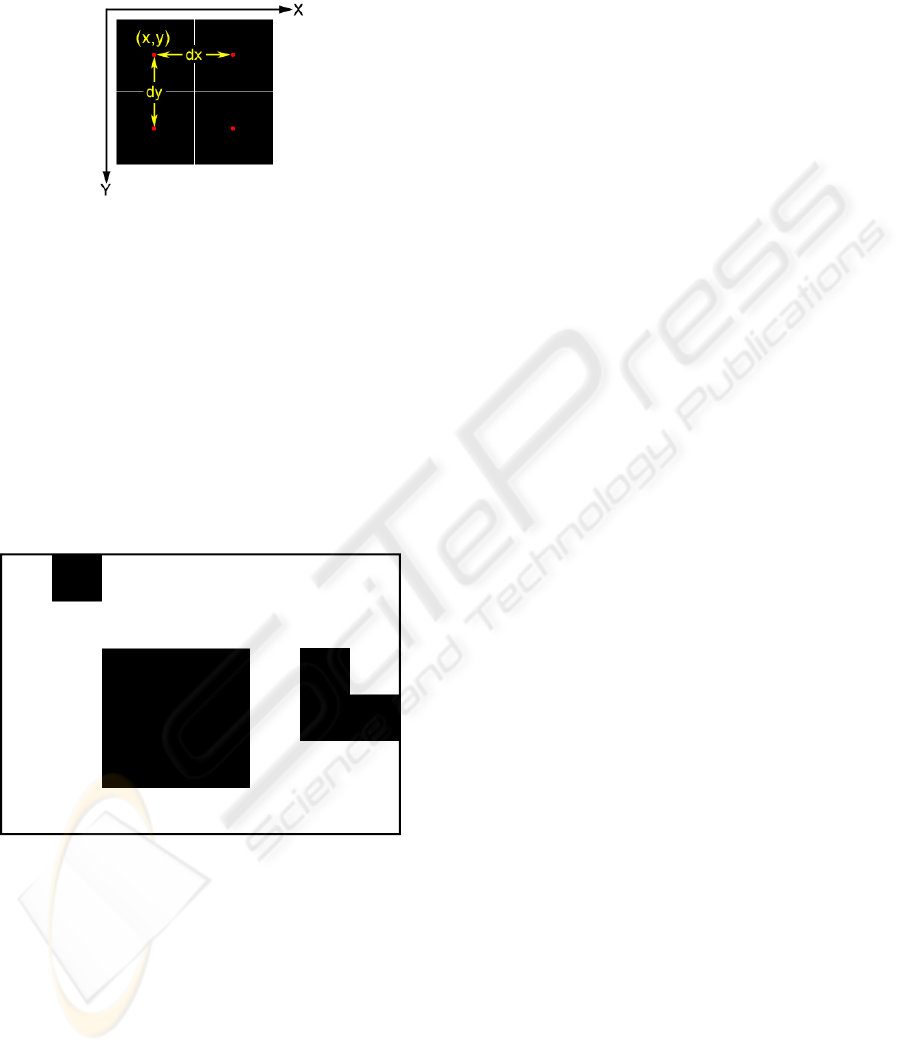
the centers of these two symbols is dx. Similarly, for
two adjacent symbols, which are arranged vertically,
it is dy.
Figure 13: Center of a macro pixel with horizontal and
vertical distance to its neighbours.
In order to detect the positions and size of the
existing obstacles in the workspace, a binary image
with the same resolution as the original grayscale
image is generated. The image is then divided into
regular blocks, where M is the number of
columns and N is the number of rows in the symbol
grid. All pixels within one block are assigned as "0"
(black), if the symbol represented by this block is
obscured by an obstacle, otherwise, the pixels are
assigned the value "1" (white). Figure 14 shows the
binary image generated for the example of Figure11.
Figure 14: Binary image showing occupancy of obstacles.
As the picture shows, there are three black areas,
which represent the positions of the obstacles. In
order to determine the size of the obstacles, the
contours of the areas are described as polygons. For
these polygons the Minimum Area Rectangles of the
obstacle regions (MAR) are then calculated
(Al Zeer, Nabout and Tibken, 2008). These regions
represent the workspace area occupied by the
present obstacles.
5 CONCLUSIONS
With the obstacle detection method presented here,
it is possible to detect existing obstacles in the
workspace of mobile robots. This method uses
grayscale images and a specially chosen reference
symbol. The results show that symbols with
irregular contour shape are not qualified to be used
as reference symbol, since the recognition process
leads to confusion with possible lighting errors and
other noise. The paper shows how to choose a good
reference symbol using a mathematical formula.
The method was developed for the detection of
obstacles in a robot vision system which is part of a
fully automated stockkeeping application. In this
context the results of the obstacle detection
described in this paper were also used for path
planning using auxiliary corners.
REFERENCES
Al Zeer, G., Nabout, A., Tibken, B., Path Planning for
Mobile Robots by Means of Approximate Routes,
2007 IEEE International Conference on Control and
Automation, Guangzhou, CHINA, May 30 to June 1,
2007, pp. 2468-2473.
Al Zeer G., Nabout, A., Tibken, B., Hindernisvermeidung
für Mobile Roboter mittels Ausweichecken, 52nd
Internationales Wissenschaftliches Kolloquium,
Technische Universität Ilmenau, 10.–13. Sep. 2007,
pp. 437-442.
Al Zeer, G., Nabout, A., Tibken, B., Extended Method for
Path Planning Using Auxiliary Corners, the 3rd IEEE
International Conference on Information &
Communication Technologies: from Theory to
Application, ICTTA'08, 7-11 April 2008, Damascus –
Syria.
Borenstein, J., Koren, Y., Real time obstacle avoidance for
fast mobile robots in cluttered environments. IEEE
Conf. Robotics and Automation, pp. 572-577, 1990.
Nabout A., Modulares Konzept und Methodik zur
wissensbasierten Erkennung komplexer Objekte in
CAQ-Anwendungen, 1993.
Simmons. R., The Curvature-Velocity Method for Local
Obstacle Avoidance. In Proc. IEEE Conf. Robotics
and Automation, 1996.
Sabe, K., Fukuch, M., Gutmann, J., Ohashi, T., Kawamoto
K., Yoshigahara, T., Obstacle Avoidance and Path
Planning for Humanoid Robots using Stereo
Vision.Proceedings of the International Conf. on
Robotics and Automation, ICRA'04, New Orleans,
April 2004.
Ulrich, I., Nourbakhsh, I., Appearance-Based Obstacle
Detection with Monocular Color Vision, Proceedings
of the AAAI National Conference on Artificial
Intelligence, Austin, TX, July/August 2000.
ICINCO 2009 - 6th International Conference on Informatics in Control, Automation and Robotics
444