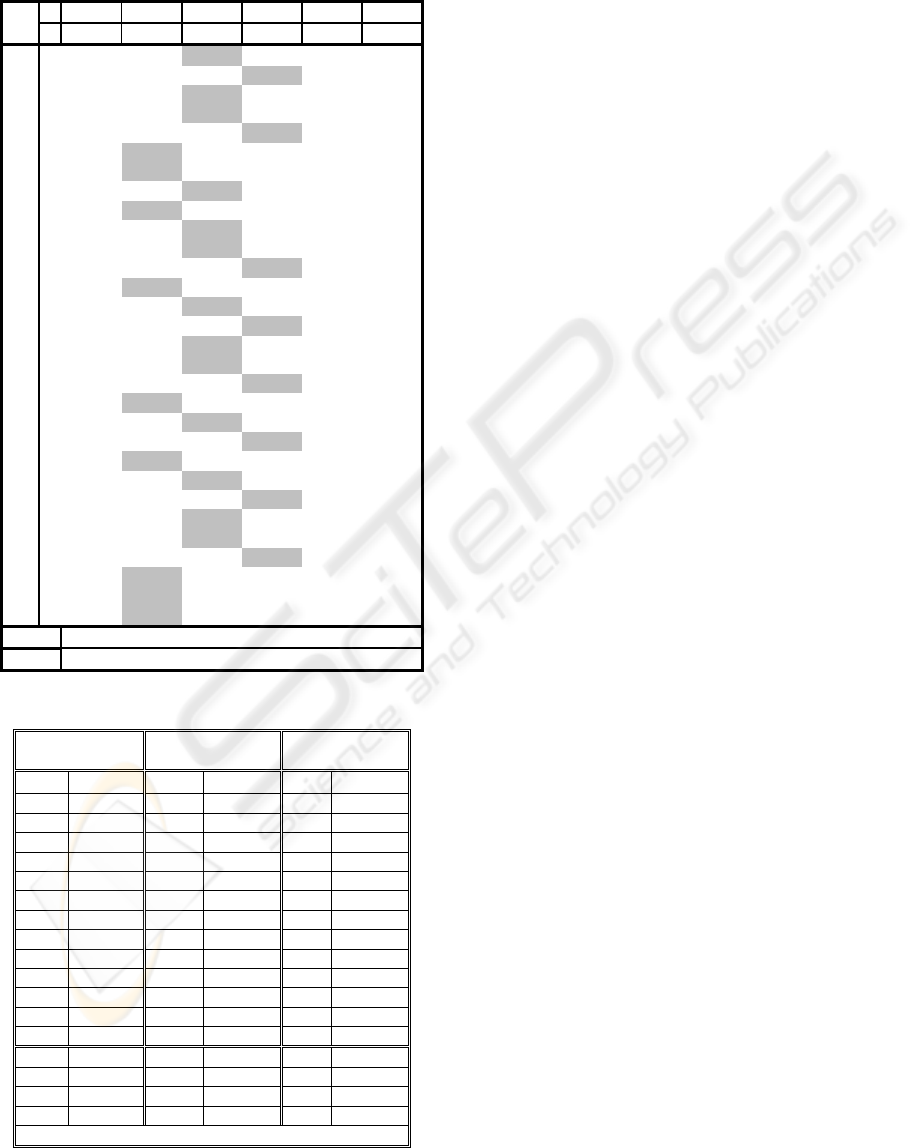
or (N=4, γ=0.3655) may be chosen as the best (near-
optimal) PM policy.
Table 3: The results of the 30 Simulation runs.
