding at
joints (A) and (C) (see Figure 4a). The connection
points A and B are only moveable in the y-direction
but fixed in the x-direction. When the system gets
loaded due to a torque the points A and C move
contrarily along the y-direction (∆y
Mt) and hence the
joint B moves from its origin position along a
circular path with the radius (a) (see Figure 4b).
The geometrical relations in x-direction are
shown in Figure 4c and can be described in equation
(2).
(2)
From equation (2) it is obvious that the achieved
Δx is linear depending on the length (a) and
nonlinear to the geometric relation of Δy
M and the
width (b), the tilt angle of the system. But when the
two rod system gets wrapped around a cylinder
surface the interacting rod length will be scaled
down by the influence of the cylinder radius R as
shown in Figure 5.
Figure 5: Function model on a cylindrical surface.
Consequently to that effect the linear impact of
length (a) gets nonlinear according equation (3)
under the precondition that the distance (b) is very
short in relation to the radius (R) (b << R).
(3)
It is obvious that (a
1) has its maximum value
when (a) is the quarter of the cylinder
circumference, which is an important fact for the
geometry of the rotor rod elements.
3.2 FEM-Studies
Based on the kinematical principle the final CAD-
design has to be defined. The optimized shape of the
measuring sleeve (see Figure 1) is characterized by a
maximum Δx and a light structure with high
stiffness. Simulation helps to accelerate the
development process and to increase the quality of
the first prototype (Seiffert, 2008). The stresses in
critical regions near the revolute joint positions must
be under the fatigue limit of the chosen aluminium
alloy. The prototype sleeve is to be made as a
turning-milling part. Therefore the minimum cutting
CONTACTLESS TORQUE SENSOR - Mechatronic Principle and Prototype Development for Automotive Applications
57