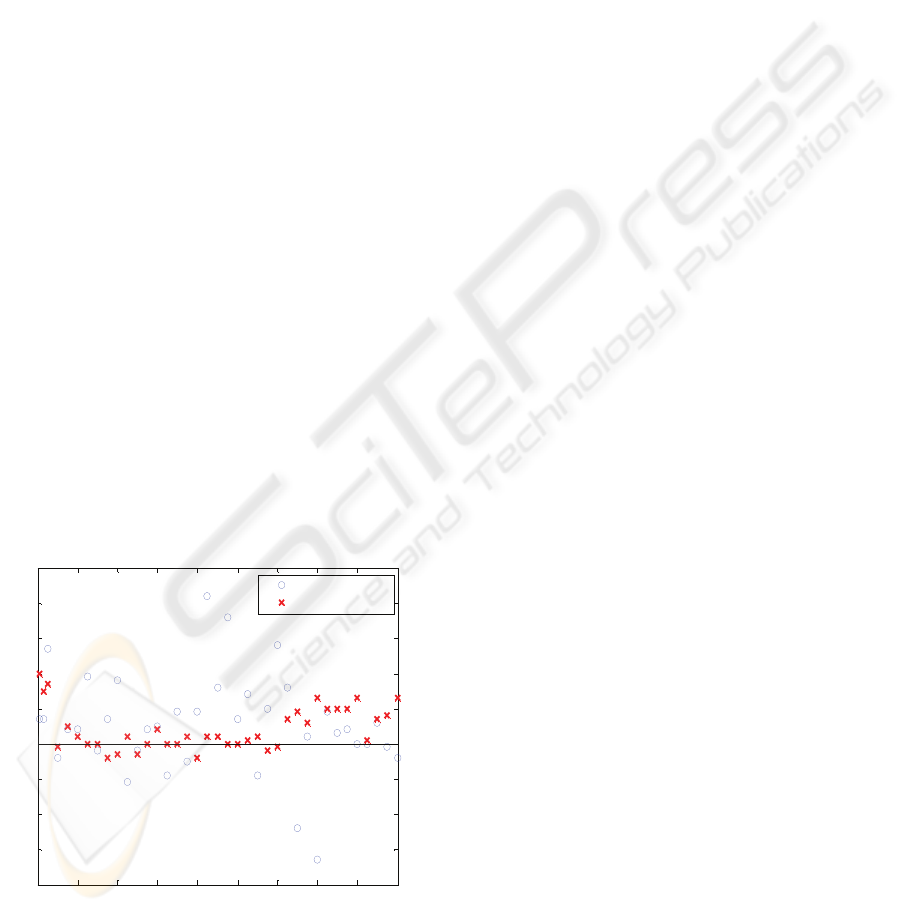
controller makes the mass M to reach its steady-state
position, the position error with the PI controller is
about 8,75 mm.
It was also carry out other experiences to study the
accuracy and repeatability of the overall control
system. Results are shown in Figures 10, which are
relative to the steady-state position error of the PI
and Hybrid Fuzzy-P+I control, respectively, when
were applied step signal references from 0 to
REF_signal mm (multiples of 5 mm, i.e., steps: 0 – 5
mm; 0 – 10 mm; …; 0 – 175 mm; 0 – 180 mm).
The worst steady-state position error of the PI
Control is 0,084 mm, but 3 times reaches below 2
µm of accuracy and 13 times reaches a accuracy
below 10 µm, although its average is 11 µm and
needs a long amount of time to reach these
accuracies. PI control can accurately control the
position of a pneumatic system, however it takes too
long. The sticking and restarting phenomena become
more evident when applied a step signal reference
from 0 to REF_signal mm where 80 mm ≤
REF_signal ≤ 140 mm.
The worst steady-state position error of the Hybrid
Fuzzy-P+I Control is 0,04 mm, but 7 times reaches
below 2 µm of accuracy and 18 times reaches a
accuracy below 5 µm, although its average is 8,6
µm. This controller has achieved a diminution in the
overshoot and in the steady state error compared
with PI and FP controllers, although it suffers some
late correcting the position error. The FP controller
has the shortest rise time and reaches early the
steady-state position. With FLC, with or without the
hybrid solution, the sticking and restarting
phenomena was not observed.
0 20 40 60 80 100 120 140 160 180
-0.08
-0.06
-0.04
-0.02
0
0.02
0.04
0.06
0.08
0.1
Edge: 0 - REF Signal (mm)
Step Position Error (mm)
PI Control
Fuzzy P+I Control
Figure 10: Steady-state position error of PI and Hybrid
Fuzzy-P+I Control when step references from 0 to
REF_signal mm were applied.
9 CONCLUSIONS
The present paper describes the design and control
of a pneumatic press to perform controlled tracking
of positional reference trajectories. The control
system of the servo pneumatic machine was
implemented with LabVIEW using CompactRIO®
hardware. Conventional PI, proportional Fuzzy and
Hybrid Fuzzy-P+I control strategies were compared
in the position control of a moving mass over 200
mm course. The Hybrid Fuzzy-P+I Controller
provides the best performance for the performed
position control experiments: short rise time, small
overshoot and a steady-state position error that can
reach the encoder resolution, less than 2 µm. It has
particularly advantageous in terms of simplicity of
design and implementation. There is an ongoing
work to implement a high performance force
controller using FLC and the overall pneumatic
system simulation with Matlab/Simulink
®
platform.
REFERENCES
Carneiro, J., Almeida, F., 2006. Modeling Pneumatic
Servovalves using Neural Networks, Proceedings of
the 2006 IEEE Conference on Computer Aided
Control Systems Design, pp. 790-795, Munich,
Germany.
Carneiro, J., 2007. Modelação e Controlo de Actuadores
Pneumáticos Utilizando Redes Neuronais Artificiais,
PhD Thesis in Mechanical Engineering, University of
Porto, Portugal.
Ferreira, J., Sun, P. Grácio, J., 2006. Design and Control
of a Hydraulic Press, Proceedings of the 2006 IEEE
Conference on Computer Aided Control Systems
Design, pp. 814- 819, Munich, Germany.
Liu, H., Lee, J., Li, B., 2007. High Precision Pressure
Control of a Pneumatic Chamber Using a Hybrid
Fuzzy PID Controller, International Journal of
Precision Engineering and Manufacturing, Vol. 8, No.
3, pp. 8-13.
Pai, K., Shih, M., 2003. Nanoaccuracy Position Control of
a Pneumatic Cylinder Driven Table, JSME Int’l
Journal, Series C, Vol. 46, No. 3, pp. 1062-1067.
Passino, K., Yurkovich, S., 1998. Fuzzy Control, Addison
Wesley Longman, Menlo Park, CA.
Santos, M., Talaia, P., Ramos, A., Ferreira, J., Oliveira,
M., 2008. Servo-Pneumatic Machine to Perform and
Monitor Tests on Biomechanical Devices, Controlo
2008: Proceedings of the 8
th
Portuguese International
Conference on Automatic Control, pp. 784 – 789, Vila
Real, Portugal.
Xiang, F., Wikander, J.,2004..Block-oriented Approximate
Feedback Linearization for Control of Pneumatic
Actuator System, Control Engineering Practice 12(4),
pp. 6113-6119.
POSITION CONTROL OF A SERVO-PNEUMATIC SYSTEM - Hybrid Fuzzy P+I Controller of a Servo-Pneumatic
Fatigue Simulator
239