Run#
N 1 2
3
4 5 6
γ 1 0.6667
0.4781
0.3655 0.2957 0.2483
1 216.730 189.894
180.155
194.132 194.575 210.016
2 229.144 196.101 192.570
187.925
210.093 194.498
3 250.869 196.101
189.466
197.236 213.197 206.912
4 250.869 186.790
180.155
200.340 188.368 213.120
5 204.315 199.205 204.984
187.925
219.404 197.602
6 263.284
189.894
201.880 194.132 197.679 197.602
7 213.626
165.065
183.259 197.236 185.264 203.809
8 232.248 214.723
192.570
194.132 206.990 194.498
9 241.558
177.480
183.259 200.340 191.472 206.912
10 216.730 189.894
180.155
194.132 188.368 206.912
11 219.833 211.619
204.984
209.650 213.197 216.223
12 222.937 189.894 189.466
181.718
197.679 197.602
13 247.766
177.480
180.155 209.650 197.679 216.223
14 247.766 196.101
180.155
206.547 197.679 203.809
15 198.108 196.101 189.466
181.718
200.782 194.498
16 216.730 192.998
183.259
200.340 185.264 203.809
17 226.040 205.412
189.466
191.029 194.575 206.912
18 195.004 202.308 211.191
191.029
210.093 191.394
19 216.730
183.687
186.362 191.029 200.782 213.120
20 226.040 199.205
183.259
203.443 200.782 206.912
21 232.248 186.790 189.466
184.822
194.575 203.809
22 204.315
196.101
198.777 197.236 197.679 200.705
23 207.419 186.790
180.155
206.547 188.368 206.912
24 210.522 208.516 195.673
187.925
206.990 197.602
25 219.833 205.412
195.673
203.443 197.679 213.120
26 257.076 192.998
173.948
215.858 191.472 219.327
27 216.730 211.619 195.673
172.407
210.093 188.291
28 216.730
189.894
201.880 200.340 197.679 216.223
29 210.522
168.169
180.155 206.547 191.472 216.223
30 247.766
186.790
189.466 187.925 197.679 200.705
Avg. 225.316 193.101
189.569
195.891 198.92 204.843
Theo. 221.495 191.076
189.728
192.850 197.222 202.051
Table 4: The near-optimal Policies of the Simulation.
Policy 1
(N
*
=2, γ
*
=0.6667)
Policy 2
(N
*
=3, γ
*
=0.4781)
Policy 3
(N
*
=4, γ
*
=0.3655)
Run# Min. TC Run# Min. TC Run# Min. TC
6 189.8940 1 180.1552 2 187.9252
7 165.0652 3 189.4660 5 187.9252
9 177.4796 4 180.1552 12 181.7180
13 177.4796 8 192.5696 15 181.7180
19 183.6868 10 180.1552 18 191.0288
22 196.1012 11 204.9840 21 184.8216
28 189.8940 14 180.1552 24 187.9252
29 168.1688 16 183.2588 27 172.4072
30 186.7904 17 189.4660
20 183.2588
23 180.1552
25 195.6732
26 173.9480
Runs 9 Runs 13 Runs 8
Avg. 181.6177 Avg. 185.6462 Avg. 184.4337
Max. 196.1012 Max. 204.9840 Max. 191.0288
Min. 165.0652 Min. 173.9480 Min. 172.4072
Overall average of min. TC: 184.1143
5 CONCLUSIONS
The proposed three simulation methods are not
significant different in generating the time-between-
failure RVs .for the PM model with age reduction.
The rejection method seems simple and easy to use
in practical.
For the infinite time span, the results from the
simulation method are very close to those obtained
by the theoretical model. However, for a finite time
span, more than one near-optimal policy can be
obtained by the simulation method. Each of the
near-optimal solution can be the best PM policy for
any single system having a finite life time period.
The simulation results have demonstrated that the
theoretical PM model might not always suitable for
a single system in a finite time span.
The simulation method can be applied in solving
more complicated real world situation, such as the
consideration of the random shock in a PM model,
which is difficult to be solved by the theoretical
model.
ACKNOWLEDGEMENTS
This research has been supported by the National
Science Council of Taiwan under the project number
NSC96-2221-E-324-010.
REFERENCES
Cheng, C.-Y. and Liaw, C.-F., 2005. Statistical estimation
on imperfectly maintained system, European Safety &
Reliability Conference 2005 (ESREL 2005), Jun. 27-
30, 2005, Tri-City, Poland, pp 351-356.
Cheng, C.-Y. Liaw, C.-F., and Wang, M., 2004. Periodic
preventive maintenance models for deteriorating
systems with considering failure limit, 4
th
International Conference on Mathematical Methods in
Reliability—Methodology and Practices, Jun. 21-25,
2004, Santa Fe, New Mexico.
Murthy, D. N. P. and Nguyen, D. G., 1981. Optimal Age-
Policy with Imperfect Preventive Maintenance, IEEE
Transactions on Reliability Vol.R-30, No.1, pp.80-81.
Pongpech, J. and Murthy, D. N. P., 2006. Optimal
Periodic Preventive Maintenance Policy for Leased
Equipment, Reliability Engineering & System Safety,
Vol.91, pp.772-777.
Ross, S. M., 1997. Simulation, Academic Press, San
Diego, pp.62-85.
Yeh, R. H. and Chen, C. K., 2006. Periodical Preventive-
Maintenance Contract for a Leased Facility with
Weibull Life-Time, Quality & Quantity, Vol.40,
pp.303-313.
ICINCO 2009 - 6th International Conference on Informatics in Control, Automation and Robotics
330