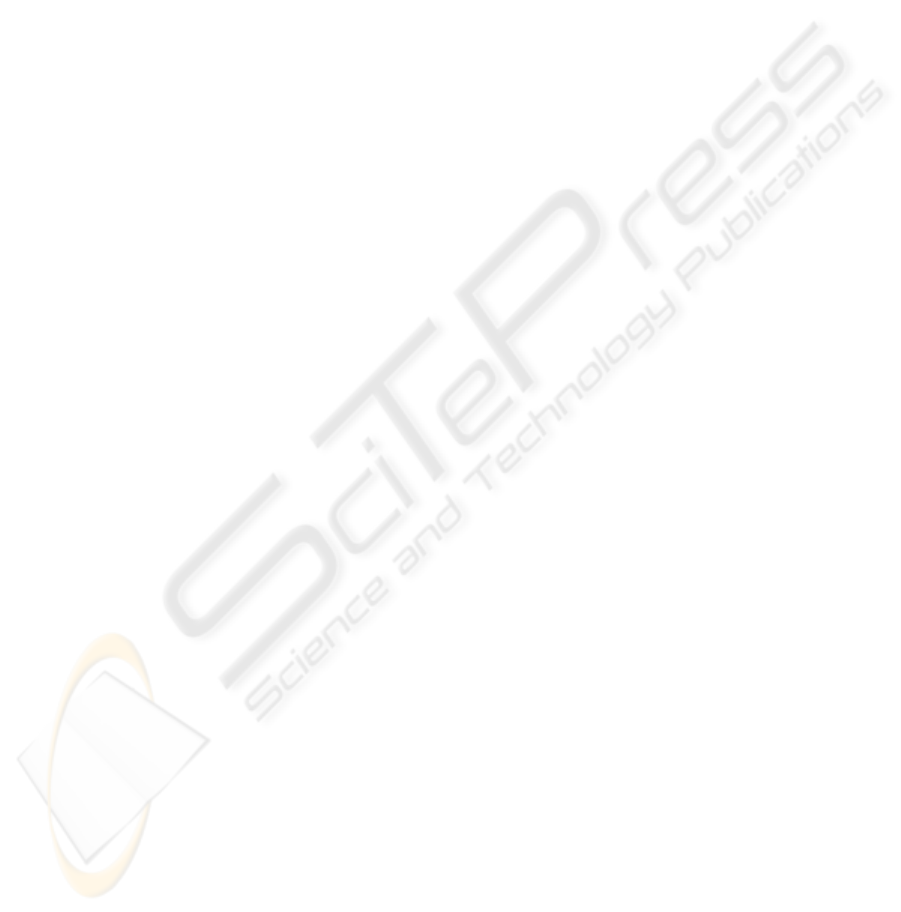
ment head is a linear array of spindles.
In the revolver-head gantry machine the PCB to
be manufactured is kept on the table at a fixed loca-
tion. The placement head of the machine moves in
the (x, y)-plane on the PCB and the feeder unit. The
placement head is also called revolver-head or even
an arm. It picks up the neccessary components from
the feeder unit that is located on the side (or sides) of
the machine and then mounts them on the PCB.
The placement head is moved by three step mo-
tors which run independently. The first one moves
the whole gantry on its rails (in x-direction). The sec-
ond motor moves the revolver-head on the gantry (in
y-direction) and the third motor is used to rotate the
revolver-head.
The revolver-head is equipped with multiple spin-
dles, typically 6-12. Each spindle can hold a noz-
zle which can grab a component. There are many
different types of component nozzles. Each compo-
nent type requires a compatible nozzle. The shape of
a component defines what type of nozzle should be
used for grabbing it. It is also possible that a certain
nozzle type is compatible with several different com-
ponent types.
The feeder unit is divided into a set of feeder slots
of fixed width (typically 8 mm). The slots are loaded
with component tapes in which the components are
stored one after the other. There are only components
of the same type in each tape. Usually, the dimen-
sions of the components are notably smaller than 8x8
mm and they fit a 8 mm tape. However, there are also
wider components which are supplied in wider tapes,
for example 16 mm. These tapes occupy more than
one feeder slots but their use is similar to that of nar-
row tapes.
At a high abstraction level, revolver-head gantry
machines operate in cycles of four phases:
1. pick-up-phase
2. travel onto the PCB -phase
3. placement-phase
4. travel onto the feeder -phase
While there are slight differences in the opera-
tion principles of different machines, we consider a
case, where the design of the machine includes the
following details: In the first phase, the revolver-head
moves on the feeder unit and collects one component
after the other from the right feeder slots keeping the
component tapes. Between two pick-up events the
revolver-head has to rotate at least one step to get
an empty nozzle operable. It is also possible that the
revolver-head has to move in the x-direction (which is
parallel to the length of the feeder unit) onto a correct
feeder slot. The revolver can rotate while it is mov-
ing to the next pick-up location. In the pick-up-phase,
we suppose that the revolver never rotates more than
360
◦
and it can leave one or more nozzles empty by
skipping them during the pick-ups.
After at least one component has been picked up
the placement head moves onto the PCB area. This
is called travel onto the PCB -phase. During this
movement, the revolver rotates so that the component
which was picked up first in the pick-up-phase can
be placed immediately after the head has reached the
placement location.
In the placement-phase, the collected components
are placed onto the PCB in their correct locations in
the same order as they were picked up. The rotation
limit of 360
◦
concerns this phase, also. Finally, the
empty revolver-head is moved back onto the feeder
unit and rotated so that the suitable nozzle for the next
component to be picked up is operable again.
If for example 180 components have to be placed
on a single PCB the gantry machine with revolver
spindle count of 12 makes at least 15 tours described
above. However, this requires that all the nozzles are
loaded in every single tour. In practice, it is usually
impossible to get full loads because of component-
nozzle incompatibilities. If the next nozzle in the re-
volver is not compatible with the next component that
should be picked up, the revolver is rotated more than
one step forward.
There are placement machines that can change
nozzles automatically during the manufacturing pro-
cess but in many cases the change-process takes
too much time and it is therefore avoided. On the
otherhand, in some placement machines the nozzle
changes can be done only manually and the placement
process has to be stopped for doing that.
A setup operation (i.e. change of component tape
reels, conveyor belt adjustment etc.) of the placement
machine must be performed before the machine can
manufacture any new PCB types. At least the follow-
ing decicions have then to be made:
1. assign the component types into the slots of the
feeder unit,
2. define the set of component nozzles and their or-
der in the revolver-head, and
3. define the sequence and tours in which compo-
nents are picked up and placed.
It has been commonly assumed in previous liter-
ature that each nozzle can grab any type of compo-
nent exist, so there has not been a need to solve the
nozzle selection for the revolver-head. However, the
situation is often more complicated in practice. The
consideration of the nozzle-component compatibility
ICINCO 2009 - 6th International Conference on Informatics in Control, Automation and Robotics
76